
Large-format 3D printing is playing an increasingly important role in the construction industry. By means of the additive manufacturing process, in particular complex and customized components can be manufactured with material and cost savings, can be freely designed and, if thermoplastic base materials are used, can be excellently recycled. As a result, completely new, highly efficient construction elements are also conceivable and feasible. In collaboration with research and industry partners, we are developing a sustainable material on the basis of biopolymers and natural fibers for large-format 3D printing. In doing so, we are enabling modern, sustainable architectural solutions.
The project is focused on the production of the 3D components by means of the extrusion-based 3D-printing process “Fused Deposition Modeling (FDM)” with short and continuous-fiber filaments on the basis of natural fibers. The utilization of this technology in architecture is targeted at two different application purposes:
1. Simplified production of established components
The objective is for established architectural components – which, up until now, have required many manufacturing steps – to be produced using faster, simpler and more adaptable manufacturing processes. The focus thereby lies on components which, due to their design or function, exhibit a high degree of individualization and complexity – for example, façade elements, free-form furniture items and partition walls as well as multifunctional components.
2. Novel, highly efficient building components
A further objective is the development of completely new types of architectural components which cannot be produced by means of conventional manufacturing processes. One conceivable example would be a load-bearing ceiling element whose topology is adapted to the static load. This would allow slender ceiling structures with minimal material requirements.
In both cases, the components should be made as extensively as possible from renewable raw materials.
The primary task of the Fraunhofer WKI is the development of the bio-based filaments for the production of components for interior construction and façade elements using the FDM process. A particular challenge hereby is the production of uniform and spoolable filaments that can be easily extruded.
Short-fiber filaments
The matrix polymers to be used include polylactic acid (PLA) and biopolyamides. By means of compounding, we reinforce the polymers with regionally available wood fibers and cellulose fibers. These should improve the thermal dimensional stability of PLA and reduce shrinkage of the components.
Continuous-fiber filaments
The continuous fibers (natural fibers) should enable the production of structurally more durable components. We are developing a process for the coating of regionally available flax and hemp fibers with thermoplastic biopolymers.
Multi-material 3D printing
We optimize short-fiber and long-fiber-reinforced filaments with respect to processing in multi-material 3D printing. As a result, the specific advantages of the different materials can be combined in a targeted manner within a single component.
Additivation
Components are subject to high requirements such as durability, UV stability and flame retardancy. In order to achieve these, we equip the biopolymers with suitable additives.
Evaluation and characteristics
The printed samples are evaluated in terms of their uniformity and we determine their properties (mechanics, flame retardancy, etc.).
Social relevance
Previous research into additive manufacturing in construction has focused on conventional material systems such as 3D-printing of concrete – regardless of the environmental impact. Concrete requires vast amounts of finite resources as well as manufacturing and transportation energy. In addition, chemical reactions during cement production release large quantities of CO2. Furthermore, concrete components can only be recycled to a limited extent.
Thermoplastic biocomposites, in contrast, are made from renewable, often regionally available raw materials and are significantly lighter. This saves resources and energy. In addition, components made from thermoplastic biocomposites can be melted down at the end of their useful life and then processed to form new components.
Biocomposites have already proven themselves as suitable, sustainable building materials for exterior applications, for example in façade construction. Until now, however, standardized profiles have been produced which have to be subsequently shaped. With this project, we are creating the possibility of producing customized large-format components from biocomposite materials in accordance with specific requirements by means of 3D-printing processes. This is not only more efficient but also significantly expands the architectural leeway. Biocomposites could therefore be increasingly utilized in the construction industry in the future, thereby replacing less sustainable materials. Furthermore: Through the production of novel, highly efficient lightweight components, the ecological footprint of a building can be additionally reduced.
Economic advantages
If the project is successful, architectural studios, construction companies and building owners could benefit from expanded design options when building with renewable raw materials.
For the forestry and agricultural industries as well as manufacturers of biocomposites, new business opportunities could be opened up.
Project partners
- Institute of Building Structures and Structural Design (ITKE) at the University of Stuttgart (project coordination)
- Laserzentrum Hannover
- Rapid Prototyping Technologie GmbH
- ETS Stange
- 3dk Trading GmbH
- ATMAT Sp. z o.o.
Funding
Official project title:
Design und Fabrikation von 3D-gedruckten Bauteilen aus Biokompositen / Filamenten aus Endlos- und Kurzfasern; Teilvorhaben 2: Materialentwicklung und Herstellung von Filamenten
(Design and fabrication of 3D-printed components made from biocomposites / filaments of continuous and short fibers; Subproject 2: Material development and production of filaments)
Funding body:
German Federal Ministry of Food and Agriculture (BMEL)
Project administration:
Fachagentur Nachwachsende Rohstoffe e. V. (FNR)
(Agency for Renewable Resources)
Funding reference: 2220NR295B
Duration: 1.7.2021 to 31.12.2023
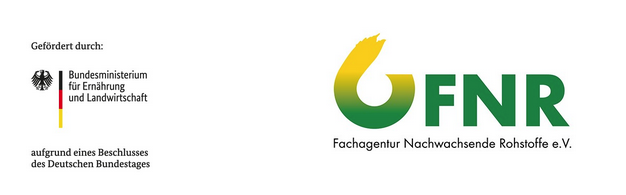
Source
Fraunhofer WKI, press release, 2021-07-01.
Supplier
3dk.berlin
ATMAT Sp. Z o.o.
Bundesministerium für Ernährung und Landwirtschaft (BMEL)
Fachagentur Nachwachsende Rohstoffe e.V. (FNR)
Fraunhofer-Institut für Holzforschung Wilhelm-Klauditz-Institut WKI
Institut für Tragkonstruktion und Konstruktives Entwerfen (ITKE)
Laser Zentrum Hannover e.V. (LZH)
RPT - Rapid Prototyping Technologie GmbH
Share
Renewable Carbon News – Daily Newsletter
Subscribe to our daily email newsletter – the world's leading newsletter on renewable materials and chemicals