The nova-Institute conducted a peer-reviewed Life Cycle Assessment (LCA) of Avantium’s PEF (polyethylene furanoate) applications within the framework of the European PEFerence project. The study demonstrated that the use of 100 % renewable carbon in PEF instead of fossil carbon in PET for producing 250 ml and 500 ml bottles would result in significant reductions in greenhouse gas (GHG) emissions. Avantium plans to start-up the world’s first commercial FDCA plant in 2024. FDCA (2,5-furandicarboxylic acid) is the main building block of PEF.
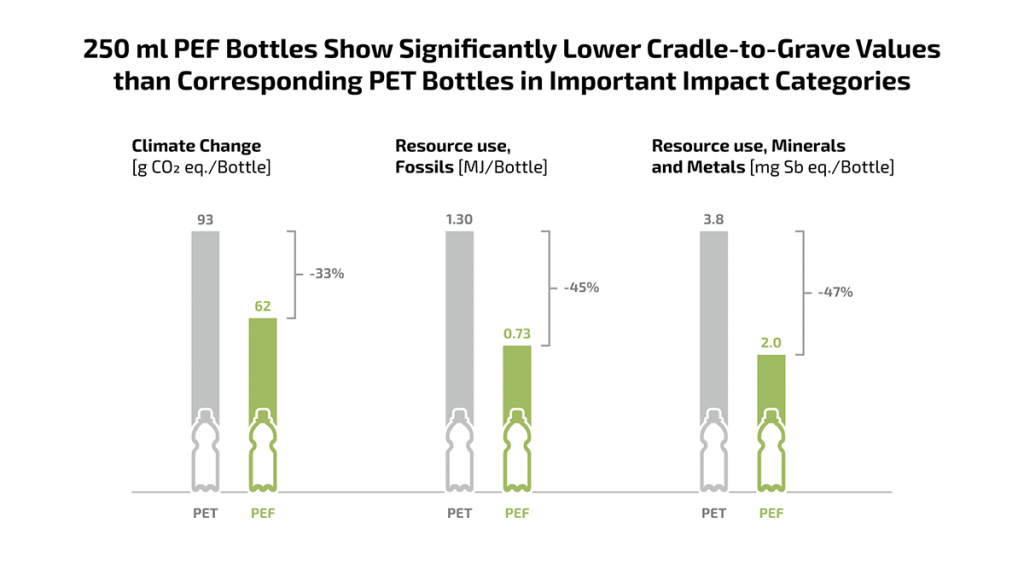
CO2 is absorbed by plants and released at the end of the product life cycle. Plant-based carbon has a net-neutral impact on the CO2 concentration in the atmosphere. In contrast to this, materials and polymers based on fossil carbon from underground, release additional CO2 into the atmosphere.
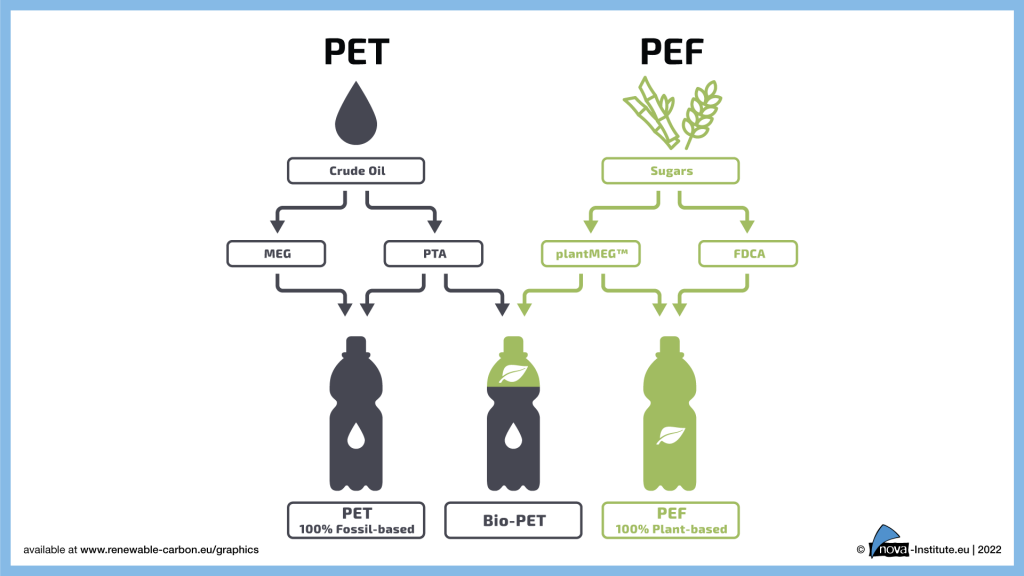
The Dutch company Avantium has developed a technology (YXY®) to convert plant-based sugars into a fully recyclable polymer. The new 100 % bio-based polymer, PEF (polyethylene furanoate) has superior performance properties compared to PET (polyethylene terephthalate). The main building block of PEF, FDCA (2,5-furandicarboxylic acid) can be produced from sugars (fructose), for example from wheat, corn and sugar beet. FDCA is polymerised with plant-based mono-ethylene glycol (MEG) to make a 100 % plant-based PEF polymer. When fully technologically developed, PEF can also be produced from cellulose and thus from agricultural and forestry waste streams. Avantium’s current process utilises starch from European wheat. PEF has enhanced barrier properties compared to PET, it is mechanically and chemically recyclable and can also be recycled within the established PET recycling. PEF has a 12 °C higher heat resistance than PET, a 60 % higher modulus and greater strength than PET. This allows the developing of lightweight packaging from PEF with lower resource requirements. Avantium has already implemented this innovative, plant-based packaging material on a pilot scale and recently started the construction of a 5,000-tonnes-per-year FDCA flagship plant in Delfzijl (the Netherlands). The nova-Institute’s peer-reviewed LCA indicates a significant reduction potential in greenhouse gas emissions and use of fossil resources of PEF compared to PET.
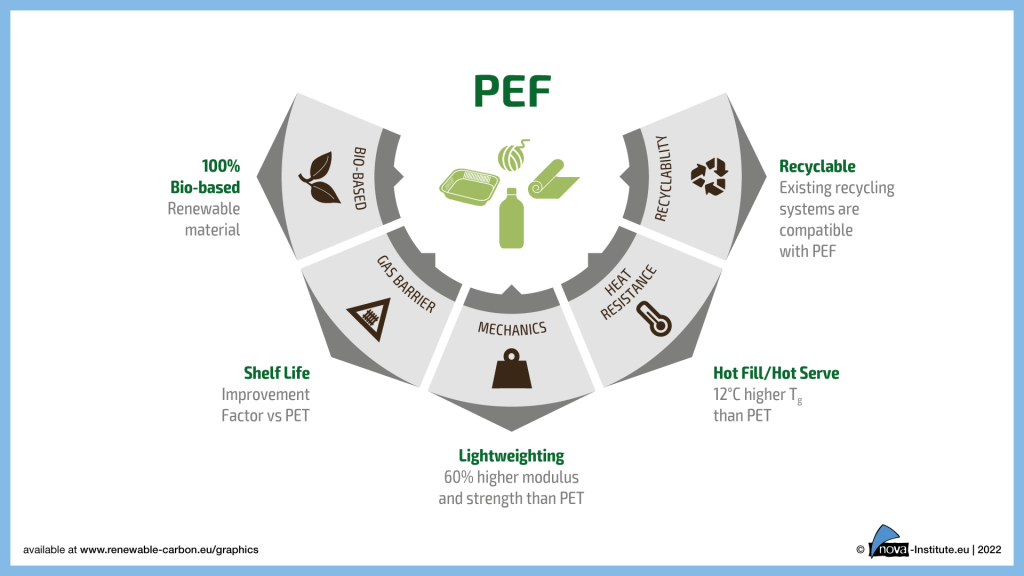
Results of the LCA
The nova-Institute performed a peer-reviewed full cradle-to-grave LCA according to the ISO standards 14040/44. A critical peer-review of the study, including experts of LCA methodology and incumbent packaging solutions, verified that the LCA met the requirements for methodology, data, interpretation, and reporting.
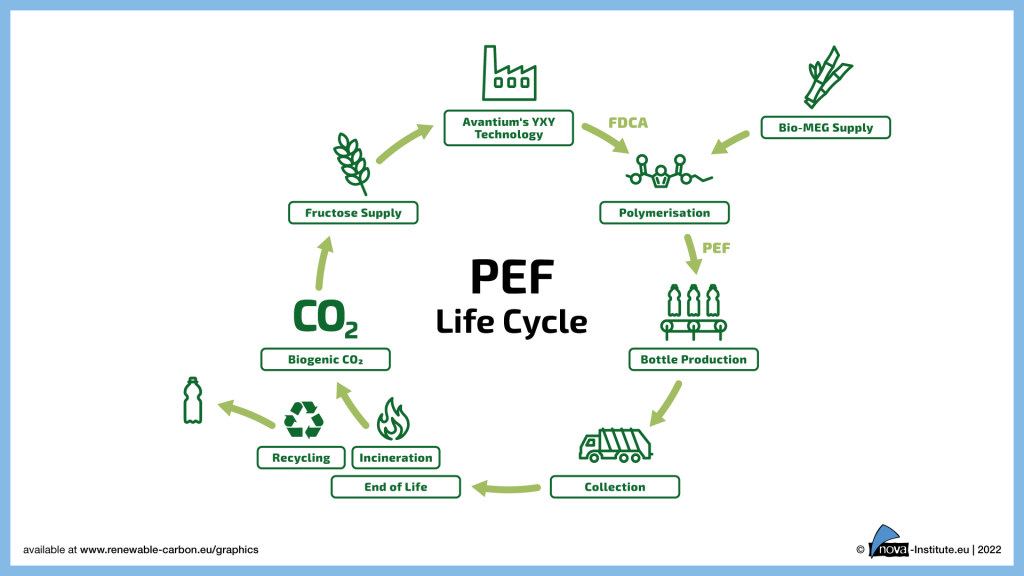
The LCA evaluated 16 different impact categories covering all relevant life cycle stages from cradle-to-grave. The comparative analysis showed that PEF bottles would result in significant reductions in greenhouse gas emissions (-33 %) compared to reference PET bottles. PEF would also lead to 45 % lower finite resource consumption of fossil fuels and reduce the pressure on abiotic resources (minerals and metals) by 47 % due to the mechanical properties of PEF enabling light-weighting. However, PET bottles would outperform PEF-bottles in other impact categories mostly arising from the current feedstock supply. Overall, this represents a benefit because climate change and resource use are among the most relevant environmental impact categories in the current political agenda. They are driving the transition from fossil to renewable carbon.
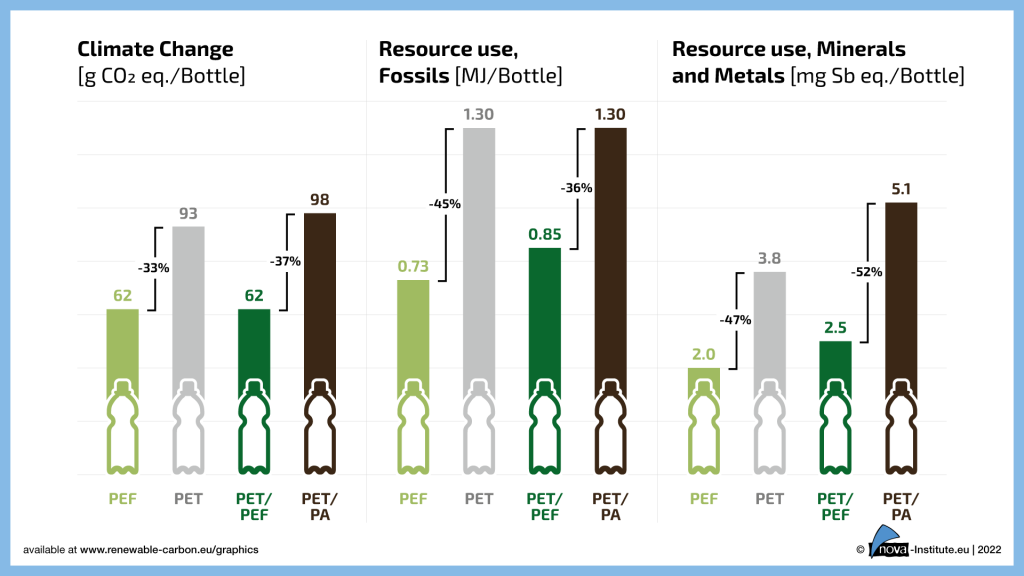
Multilayer bottles
In addition to monolayer PEF bottles, PEF can also be used for multilayer packaging. Multilayer bottles can be an option when the required shelf life cannot be guaranteed by monolayer packaging. PEF offers a good passive barrier for O2 and CO2 and could potentially contribute towards reducing the environmental footprint of packaging solutions by increasing the shelf life of products, enabling a reduction in the weight of packaging, and by improving recyclability.
In this LCA, 250 ml PET/PEF multilayer bottles with 10 % of PEF were also assessed and compared to reference PET/PA bottles with a typical 7 % of PA (polyamide). The analysis showed that significant reductions of around 37 % in GHG emissions could be achieved by replacing the PA layer with PEF, mainly attributed to the recyclability of the PET/PEF system over the non-recyclability of the PA-containing system. This replacement would also contribute to a significant reduction of finite resources demand (-37 % and -52 % of fossil fuels and minerals and metals, respectively).
Development potential
PEF is a relatively new material and not yet commercially available. PET is a conventional product that has been on the market for over 40 years and is produced in a highly established process that runs close to maximum efficiency at a very large scale. It is expected that the commercialisation and growth of the PEF market will lead to substantial economic, technological, and environmental optimisations covering the full value chain. The impact originating from the plant-based feedstock could also be further reduced by a switch to lignocellulosic feedstocks such as second-generation biomass. This will be tested at Avantium Renewable Polymers in the framework of the BBI-JU PEFerence project, and should confirm that the YXY® process can use second-generation biomass when it becomes available at commercial volumes and pricing. An update of the LCA is planned afterwards.
Funding
The PEFerence project receives funding from the Bio-based Industries Joint Undertaking (JU) under the European Union’s Horizon 2020 research and innovation programme under grant agreement No 744409. The JU receives support from the European Union’s Horizon 2020 research and innovation programme and the Bio-based Industries Consortium.
More information about the PEFerence project can be found at www.peference.eu.
A more detailed report on the LCA is available at www.renewable-carbon.eu/publications.
Source
nova-Institut GmbH, press release, 2022-08-31.
Supplier
Avantium Technologies B.V.
Bio-based Industries Consortium (BIC)
Circular Bio-based Europe Joint Undertaking (CBE JU)
European Union
nova-Institut GmbH
Share
Renewable Carbon News – Daily Newsletter
Subscribe to our daily email newsletter – the world's leading newsletter on renewable materials and chemicals