The manufacturing of materials such as concrete or plastics goes hand in hand with massive CO2 emissions. Within the scope of its BasFlair and GreenBraid Projects, the Institut für Textiltechnik (ITA) of RWTH Aachen University researches the usability of climate-friendly natural materials. These projects are now being recognised by the KlimaExpo.NRW. Dr Heinrich Dornbusch, chairman of the initiative, presented an official certificate regarding the admission of the project to the state-wide exhibition to the project managers on Tuesday.
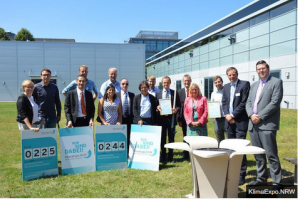
The Project BasFlair uses basalt fibres made from volcanic rock to manufacture climate-friendly concrete. In the GreenBraid Project, the scientists from Aachen use flax for the production of natural fibre reinforced plastics. “These two exemplary and innovative projects impressively show to produce materials in an energy-efficient and CO2 emission-saving manner. Therefore, the projects are two successful examples of the motor of progress that is climate protection” said Dr Heinrich Dornbusch, chairman of KlimaExpo.NRW when he presented the certificates to Andreas Koch, Project Manager of BasFlair, and to Viktor Reimer and Marie-Isabel Popzyk, Project Managers of GreenBraid.
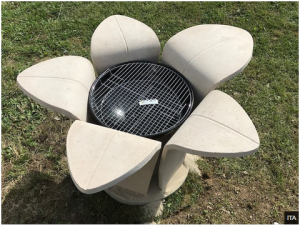
Sustainable concrete made with volcanic fibres
Concrete, the research object of the BasFlair Project, is one of the cheapest and most important materials for the construction industry. However, it is also one of today’s biggest climate killers. The production of cement, one of the core ingredients of concrete, is responsible for 6-9% of global CO2 emissions. In order to combine the good material properties of concrete with those of technical textiles and create a resource efficient alternative to conventional concrete, textile concrete is being developed in Aachen since the 1990s. Usually, textile concrete contains glass- or carbon fibres which enhance the tensile strength of normally brittle concrete. Because the components of textile concrete are up to 75% thinner, and therefore lighter, than those of conventional steel-reinforced concrete, while maintaining the same strength, transport costs and production-related CO2 emissions are considerably lower. Textile concrete is also more corrosion-resistant and more malleable than conventional concrete.
The BasFlair Project now replaces conventional expensive and energy-intensive carbon glass- and carbon fibres with basalt fibres made from volcanic rock. “Basalt fibres can significantly enhance the application fields of the innovative composite material that is textile concrete. The main arguments are the low price and sustainability which result from the use of a renewable material.” says Andreas Koch, Head of the Department of Textile Construction at the Institut für Textiltechnik (ITA) of RWTH Aachen University.
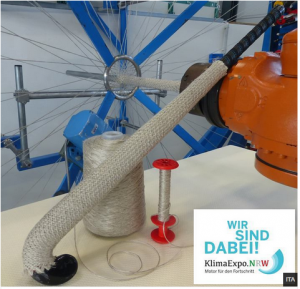
Development of resistant flax-composite-materials
The GreenBraid project develops natural fibre reinforced synthetic materials. Natural fibre-reinforced synthetic materials are much more energy efficient than carbon-reinforced fibres, which are used to construct bicycle frames for instance. The GreenBraid Project uses flax as a natural fibre and produces a hockey stick as a prototype which particularly benefits from the good cushioning properties of the natural fibre, which curbs the strain on joints, arms, and legs. The project optimises the properties of flax fibres in a fibre composite material with the aim of lowering the energy consumption by up to 75% compared to the conventional production method. “With GreenBraid it becomes possible to use bast fibres such as flax for highly loaded parts from fibre composite materials, which so far could only be exploited with glass fibres. By using bast fibres, we’re able to save about 30% in CO2 emissions, compared to using conventional glass fibre reinforced synthetic materials”, Project Manager Viktor Reimer of ITA summarises. The project is being accompanied by three industry partners: Barthels-Feldhoff GmbH & Co. KG from Wuppertal, Germany as well as NPSP BV and Holland Hockey from the Netherlands.
Both the BasFlair Project and the GreenBraid Project are being conducted within the framework of the European funding program “Eurostars”. The German partners receive funds from Germany Federal Ministry of Education and Research.
Source
Institut für Textiltechnik (ITA), press release, 2017-07-18.
Supplier
Barthels-Feldhoff GmbH & Co. KG
Bundesministerium für Bildung und Forschung (BMBF)
Holland Hockey
Institut für Textiltechnik (ITA) – RWTH Aachen
KlimaExpo.NRW
NPSP Composites
Share
Renewable Carbon News – Daily Newsletter
Subscribe to our daily email newsletter – the world's leading newsletter on renewable materials and chemicals