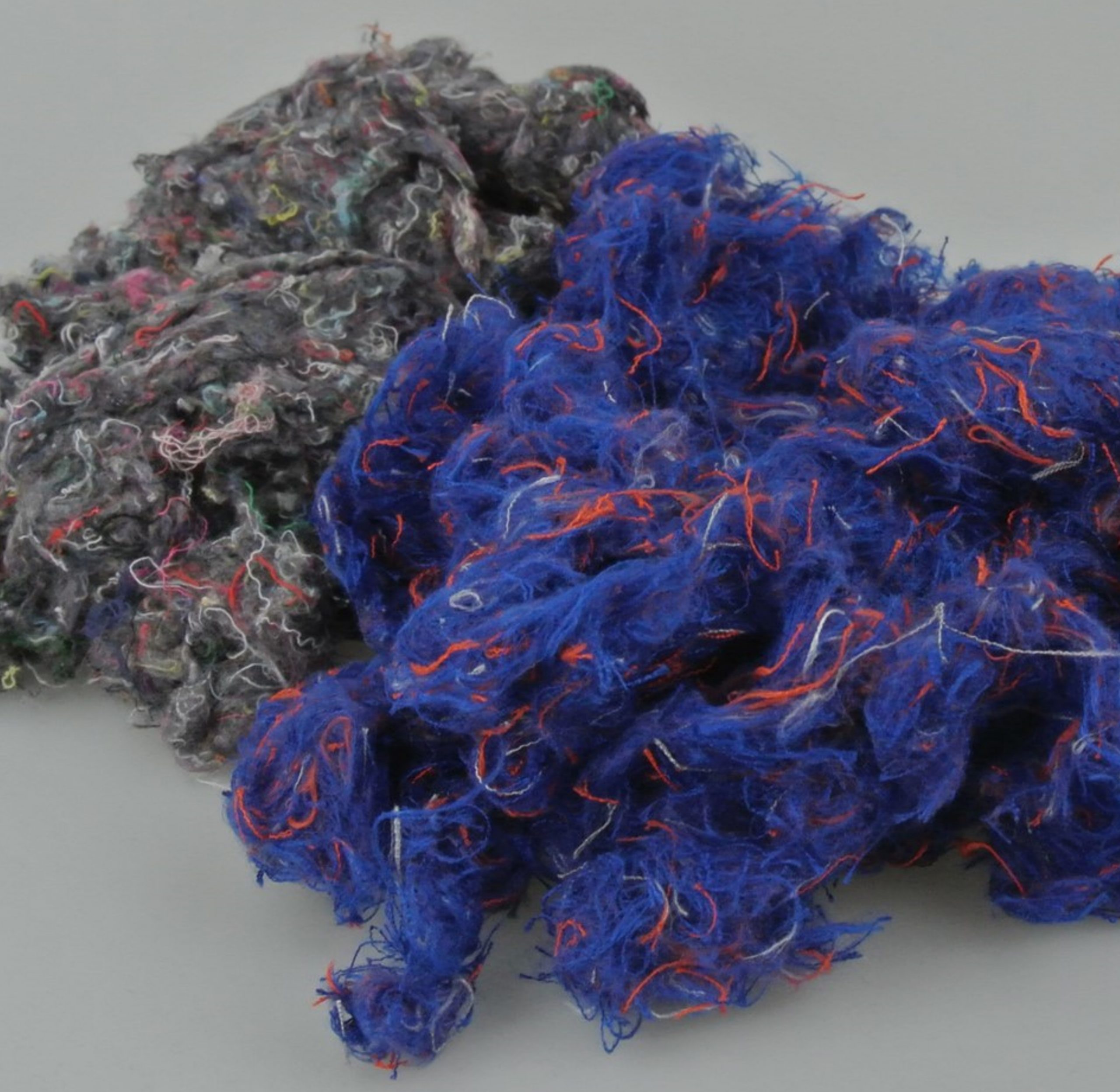
Sustainability was the leading theme of this year’s ITMA textile machinery trade show. Almost all exhibitors in Milan showed new technologies for textile recycling. However, it is demanding to obtain high-quality yarns from used textiles and to process them into equally high-quality products. The appropriate technological solutions are not yet available for all the challenges. Ultimately, it is a matter of finding the right processes for each material. The German Institutes of Textile and Fiber Research Denkendorf (DITF) and the Saxon Textile Research Institute (STFI) have developed a new test routine for this purpose.
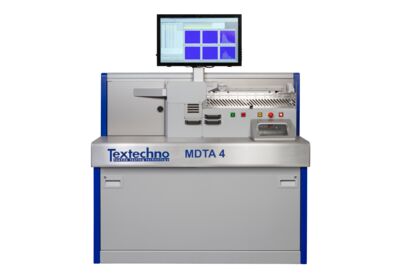
The recycling process begins with mechanical tearing, which involves shredding the used textiles. In most cases, the procedure damages the fibers. Individual fibers get too short, which makes the subsequent spinning process more difficult. In order to be able to optimally adjust the tearing machines, the fibers are classified after shredding. For this purpose, the researchers developed a new test routine, which was carried out with a special measuring device. Fiber length is the most important parameter for further processing of the fibers and for the quality of the finished yarn made from recycled fibers. Pieces of yarn still in the torn material are always longer than the fibers themselves and thus distort the fiber length measurement. With the test setup, pieces of yarn still present can be broken up almost without further fiber shortening. Thus, an exact measurement of the fiber length distribution of the torn recycling material is possible.
Based on the test results, the tearing parameters can be better adjusted to the material so that the fibers are less shortened during the tearing process. In this way, higher quality yarns can be produced. The characteristic values of the optimum recycled material, which are determined using a statistical method, were also used to find the suitable recycled product to be spun out and the optimum settings and spinning agents for the spinning process.
The recycled materials were then processed into ring and rotor yarn. In practice, the ring yarn was best produced using the compact spinning process. This process allows the already short recycled fibers to be much better integrated. As a result, the yarn gains in strength.
With the new test routine and the resulting optimized processes, it was possible to produce yarns from 100 percent recycled aramid fibers, which were then further processed into knitted fabrics. Since aramid fibers are very expensive, the process reduces costs, saves raw materials and contributes to greater sustainability. Cotton fibers were also spun in a blend of 80 percent virgin fibers and 20 percent recycled material. After completion of the project, the recycled content of cotton could be increased to up to 70 percent.
In the textile industry, there is often skepticism as to whether closed cycles, i.e. cradle to cradle, are possible. Some even question whether it would not be just as sustainable to burn the used textiles and use the resulting heat as an energy source.
The research work of DITF and STFI, on the other hand, shows that it is possible to reprocess 100 percent of recycled material. However, the yarns must be used in a product-oriented manner, which means that not every yarn made from recycled fibers is suitable for every application. This is because the tearing process inevitably leads to losses in the quality of the fibers, for example in yarn strength.
The quality of the starting material is also decisive for the quality of the yarn made from recycled fibers. If the recycled textile consists of different materials, these must first be laboriously separated. Again, straw cannot be spun into gold.
“The recycling rate is an important purchase criterion, but one has to keep an eye on the quality of the product and the application,” concludes Markus Baumann, a scientist working on the project.
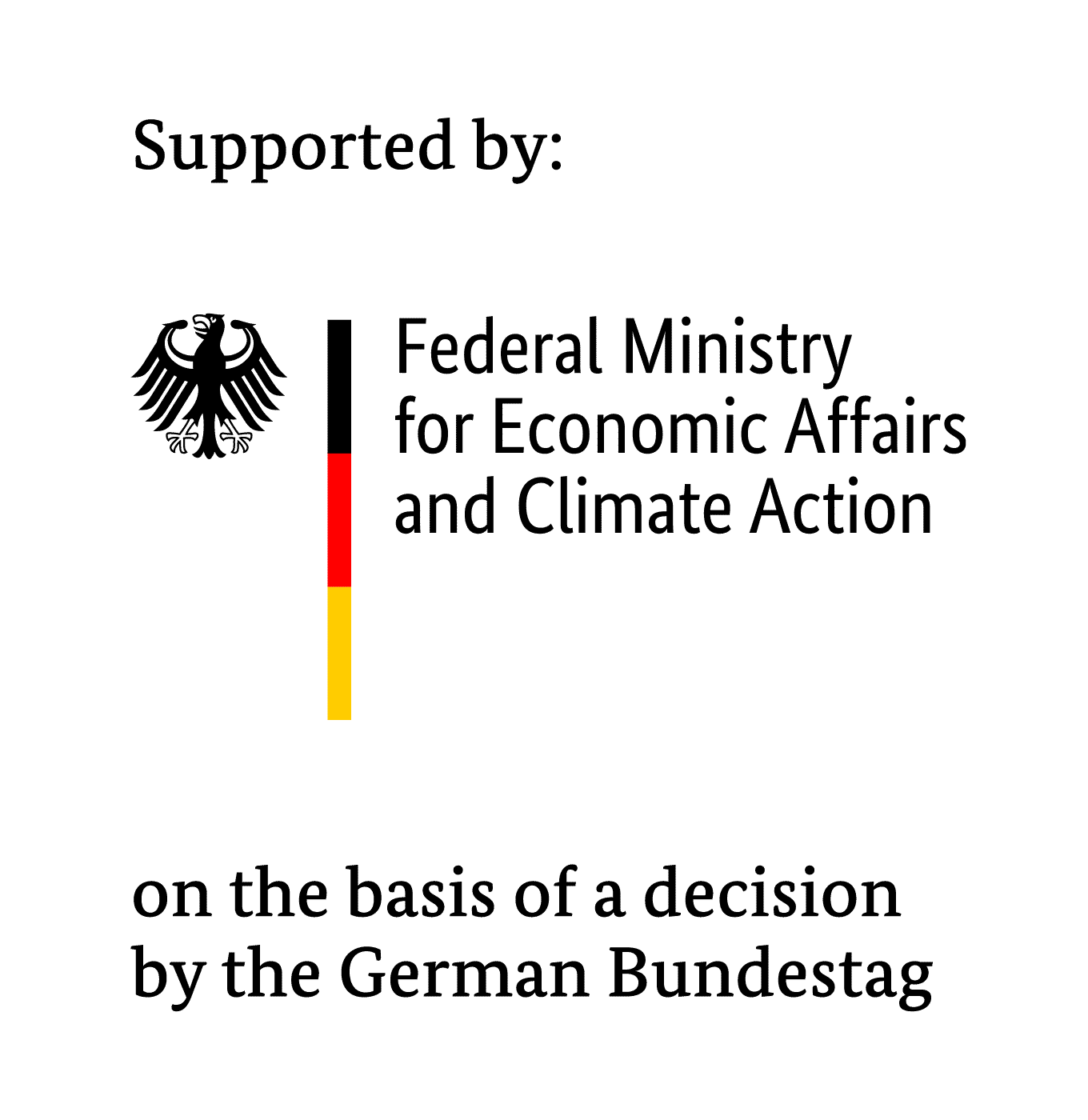
The IGF project 21286 BG/1 of the Research Association Forschungskuratorium Textil e.V., Reinhardtstraße 14-16, 10117 Berlin, was funded by the Federal Ministry of Economics and Climate Action via the AiF as part of the program to promote joint industrial research (IGF) on the basis of a resolution of the German Bundestag.
Source
DITF, press release,2023-08-30.
Supplier
Arbeitsgemeinschaft industrieller Forschungsvereinigungen “Otto von Guericke” e.V. (AiF)
Bundesministerium für Wirtschaft und Klimaschutz (BMWK)
DITF – Deutsche Institute für Textil- und Faserforschung Denkendorf
Textechno - Textile testing technology
Share
Renewable Carbon News – Daily Newsletter
Subscribe to our daily email newsletter – the world's leading newsletter on renewable materials and chemicals