Who will win the main prize will be traditionally announced at the “BIOPOLYMER – Processing & Moulding” congress, which takes place on June 13th in Halle (Saale), Germany. As in previous years, participants from all over the world can follow the award ceremony and the entire conference free of charge in real time via video stream and participate in live discussions, too.
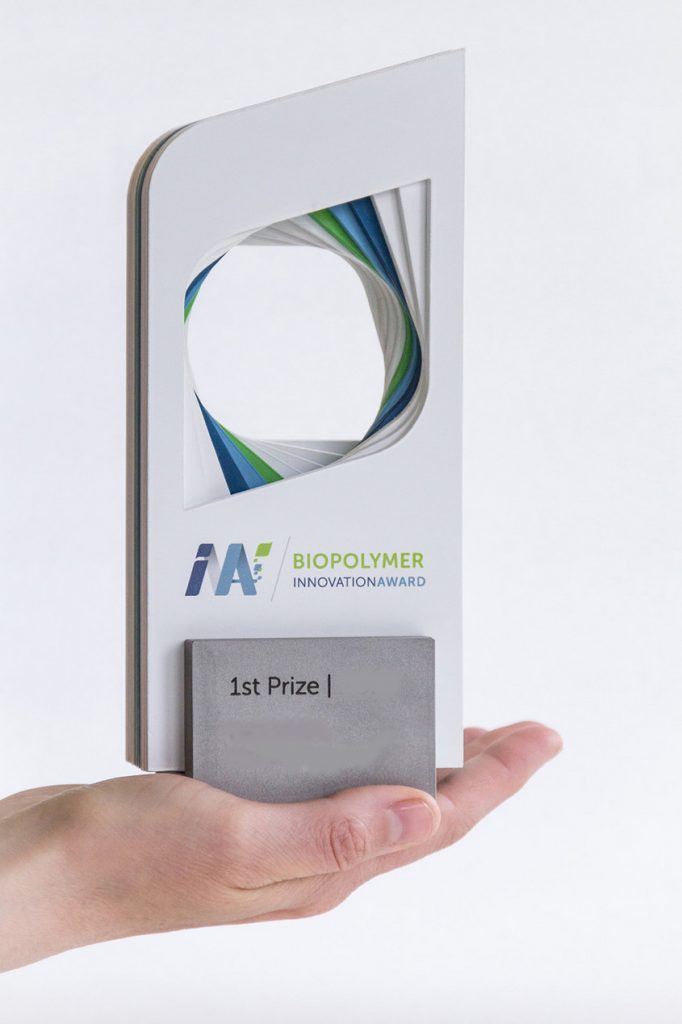
Is Germany still innovative enough to keep up with the world leaders? “When it comes to developing plastics and plastic applications on a biological basis and for non-fossil cycles, the answer is quite clear: yes!”, jury chairman Peter Putsch is more convinced than ever after this year’s nominations for the BIOPOLYMER Innovation Award: “Several German entries set the benchmarks in the competition this year.” While some of the coveted prizes have recently gone to Finland, Italy, Belgium or Brazil, this year for the first time the judges nominated only German applicants for the main prize, which is endowed with 2,000 euros. The three candidates and their innovations are briefly presented below (in reverse alphabetical order of the company names):
For its Cell-Screw® product, Green Elephant GmbH from Giessen makes use of a persistently underestimated property of the bioplastic and classic 3D printing material PLA (polylactic acid): its high biocompatibility. The start-up produces innovative cell culture flasks under the label CellScrew® from completely bio-based PLA using additive manufacturing. Tissue cells can be developed inside of CellScrew® in a new, more convenient way, for example for gene and cell therapies or for research into cosmetics and medicines. Researchers, developers and manufacturers are thus producing much more efficiently and in a more environmentally friendly way than before. An Archimedes screw and concentrically arranged cylinders inside the bottle ensure a huge surface for attachment of the cells and automatic wetting of the inner surfaces with culture medium when stored rotating. One CellScrew® replaces up to 400 conventional cell culture flasks made from fossil plastics. And even if the bio-based PLA is not composted after one-time use for reasons of sterility, but is burned, only as much CO2 is emitted as was previously bound in the bio-organisms from which the material was created.
For several years, SoBiCo GmbH from Rhineland-Palatinate has been pursuing an innovative approach to expand the inherently limited range of PLA (polylactic acid) systematically. “The low elongation at break of pure PLA, for example, is a key reason why the bioplastic is hardly used as a packaging material,” explains SoBiCo Managing Director Johannes Fuchs. Classic modification attempts usually failed due to the complex migration and crystallization behavior of plasticizers and other additives. Fuchs’ team found their own solution with the Potsdam Fraunhofer Institute for Applied Polymer Research (IAP) and named it Plactid®. The brand stands for a family of PLA copolymers that is manufactured using a new type of process – reactive compounding. In addition to lactide, which is always bio-based, various polyols are used, which can come from biological or fossil sources, depending on the application. In this way, the PLA copolymers can be specifically adjusted from hard/brittle to soft/ductile. For example, soft films with high crystallinity are possible. However, injection molding grades with a significantly higher crystallization rate and impact strength than standard PLA can also be produced. In addition, the PLA copolymers are also suitable as additives for modifying standard PLA.
The Thuringian Institute for Textile and Plastics Research Rudolstadt (TITK) has taken on a previously unsolved problem that everyone is literally surrounded by in their everyday lives: that of adhesives. They are in almost every product, mostly contain polymers, are typical single-use products, can hardly be separated in recycling processes and all too often end up in the environment as microplastics. The Thuringian researchers’ answer to this challenge is called Caremelt® and is a bio-based and biodegradable hot-melt adhesive whose end properties and application profile are comparable to those of established hot-melt adhesives. The formulation of biopolymers such as polylactic acid (PLA) and polybutylene succinate (PBS), of terpene and colophony resins, natural waxes and citric acid derivatives is not only suitable for short-lived products such as shopping bags, diapers or cardboard boxes. Shoes, textiles, furniture parts, vehicle interiors or books can also be joined together reliably and permanently, as practical tests have shown. The manufacturing process has already been optimized so that the formulations can be reproduced in a controlled process.
At the awards ceremony at the “BIOPOLYMER – Processing & Molding” congress on June 13, the coveted hand-made trophies will be presented to the winners. The three honorees present their innovations and answer questions from the audience in the George-Frederick-Handel-Halle in Halle (Saale) and in the worldwide live stream.
Source
Polykum, press release, 2023-05-23.
Supplier
Green Elephant GmbH
SoBiCo GmbH
Thuringian Institute for Textile and Plastics Research Rudolstadt (TITK)
Share
Renewable Carbon News – Daily Newsletter
Subscribe to our daily email newsletter – the world's leading newsletter on renewable materials and chemicals