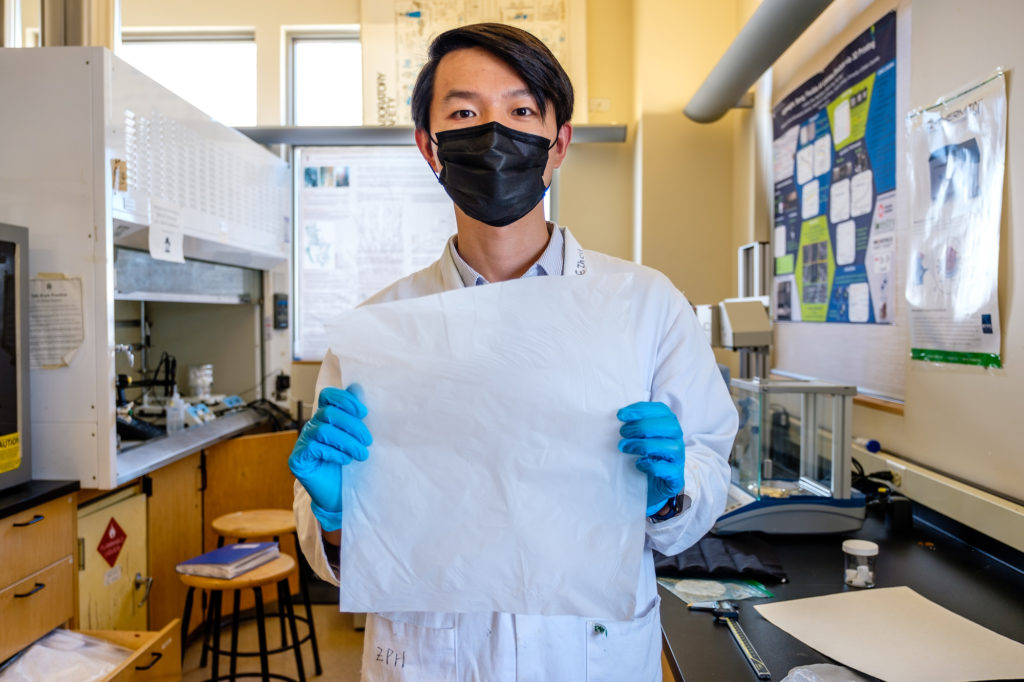
How it’s made
Dr. Jiang’s process breaks down wood fibres (sourced from forest waste) in a solution of cold sodium hydroxide combined with mild mechanical blending. The sodium hydroxide is then recycled. The result is a translucent, strong and water-resistant film.
Other researchers have also developed cellulosic films but the UBC project—funded by the Ministry of Forests, Lands, Natural Resource Operations and Rural Development—is the first to use small amounts of energy and chemicals in the manufacture.
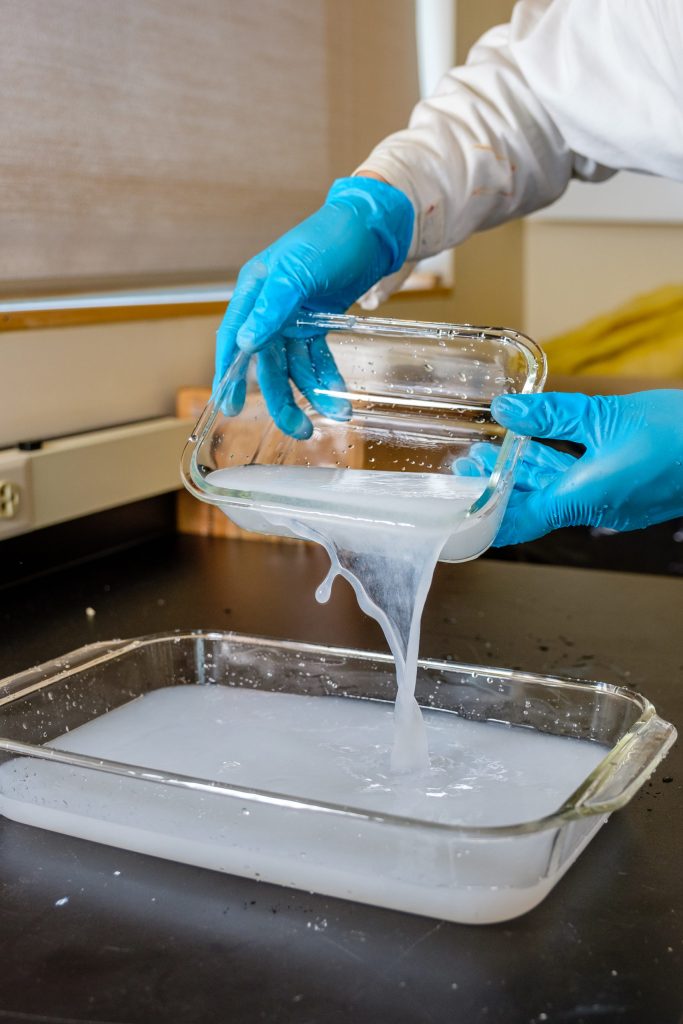
What it’s good for
Like conventional plastic, the film can be made into coffee bags or chip bags, pouches like pouches for cereal or frozen fruit, or protective wrap like bubble wrap or envelopes.
The difference is that at the end of its life cycle, the cellulose film can be buried in the ground or an organics bin, where it will break down within three weeks.
Why it matters
With certain plastics taking up to a million years to decompose, single-use plastic is a massive source of pollution and it also uses significant amounts of toxic chemicals during manufacture. Dr. Jiang and his team hope to bring their film to market within a few years to offer an alternative that is environmentally friendly and marks a new use for forest byproducts.
Contact
Steph Troughton
UBC Forestry
Cell: 604-362-7706
Email: stephanie.troughton@ubc.ca
Author
Lou Corpuz-Bosshart
Source
University of British Columbia, press release, 2022-09-23.
Supplier
University of British Columbia
Share
Renewable Carbon News – Daily Newsletter
Subscribe to our daily email newsletter – the world's leading newsletter on renewable materials and chemicals