The founders of the company IneraTec are developing a chemical reactor that can produce synthetic fuels from a broad range of different gas sources. What is completely new is the size of the reactor: it is no bigger than a desk. The IneraTec founders have found a way to design a compact reactor that fits into a container and only needs be connected to a gas source. At present, the reactor is set up to use methane as a source gas, but it has the potential to convert carbon dioxide and hydrogen mixtures into fuels at some point in the future. This, in combination with its decentralised application, gives some idea of the huge potential of the IneraTec reactor.
The company IneraTec – Innovative Reactor Technology – convinces with its technical know-how and pioneering idea: “We are planning to manufacture containerised, compact reactor systems that enable the chemical conversion of methane into fuel,” says Phillip Engelkamp, industrial engineer and one of the co-founders of IneraTec, which will be officially launched in summer 2015. The founding team consists of Tim Böltken, Paolo Piermartini, Professor Peter Pfeifer and Phillip Engelkamp, all of whom have a background in industrial engineering. IneraTec’s initial headquarters will be at the Karlsruhe Institute of Technology (KIT), which has been made possible through the Young Innovators programme run by the Baden-Württemberg Ministry of Science, Research and the Arts. “The support from the programme has enabled us to continue using the outstanding infrastructure at the KIT’s Institute for Micro Process Engineering (IMVT) whilst concentrating on establishing the company,” says Engelkamp.
Containerised, chemical production of synthetic fuels
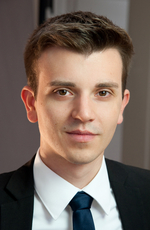
Before they considered establishing a company, the IMVT scientists had all intensively worked on the ways the Fischer-Tropsch (FT) process could be put to good use in converting gases into fuels. The FT process is a collection of chemical reactions that turns a mixture of carbon monoxide (CO) and hydrogen (H2) into medium- to long-chain hydrocarbons. Hydrocarbons with a length of 5 to 22 carbon atoms are suitable as liquid fuels such as petrol and diesel. Further extension of the carbon chain even leads to solid paraffin (waxes).
“The large-scale application of the FT process began in South Africa in the 1950s. My colleague and co-founder of IneraTec, Tim Böltken, studied for a while in South Africa where he gained useful experience,” says Engelkamp. In Africa, coal is used as feedstock material for the production of liquid hydrocarbons. The original FT process was invented by Fischer and Tropsch in Germany in the 1930s. Natural gas is now used in place of coal as feedstock for producing synthetic fuels. In order to make natural gas suitable for large-scale FT, the methane (CH4) contained in natural gas needs to be converted into gaseous reactants, i.e. carbon monoxide and hydrogen, in a process known as steam reforming. Carbon monoxide and hydrogen are then further processed into synthetic fuels. This method has been used on a large scale in South Africa since the early 1960s, and predominantly in the Middle East and Malaysia since the 1990s. “The gigantic gas-to-liquid plants in such regions are around half the size of Stuttgart, the sixth largest city in Germany. And they cost about 35 billion euros,” says Engelkamp.
The IneraTec founders will initially also use methane-based natural gas as the basis for synthetic fuel production. Since portable decentralised reactors are synonymous with relatively independent production sites, Engelkamp and his colleagues have decided to initially focus specifically on smaller-scale reactors. “Not all countries have as much coal as countries like South Africa, or as much natural gas as Qatar. “Our approach enables us to use smaller gas deposits,” says Engelkamp. IneraTec’s chemical FT reactor is only as big as a desk, thanks to a sophisticated and compact design and the possibilities now offered by the fields of microsystems engineering and microprocess engineering. “The reactor and all other modules required for the process, including compressors and the gas purification unit, fit easily into a shipping container,” says Engelkamp referring to their invention.
“Our current approach is based on using methane – for example methane derived from natural gas – as carbon source. We have chosen the process parameters so that only liquid hydrocarbon chains – i.e. fuels – are produced. This fuel mixture usually consists of 25 per cent petrol (C5 to C11 chains), 50 per cent diesel (C5 to C22 chains) and 25 per cent kerosene (C8 to C13). The ratio of the chain lengths can be adapted to a certain degree with the application of the resulting fuels in mind. We can produce up to 8,000 litres of this fuel mixture per day,” says Engelkamp. “At present, the final refining step, i.e. the separation of the fuels, needs to be done somewhere else, but in theory it is possible to add a small separation system as another module to the containerised system.” IneraTec’s modular system costs around 1.25 million euros per container. “This sounds quite a lot for an initial outlay. However, once sales increase, we will be able to reduce production costs and make economies of scale,” says Engelkamp.
Enormous potential for the future bioeconomy
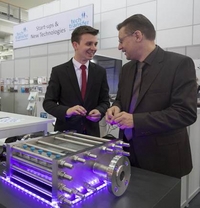
The gas-to-liquid FT process requires carbon monoxide and hydrogen, which can be produced from methane. However, methane derived from fossil natural gas is not the only feedstock material that can be used for this purpose. Biogas, which consists of up to 70 per cent methane, can also be used. Landfill and sewage gases also contain large amounts of the colourless and odourless gas and could also be used in an IneraTec reactor to produce synthetic fuels using the FT process. “We are trying to establish a complete value creation chain. And this is where the flexibility of the reactor pays off. Biogas-derived methane can be purified and processed directly in the containerised reactor. Since we require between 20 and 100 standard cubic metres methane per hour, we are looking at farmers’ associations and other biogas producers that are operating old block heat and power stations and who might be interested in producing their own fuel. Around 600 litres of fuel mixture an hour can be produced from 100 m3 methane,” says Engelkamp.
The reactor vision goes even further. “As a disruptive innovation, our technology has the potential to completely revamp the value chain for fuels,” says Engelkamp. There is also the possibility of producing the methane required with biotechnological methods, i.e. with bacteria that convert carbon dioxide and hydrogen into methane and water. In this way, the bacteria would withdraw the greenhouse gas carbon dioxide from the atmosphere and turn it into a valuable fuel.
Water electrolysis has the potential of being used for producing the hydrogen required. However, this approach consumes a lot of energy. If this energy could be produced with solar cells or wind turbines, water electrolysis would be an outstanding possibility for storing regenerative energies in the form of fuels. “This is still a vision of the future, but in five to ten years’ time, it could be relevant for our modular approach. We do not want to produce the gases, but use them. However, a company that is working on the development of a compact electrolysis system for the production of hydrogen, would be an exciting strategic partnership that we would certainly consider,” says Engelkamp.
IneraTec interprets the signs of the times. The sense of sustainability and innovative thinking has never before been so noticeable – both in Baden-Württemberg and throughout Europe. The company’s developments also benefit from new laws and amendments such as Germany’s Renewable Energy Act. “Since the introduction of the Renewable Energy Act in Germany, block heat and power stations have been receiving fewer subsidies than before. Therefore, fuel production alternatives such as the one we are developing are becoming increasingly important. A rethinking is also taking place in the fuel sector, and this will also be to our advantage. The idea is to reduce the envisaged 10 percent energy crop-derived ethanol part of the E10 fuel (fuel mixture of 10% anhydrous ethanol and 90% petrol) blend to seven percent, and replace the remaining three per cent with second-generation fuels. And we are second-generation fuel producers,” says Engelkamp.
Support to market
IneraTec is employing an award-winning concept. In 2014, the innovative character of the project also convinced BIOPRO Baden-Württemberg. Back then, one of the IneraTec founders, Paolo Piermartini, presented the IneraTec concept at the Bioeconomy Conference, which was jointly organised by the Baden-Württemberg Ministry of Science, Research and the Arts, the University of Hohenheim and BIOPRO Baden-Württemberg GmbH in Stuttgart. “BIOPRO put us into contact with interesting people, and we have benefitted enormously from BIOPRO’s assistance and the contacts we made,” says Engelkamp. The only thing that is missing before the founders have a marketable system and can initiate serial production, is producing a containerised system that they could use to show that the compact process works perfectly and to demonstrate market maturity.
Contact
Philipp Engelkamp (Managing Director)
IneraTec – Innovative Reactor Technology
Karlsruhe Institute of Technology
Tel.: +49 (0)721/608 22732
E-mail: philipp.engelkamp@ineratec.de
Author
Sanja Fessl
Source
BIOPRO Baden-Württemberg, press release, 2015-05-18.
Supplier
BIOPRO Baden-Württemberg GmbH
INERATEC - Innovative Reactor Technology
Karlsruher Institut für Technologie (KIT)
Ministerium für Wissenschaft, Forschung und Kunst (BW)
Share
Renewable Carbon News – Daily Newsletter
Subscribe to our daily email newsletter – the world's leading newsletter on renewable materials and chemicals