Deutsche Version: https://renewable-carbon.eu/news/bioverbundwerkstoffe/
First presentation of the results at the biggest WPC event in Europe, “Fifth German WPC-Conference”, 10 and 11 December 2013, Cologne (www.wpc-conference.com).
The market report gives the first comprehensive and detailed picture of the use and amount of wood and natural fibre reinforced composites in the European bio-based economy. The analysis covers natural fibre as well as wood-plastic composites in extrusion, injection and compression moulding in different branches and applications.
To achieve a reliable base of data, the study draws from a survey conducted in 2013 among the WPC and NFC industry, producers and customers. The rate of return was exceptionally high, especially for the WPC part of the study, more than 50% of the extruded volume produced took part in the survey – that means the study covers about 65 European WPC extruding companies in 21 countries.
Wood-Plastic Composites – Decking still dominant, but technical applications and consumer goods rising
The total volume of WPC production in Europe was 260,000 tonnes in 2012 (plus 90,000 tonnes Natural Fibres Composites for the automotive industry, see below). The level of market penetration of bio-based composites varies between different regions and application fields. Germany leads in terms of number of actors as well as in production figures. The typical production process in Europe is extrusion of a decking profile based on a PVC or PE matrix. The increasing market penetration of WPC has meant that WPC volumes have risen strongly and that today, Europe has reached a mature WPC market stage. This study predicts growth especially in the German-speaking area on the back of a recovery in construction, especially in renovation, and a further increase of WPC share in the highly competitive decking market. Also, variations of WPC decking models, such as capped embossed full profiles or garden fencing are on the rise across Europe.
The development in shares of applications points to a direction where WPC is increasingly used for applications beyond the traditional ones such as decking or automotive parts. For example, WPC is increasingly used to produce furniture, technical parts, consumer goods and household electronics, using injection moulding and also other processes than extrusion. Also new production methods are being developed for extrusion of broad WPC boards.
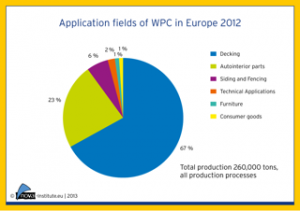
Figure 1 shows the different application fields of WPC produced in Europe. The decking market is leading with 67% (mainly extrusion), followed by automotive interior parts with 23% (mainly compression moulding and sheet extrusion as well as thermoforming). Although still smaller, siding and fencing as well as technical applications (mainly extrusion) and consumer goods and furniture (mainly injection moulding) are showing the highest increase in percentage. With increasing plastic prices, WPC granulates for injection moulding are getting more and more attractive, and are increasingly found in the product range of the European granulate suppliers.
The report also gives an overview of the latest market development in North-America and Asia and an overview and forecast of the global WPC market situation, which has grown up to 2.5 million tonnes of production in 2012. China has the strongest growth rates with a production volume of 900,000 tonnes in 2012 and is trying to catch up with the largest WPC production volume in the world, which takes place in North America and has grown to 1.1 million tonnes of WPC production in 2012. The share of WPC decking in the total decking market is increasing again, after a period of housing crises and WPC quality problems that have led to a shakeout of the top WPC producers.
In China, also decking has the largest market share compared to other WPC applications, mainly through strong exports, although the domestic market has steeply developed in recent times. China hosts also the largest window and door market of the world. Hence companies lately have started to produce commercial window frames with WPC, with approximately 40 % of wood fibre that substitutes PVC in combination with aluminium. China produces a large variety of WPC for indoor applications. Another successful product is an extruded WPC door that is already produced by 30 companies.
Automotive Industry
The most dominant use of natural fibre composites by far can be found in interior parts of the automotive industry – other sectors such as consumer goods are still in a very early stage. In automotive, natural fibres composites have a clear focus on interior trims for doors for high-value doors and dashboard. Wood-Plastic Composites are mainly used in rear shelves and trims for trunks and spare wheels as well as in interior trims for doors.
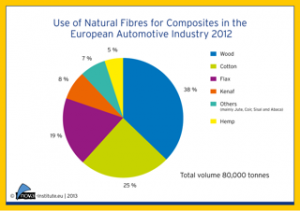
Figure 2 shows the total volume of 80,000 tonnes different wood and natural fibres used in 150,000 tonnes of composites in passenger cars and lorries, produced in Europe in 2012 (90,000 tonnes Natural Fibre Composites and 60,000 tonnes WPC). Recycled Cotton Fibre Composites are mainly used for the driver cabins of lorries.
The highest market shares are made up for by wood (European origin), recycled cotton (from world market) and flax fibres (European origin). Compared to the last survey for the year 2005, the shares of kenaf (from Asia) and hemp fibres (European origin) show the biggest increase in percentage.
Process-wise, compression moulding of Wood and Natural Fibre Composites is an established and proven technique for the production of extensive, lightweight and high-class interior parts in mid-range and luxury cars. Advantages (lightweight construction, crash behaviour, deformation resistance, lamination ability, depending on the overall concept, also price) and disadvantages (limited shape and design forming, scraps, cost disadvantages in case of high part integration in construction parts) are well known. Process optimisations are in progress in order to reduce certain problems such as scraps and to recycle wastage.
Since the year 2009, new improved compression moulded parts have shown impressive properties in weight reduction. This is one reason for the increasing interest in new car models. Today with the newest technology, an area weight of down to 1,500 g/m2 (with thermoplastics) and even down to 1,000 g/m2 (with thermosets) is possible – outstanding properties compared to pure plastics or glass fibre composites.
In the EU, 15.7 million passenger cars were produced in 2011; in addition, 2 millions of other motor vehicles (incl. trucks, transporter, motor bikes, etc.) were manufactured. Considering that 30,000 tonnes of natural fibres and another 30,000 tonnes of wood fibres were used in 15.7 million passenger cars, every passenger car in Europa averagely contains 1.9 kg of natural fibres, respectively 1.9 kg wood fibres, so in total that makes almost 4 kg of these fibres per car.
From a technical point of view, much higher volumes are possible. Vehicles with considerably larger amounts of 20 kg natural and wood fibres have been successfully produced in series for years. The market development depends also on the political framework: Any incentive for the use of natural and wood fibres in the European automotive industry could help to extend the existing amount of 30,000 t/year for natural and wood fibres each. The vision could be an increase of up to five times, that means to 150,000 t/year for each fibre type – the technologies are ready to use. A great potential for biocomposites!
Content of the report
The full report contains about 150 pages and covers almost all aspects of technical markets for natural fibres and WPC. The report “Wood-Plastic Composites (WPC) and Natural-Fibre Composites (NFC): European and Global Markets 2012 and Future Trends“ can be ordered for 1,000 € (plus VAT), starting now, the delivery of the report will start end of January. Please order here: www.bio-based.eu/markets
- WPC and NFRC: Definition, standards and norms, certifications
- Processing technologies
- Mechanical properties
- Comprehensive analysis of WPC market and application fields as well as distribution channels in Europe 2012 and overview for other regions
- World market for natural fibres
- Natural fibres in the European automotive industry 2012
- Overview of life cycle assessments for WPC and Natural Fibre Composites
- Summarizing SWOT analysis
First presentation of the results at the biggest WPC event in Europe, “Fifth German WPC-Conference”, 10 and 11 December 2013, Cologne (www.wpc-kongress.com).
Main authors of the study:
Michael Carus, Lara Dammer, Lena Scholz – nova-Institute (Germany)
nova-Institute is a private and independent institute, founded in 1994; nova offers research and consultancy with a focus on bio-based and CO2-based economy in the fields of feedstock, techno-economic evaluation, markets, LCA, dissemination, B2B communication and policy. Today, nova-Institute has more than 20 employees and an annual turnover of about 1.8 Mio. €.
Dr. Asta Eder – Asta Eder Consulting (Austria/Finland)
Dr. Asta Eder is one of the leading market experts on bio-based plastics and composites, especially on wood-plastic composites. Since about 15 years she is doing market research and consulting for the development of new bio-based composites and their applications.
Download this press release as PDF file: 13-11-26_pr_wpc_nfrc_study_nova
Responsible under press legislation (V.i.S.d.P.):
Dipl.-Phys. Michael Carus (Managing Director)
nova-Institut GmbH, Chemiepark Knapsack, Industriestrasse 300, DE-50354 Huerth (Germany)
Internet: www.nova-institute.eu and www.bio-based.eu
Email: contact@nova-institut.de
Phone: +49 (0) 22 33-48 14 40
Source
nova-Institute GmbH, press release, 2013-11-26.
Supplier
Asta Eder Composites Consulting
nova-Institut GmbH
Share
Renewable Carbon News – Daily Newsletter
Subscribe to our daily email newsletter – the world's leading newsletter on renewable materials and chemicals