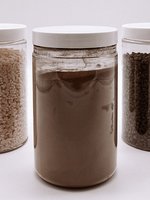
Making biogenic residual materials usable for business and industry – that is the primary research goal of the Institute for Biopolymers (ibp) at Hof University of Applied Sciences. Now the researchers may have made an interesting breakthrough. With the help of electron irradiation, they have been able to treat previously largely unused residual materials from the paper industry in such a way that they can be used as bioplastics for further processing. The materials obtained in this way are still completely biodegradable and could already be used for all kinds of products – if it was not for one unsolved problem.
Description
Ms. M.Eng. Kübra Aslan works as a team leader for the processing of bioplastics at the Institute for Biopolymers (ibp) at Hof University of Applied Sciences. There, she oversees the LigNutz research project, which already includes the name of the substance around which the young researcher’s ambitions currently revolve: Lignin. The biopolymer occurs naturally in trees, among other places, where it is responsible for the lignification of the cells and the tensile strength of the wood.
Residual material in paper production
In the production of paper, however, lignin is eliminated as a residual material because it would otherwise cause the paper sheets to yellow: “The kraft lignin obtained in this way accounts for 85 percent of global lignin production. However, only about 5 percent of it is currently used, for example as an admixture in cement, pet food or in the lignin-containing ARBOFORM® granules produced by Tecnaro, which can be further processed into injection-molded components. By contrast, 95 percent is used at best for energy generation. “We would like to change that,” explains Kübra Aslan. The problem is that, as a natural biopolymer, kraft lignin simply could not be used by industry because it cannot be melted in its original state and thus cannot be molded or processed.
Irradiation changes the structure
The suggestion to focus on precisely this problem was finally brought to the attention of the researcher and the head of the institute, Prof. Dr. Michael Nase, by the company Tecnaro GmbH, a long-standing research partner of Hof University of Applied Sciences, where it was immediately taken up. “Now there are several ways to change the structure of lignin so that it can be shaped and processed. Of course, chemical treatment was out of the question for us, since our end product should always remain biodegradable. That’s why we decided to experiment with electron irradiation,” says Kübra Aslan. Together with her team, she completed several series of tests to achieve the desired goal.
New substance to be fully processed
The researcher explains how electron irradiation works: “At an external partner of our institute, the surface of the kraft lignin was irradiated with electrons of different strengths. As a result, free radicals are formed on this surface, which combine with another bioplastic during compounding and change the chemical structure to the desired form.” This result has now also made it possible for the researchers to develop a thermally stable lignin compound, i.e. a new compound of the bioplastic. This has the desired properties: “The new bioplastic based on kraft lignin can now be pressed through a shaping nozzle and thus be shaped. The corresponding process is called extrusion. In this way, we can produce tubular films at our institute, for example,” says Kübra Aslan. After extrusion, the products also have very good mechanical properties such as high tensile strength and/or high elongation at break, which extends the product’s range of applications.
Open questions
However, as the researchers at Hof University of Applied Sciences concede, this does not eliminate all problems associated with making the residual material lignin usable: “Lignin – even in its processed form – has a slight smell of burning about it. This means, of course, that it is not yet suitable for all products, especially those that are close to people. So research still has a way to go here,” says Prof. Dr. Michael Nase, head of ibp.
The “LigNutz” project is funded by the German Federal Ministry for Economic Affairs and Energy as part of the Central Innovation Program for SMEs (ZIM).
Source
Hochschule Hof, press release, 2021-06-17.
Supplier
Bundesministerium für Wirtschaft und Energie (BMWI)
Hochschule Hof - University of Applied Sciences
TECNARO GmbH
Share
Renewable Carbon News – Daily Newsletter
Subscribe to our daily email newsletter – the world's leading newsletter on renewable materials and chemicals