An interdisciplinary team of researchers from the Max Planck Institute of Colloids and Interfaces (MPICI) has investigated how the natural properties of native tree bark can be used to create a standardized product for long-term use without the addition of adhesives. In doing so, they have created bark panels by peeling and drying via hot pressing, which could be used in interior design or furniture and packaging, for example, through industrial production.
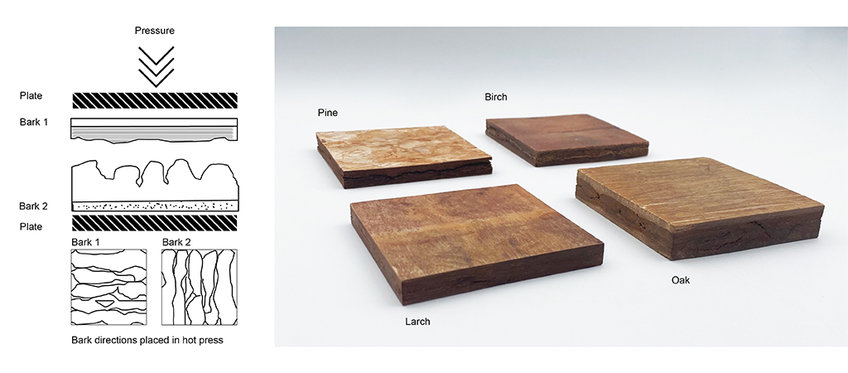
With this processing method, the natural resource of tree bark could be further processed without the addition of artificial binders, such as adhesives, and without high energy expenditure.
“A major advantage of ‘pure’ single-component products is that there is no need to separate the components after they have been used,” says Dr. Charlett Wenig, first author of the study. She adds, “Even if the structure of the raw material is changed, the basic building blocks remain the same and can therefore still be readily used for further processing, such as obtaining chemicals or fibers, or as fuel for energy production.”
As a waste product of the timber industry, tree bark is available in large quantities. First, the bark must be peeled from the trunk and then dried. In the experiments, the scientists pressed the insides of the barks with a hydraulic press at 90 degrees Celsius. They used bark from the native tree species pine, larch, birch and oak. After pressing, all the bark panels produced in this way had a smooth surface comparable to sanded wood surfaces. The mechanical properties of the boards are comparable to those of a shelf board.
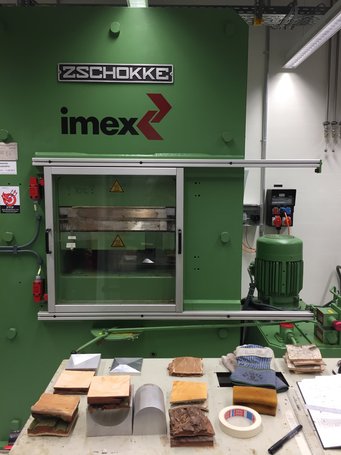
What is new? Previously, pure bark particle boards were made with the addition of formaldehyde-based adhesives or resins. As early as 1960, studies showed that it was possible to produce adhesive-free bark boards, but by using shredded bark pieces and by heavy processing. In the MPICI trials, researchers are taking advantage of the natural structural properties of the barks.
Partners: Eberswalde University of Applied Sciences (Department of Forest Utilization and Wood Market) and ETH Zurich (Wood Materials Science).
Original publication
Charlett Wenig, Friedrich Reppe, Nils Horbelt, Jaromir Spener, Ferréol Berendt, Tobias Cremer, Marion Frey, Ingo Burgert, Michaela Eder; Adhesives free bark panels: An alternative application for a waste material; PLOS ONE, 23 January, 2023; https://dx.doi.org/10.1371/journal.pone.0280721
Source
Max-Planck-Institute of Colloids- and Interfaces, press release, 2023-01-27.
Supplier
Eidgenössische Technische Hochschule Zürich (ETH Zürich)
Hochschule für nachhaltige Entwicklung in Eberswalde (HNEE)
Max-Planck-Institut für Kolloid- und Grenzflächenforschung
Share
Renewable Carbon News – Daily Newsletter
Subscribe to our daily email newsletter – the world's leading newsletter on renewable materials and chemicals