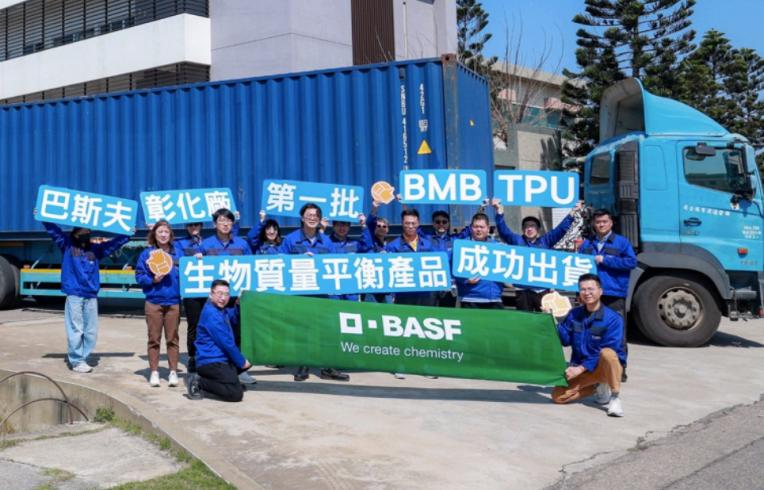
BASF is celebrating its first full container shipment of Elastollan® BMB – a new bio-attributed (mass balanced) thermoplastic polyurethane (TPU) solutions, tailored for the footwear/apparel industry. Produced at our BASF TPU production facility in Taiwan, this marks a big step toward sustainable manufacturing.
Elastollan is the brand name for BASF’s thermoplastic polyurethane (TPU). It stands for maximum reliability, consistent product quality and cost efficiency. Elastollan® can be extruded into hoses, cable sheathing, belts, films and profiles, and can also be processed using blow molding and injection molding technologies.
The new TPU series provides exceptional hydrolysis and microbe resistance and combines stable processing behavior with good compression set properties. The material delivers outstanding burst pressure performance and can be processed by extrusion and injection molding. The aging stability of Elastollan® 1400 ensures long-lasting performance – a versatile option for a wide range of applications.
Improved sustainability by lower product carbon footprint
The Elastollan® 1400 series has been designed with sustainability in mind, offering a lower carbon footprint when compared to TPU grades with a comparable performance (e.g., for a hardness of shore 80 A it is possible to reduce the carbon footprint by up to 30%). This sustainability advantage appeals to manufacturers prioritizing environmental concerns and seeking ways to minimize their ecological footprint.
Advanced material technology with excellent mechanical properties
Key advantages like hydrolysis resistance and excellent mechanical properties make Elastollan 1400 an ideal choice for diverse industries such as transportation, industrial manufacturing, and footwear. Whether it is rail pads, cable sheathings, tubes and hoses, profiles, gearwheels, or shoe soles, the new grades provide reliability and long-lasting performance. For the footwear industry, superior wet slip resistance is a key benefit, ensuring enhanced safety and comfort.
The 1400 series offers unique dynamic properties originated from a discrete glass transition temperature (Tg) and an extended viscoelastic plateau. These features contribute to improved dimensional stability and a wide thermal application range.
With Elastollan BMB, BASF can help reduce the product carbon footprint(PCF) for its customers who mould or extrude parts for versatile goods in daily life, helping brands create top-quality products.
Additionally, they started using renewable electricity at the plant and launched a TPU recycling project to realize “Make, Use, Recycle” as a complete circle.
Source
Bioplastics MAGAZINE, 2025-04-02.
Supplier
Share
Renewable Carbon News – Daily Newsletter
Subscribe to our daily email newsletter – the world's leading newsletter on renewable materials and chemicals