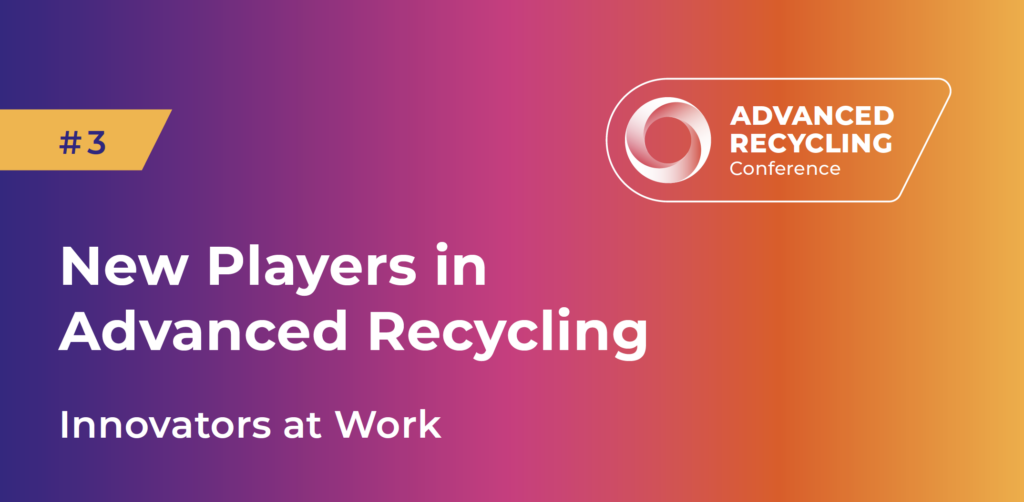
The Advanced Recycling Conference
The Advanced Recycling Conference 2024 is just around the corner, and is set to be a hub of innovation and progress in the recycling sector. This year, nova-Institute is thrilled to spotlight the pivotal role that smart and dynamic startups play in driving advanced recycling technologies.
Many of these innovative startups will be showcasing their pioneering solutions, including cutting-edge advancements like DePoly unique PET recycling technology. Their patented continuous reactor is critical for breaking down PET waste into its base chemical monomers, which can then be purified and repurposed into new PET. With environmentally sustainable and economically viable solutions, DePoly is making it easier for their innovations to be applied at an industrial scale in order to lead the charge towards a more sustainable and circular economy.
Read more about it in our interview series “New Players in Advanced Recycling – Innovators at Work” with DePoly CSO & Co-Founder Christopher Ireland.
The unique concept of presenting all advanced recycling solutions and related topics at one event will guarantee a comprehensive and exciting conference experience, including technologies such as extrusion, dissolution, solvolysis, enzymolysis, pyrolysis, thermal depolymerisation, gasification, and incineration with Carbon Capture and Utilisation (CCU).
This year’s Advanced Recycling Conference will take place on 20-21 Novemeber 2024 in Cologne, Germany and online.
1. Innovation & Sustainability
How does DePoly’s chemical recycling technology help reduce plastic waste and promote sustainability? Can you share specific examples where this has had a significant environmental impact?
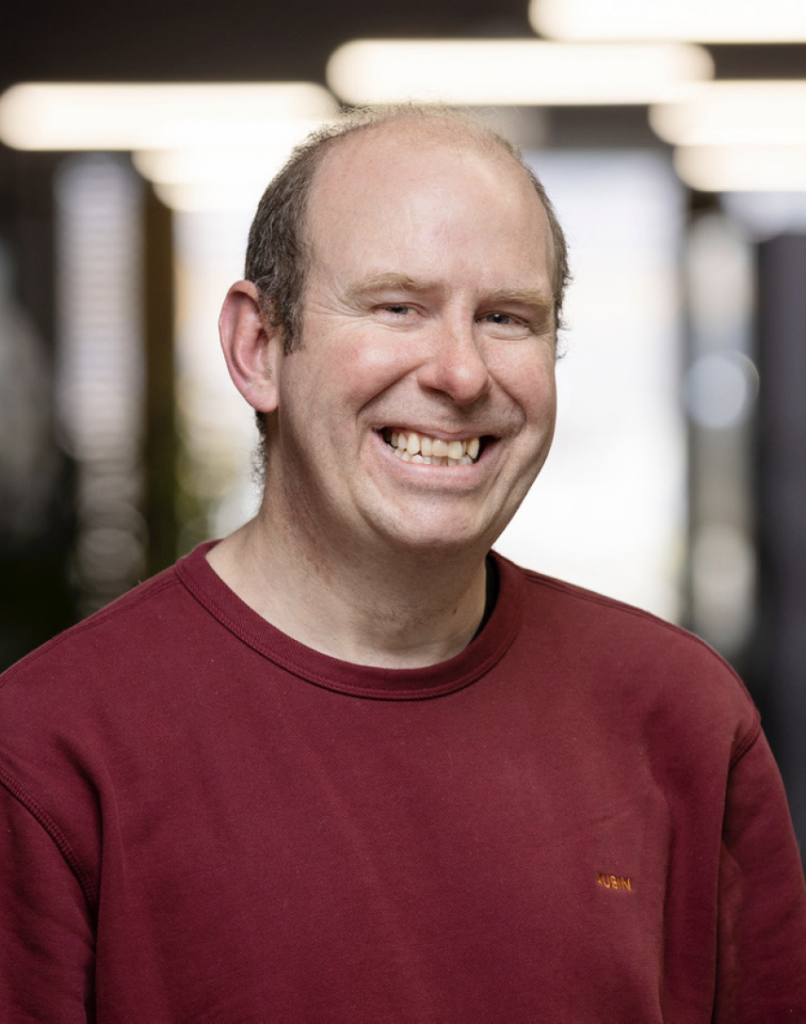
Dr. Christopher Ireland: Our technology recycles PET plastic into its monomers of purified terephthalic acid and mono ethylene glycol using sustainable chemicals that can be found at home, and no additional heat or pressure. Our technology targets PET specifically, meaning we can handle mixed plastic, contaminated waste, both post-industrial and post-consumer waste and polyester containing textiles – no sorting is required. We therefore compliment mechanical recycling by targeting waste that isn’t currently recycled. A recent project involved taking waste that was rejected from the recycling system, and with partners, developing it into a jar that could be used for cosmetics – something we are all very proud of.
2. Breakthrough Technology
What breakthrough technologies form the groundwork of Depoly’s recycling process, and how have they improved both efficiency and environmental outcomes compared to traditional mechanical methods?
Dr. Christopher Ireland: Our core tech was developed in the lab towards the end of 2018; initially testing water bottles, we saw the monomers being produced, so then went on to test any PET based product we could think of, from shampoo bottles, peanut butter containers to one of my shirts. We built a pilot plant in 2021, validating our process with various PET products at scale, and recently started construction of our Showcase Plant in Monthey, Switzerland. Along the way, we’ve developed innovative ways of purifying and forming the monomers using sustainable chemicals and as little energy as possible. This allows us to avoid recrystallisation with organic solvents and helps lower our environmental footprint. Unlike mechanical methods, we are not restricted in our feedstock, which allows us to compliment mechanical methods as opposed to replacing them.
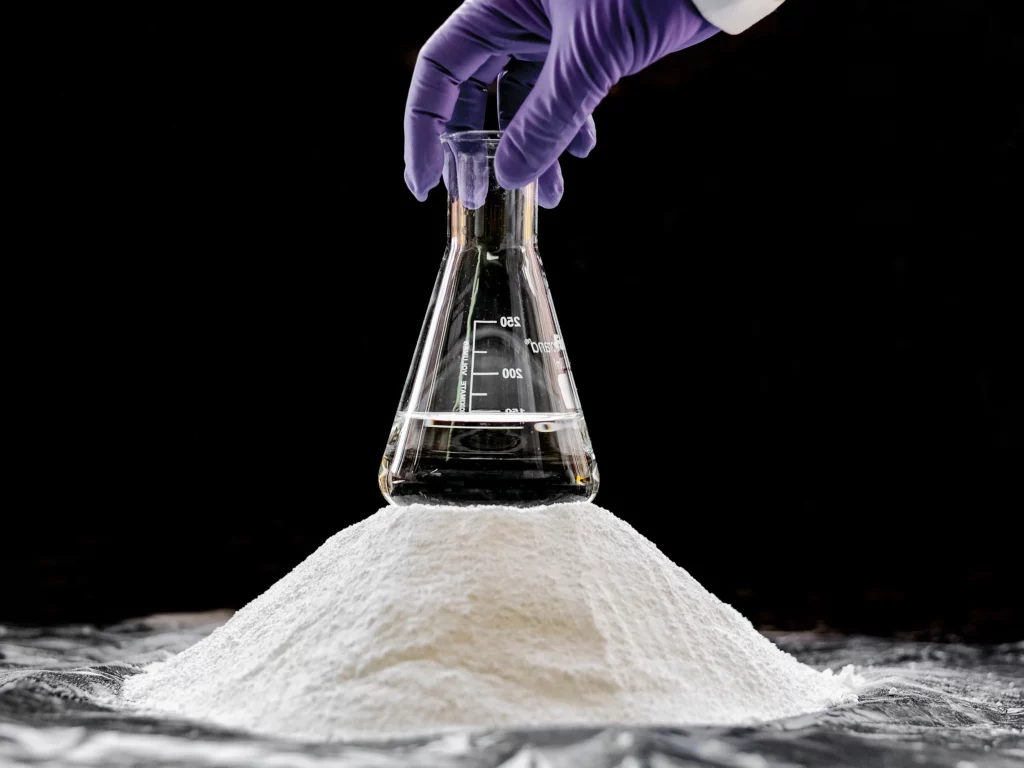
3. Challenges & Opportunities
What have been the biggest challenges in scaling your recycling operations, and what opportunities in the industry have been key to DePoly’s growth?
Dr. Christopher Ireland: We have a strong engineering and R&D team which has allowed us to scale from grams, to kilograms, to our showcase plant which will begin operations in 2025, handling tonnes. Our core technology of recycling the PET uses a patented continuous reactor; the rest of the process uses off the shelf equipment such as filters, shredders etc. A key challenge is ensuring the equipment works well and compliments each other when the plant is built. We still have a strong R&D focus, but we limit our research to ensure all the innovations needed to be at scale are both environmentally and economically viable; although this is restrictive, it also allows us to produce stunning innovations.
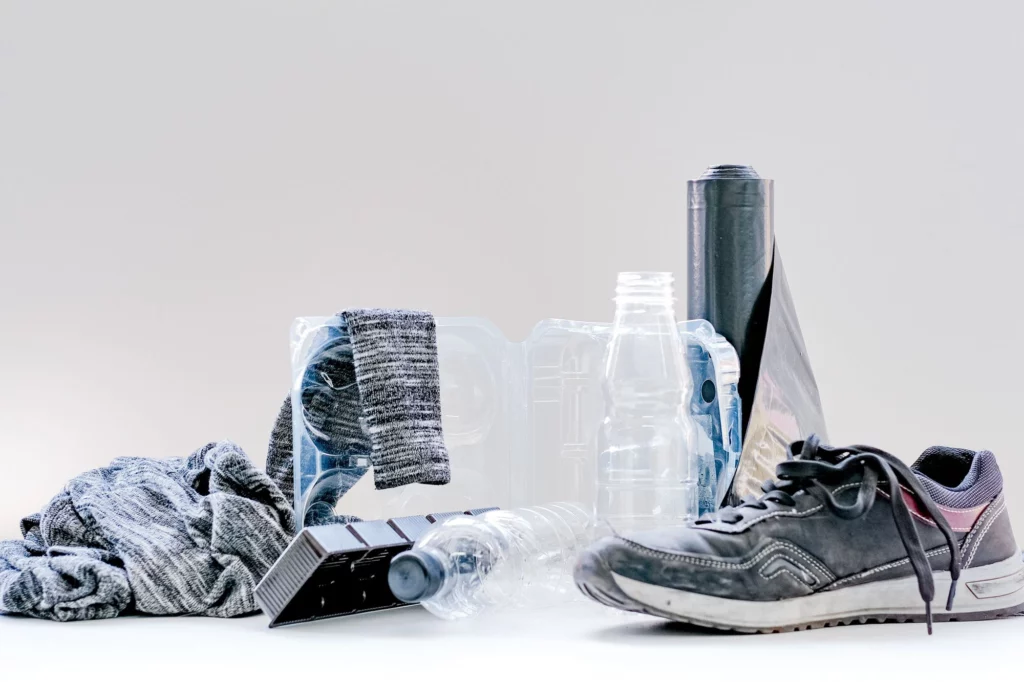
4. Collaboration & Industry Dynamics
Can you elaborate how partnerships with other companies or sectors have helped DePoly expand its impact, and what types of new collaborations are you seeking to further your mission?
Dr. Christopher Ireland: We completed our seed round last year, led by BASF and Founderful VC; Beiersdorf, Syensqo and Qemetica are also investors amongst others. This gives us exceptional scope, with traditional venture capital firms, chemical manufacturers and brands all helping with our strategy and focus as we scale. We can take unwanted PET waste, sell chemicals for PET polymerisation, or complete the circle and with partners, create the PET again from the initial feedstock. We therefore are looking at partnering waste collectors (post-consumer and post-industrial) PET manufacturers and brands, wanting to create circularity.
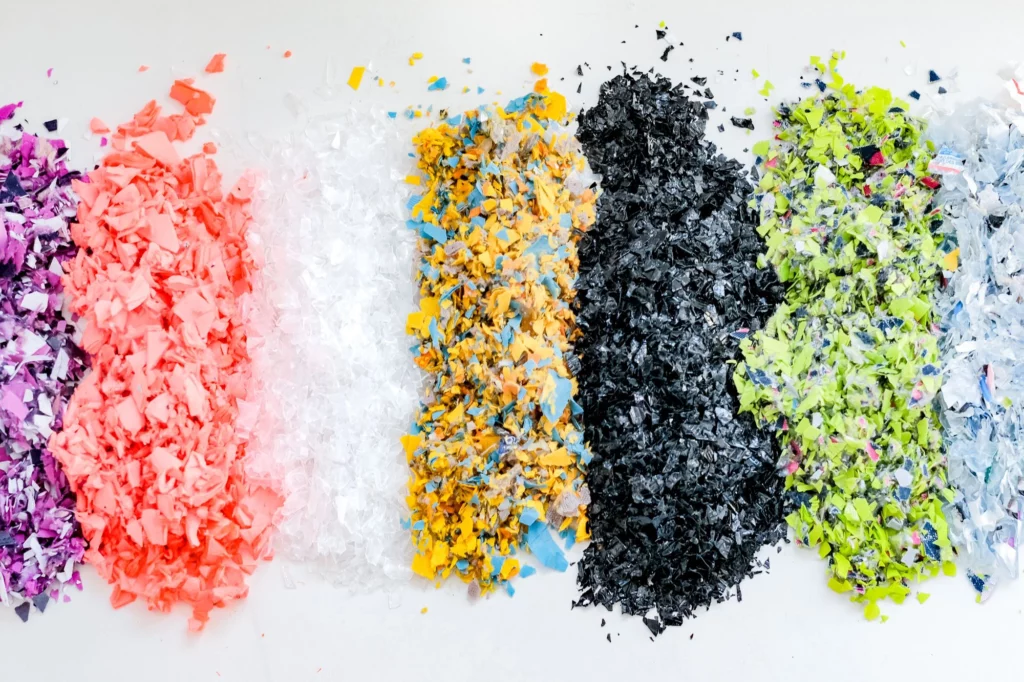
5. Future Innovations
Looking ahead, what advancements or innovations is Depoly focusing on to enhance the efficiency and scalability of your technology?
Dr. Christopher Ireland: We are continually improving our core tech, and really excited for next year to see our Showcase Plant up and running in Monthey, Switzerland. The next step is to start building our First of a Kind Plant (FOAK) – we are already starting the planning of this. Our goal is to be able to handle all types of plastic, and so our R&D team is developing techniques to recycle plastic such as PU, HDPE/LDPE and PP. Our goal is to follow the same trend from Lab to Pilot to Showcase to FOAK.
Source
nova-Institute, original text, 2024-10-15.
Supplier
BASF SE
Beiersdorf AG
DePoly SA
nova-Institut GmbH
QEMETICA
Syensqo
Share
Renewable Carbon News – Daily Newsletter
Subscribe to our daily email newsletter – the world's leading newsletter on renewable materials and chemicals