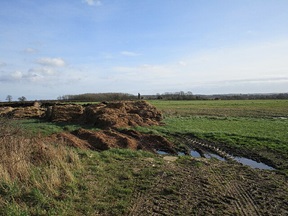
Boards are a wonderful material. For many purposes, they are strong enough. They consist of pressed wood chips, contained in a layer of veneer. Nowadays, much furniture is made from this material. Like cupboards and tables. They help makers to produce their products cheaply, without much quality loss. For they are made of waste wood or unusable pieces of wood; lending them a useful application after all.
Side streams
But often, boards consist just in part of recycled wood. This is being supplemented with fresh wood, that sometimes covers more than half of the material used. Causing waste wood to end up in the shredder after all. But not if Ecoboard can help it.
Founder Waldo Chotkoe tells Change.inc that they use vegetal leftovers: from rice, wheat, paprika, tomatoes. Often, these are being burned on the land; Ecoboard pays for them. The upside of this is that waste is being produced all year around. And that the company can buy the agricultural waste where it is being produced.
Consequently, their material is competitive against existing board materials. And the upside of this resource is that it grows much faster than wood. It is available already after half a year to a year – whereas it may take twenty years before one can saw planks from a tree, the process that will also produce wood waste. Moreover, the agricultural fibres chain is relatively well-organized and transparent. In the case of wood fibres however, there is always a degree of uncertainty: maybe, the product consists of finely ground used wood.
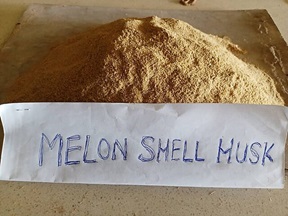
Quality
This wouldn’t even be a problem if wood-sourced board would be better in quality. But according to Chotkoe, board sourced from agricultural waste would even be better. Waterproof, for instance. An ecoboard hardly swells upon getting wet. Therefore, the lifetime according to their life cycle analysis is 75 years – whereas for chipboard, this is put at ten years.
Chipboard often contains a lot of glue, for keeping the wood fibres together. But ecoboards are being glued by an MDI resin. Together with the natural binding agents contained in the boards, this results in just 3 percent of glue being required. Therefore, at the end of their lifetimes, the boards will be entirely reusable. The goal being to reduce the amount of glue to zero.
A trend that is here to stay
At the moment, ecoboard production is mainly confined to mainland China. The factories there have mainly local customers. Ecoboard would like to conquer a market share in Europe as well, and therefore together with a partner constructs a factory in Portugal, aimed at the European market.
Chotkoe is optimistic when it comes to the future of his product in Europe. In his opinion, there is much demand for construction materials with a low footprint. Not just with consumers, but increasingly also with construction companies and architects. According to Ecoboard, this trend is here to stay. Therefore, they are of the opinion that their product will be successful in Europe as well.
Author
Diederik van der Hoeven
Source
Supplier
Change Inc.
ECOBoard international BV
Share
Renewable Carbon News – Daily Newsletter
Subscribe to our daily email newsletter – the world's leading newsletter on renewable materials and chemicals