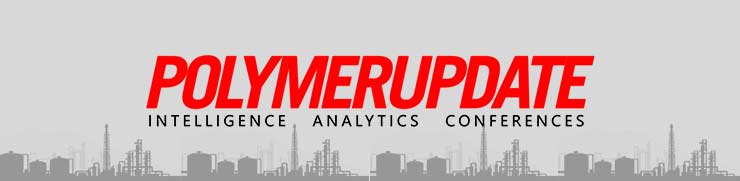
The chemical industry’s demand for carbon continues to grow, and so does the need to lower its dependency on fossil fuels. This, coupled with the goal to achieve net-zero emissions by 2050, has accelerated feedstock innovations. Along with new generations of bio-based feedstocks and advanced recycled raw materials, the industry is actively exploring carbon capture and utilisation (CCU) technologies to use CO2 as a feedstock. Here, Sreeparna Das, independent specialist consultant to the chemicals industry and contributor to materials database Matmatch, outlines some key advancements in the market.
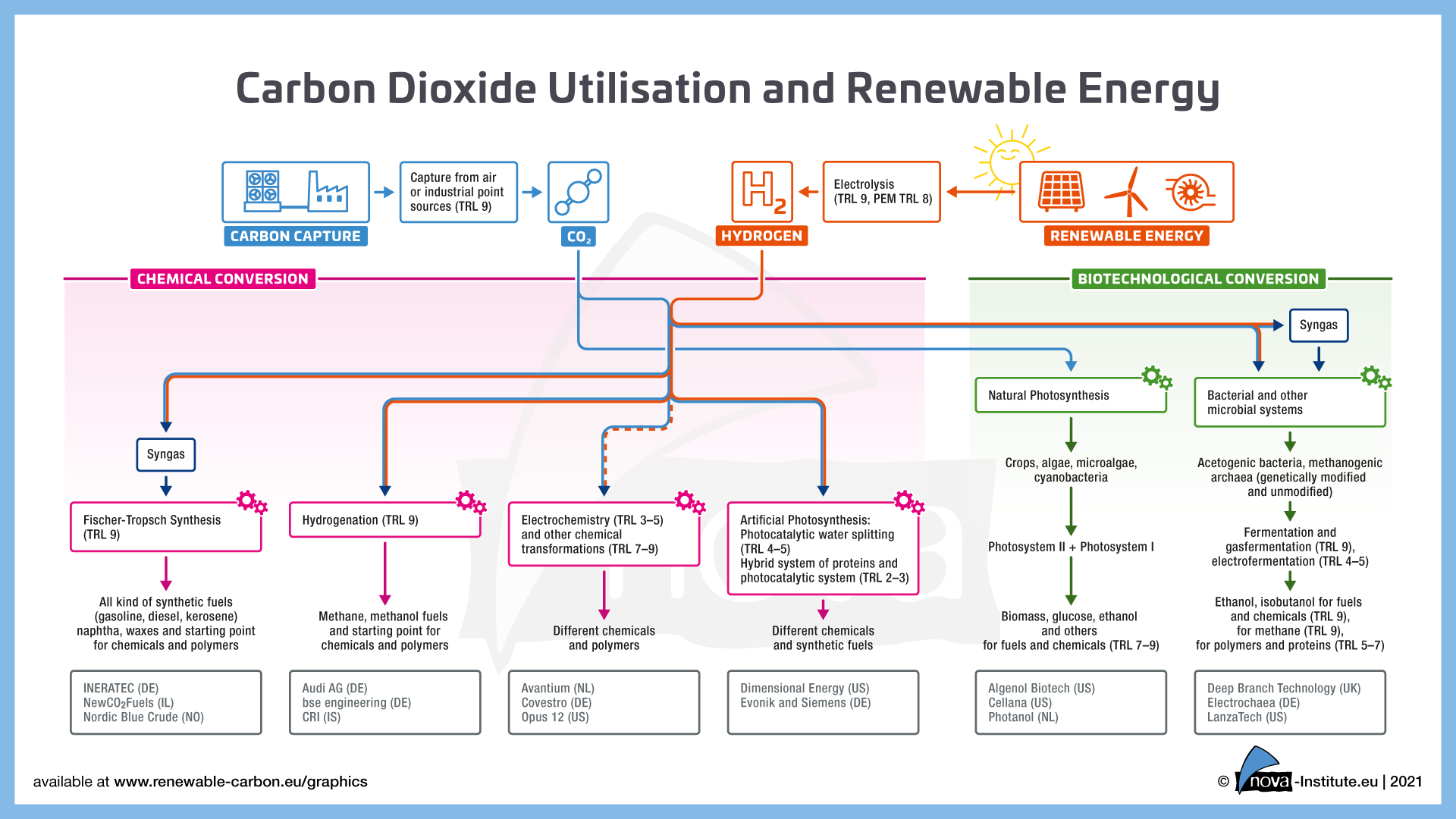
Some promising advances in CCUs have been made in recent years, and we are starting to see examples of commercial products. A joint partnership between LanzaTech, Total Energies and L’Oréal recently made headlines with the development of a cosmetic plastic bottle made from waste CO2. The three partners are working together to scale up the production of these sustainable plastic packaging. We’ll get to more such examples and other developments a little later in the article. But first, let’s understand a bit more about the technology.
Thanks to Elon Musk funding the $100M XPRIZE carbon removal contest, carbon capture, utilisation, and storage (CCUS) technologies have taken centre stage in the mainstream discussion this year.
The pathway to net-zero emissions is a complex one. While the energy sector is looking to decarbonize by moving towards renewable sources, the task is more complicated for other industries like cement, steel, mining and chemicals. With CCU technology, the flue gases emitted by these industrial plants can be used to recover CO2, which can further be upcycled into useful products. An added bonus is that this also helps in lowering GHG emissions and replacing fossil-based raw materials.
Upcycling CO2 into high-value chemicals and polymers
One of the initial examples of CO2 conversion into polymers that I’d come across was the one developed by the American company, Novomer. In February 2013, the company had announced its first production of 7 tons of Polypropylene Carbonate (PPC) polyol, produced using their proprietary catalyst that enabled the direct incorporation of CO2 (up to 40 per cent by mass) into the molecular backbone of propylene oxide.
Novomer’s Converge® polyol technology was acquired by Saudi Aramco in 2016 and was made market-ready within the next two years. When incorporated into polyurethane formulations, the material demonstrated superior performance and the potential to be a sustainable alternative in coatings for household appliances, consumer and industrial adhesives, automotive and medical applications, food packaging and more.
Currently, several conversion pathways are being explored. To achieve maximum environmental benefit, renewable energy will be needed for CO2 utilisation.
From mattress foam and textile fibres to surfactants made from CO2, Covestro (formerly Bayer Material Science) is another pioneer in this space. Scientists and researchers from RWTH Aachen University and Covestro, as part of the “Dream Reactions” project, discovered a unique catalyst that enabled CO2 to react with high-energy substances known as epoxides without complicated side reactions. The inventors of the technology were one of the three finalists at the European Inventor Award 2021.
Since 2016, Covestro has been using “Dream Resource” CO2 to produce polyols as a component for soft polyurethane foam. The polyols, marketed as cardyon®, find use in several other applications and make it possible to save up to 20 per cent of fossil resources.
Both the examples, Saudi Aramco (Novomer) and Covestro, are classified under the chemical conversion technologies involving a chemo catalytic reaction to produce CO2-based polyols. Next, let’s consider one of the leaders in biotechnological conversion. Using special microorganisms, LanzaTech converts carbon emissions (via gas fermentation) into ethanol and other chemicals.
LanzaTech’s technology is already used on a commercial scale to transform steel production exhaust gases into ethanol. And they have set up interesting partnerships across the value chain to develop new solutions. Together with Twelve, a carbon transformation company, LanzaTech plans to develop CO2Made polypropylene. And, similar to the cosmetic plastic bottle example mentioned earlier, the company has partnered with India Glycols Limited, Far Eastern New Century and lululemon to create CO2-based polyester fabric.
CCUS is also finding use in non-textile related markets. Photanol, a company active in the biotech space, has developed a unique process that harnesses cyanobacteria’s power to photosynthesise and produce key industrial compounds. The company has partnered with Corbion, Nouryon and Renolit and offers a whole host of important intermediates like lactic acid, glycolic acid, ethylene and propylene.
Another interesting project is Avantium’s Volta Technology, which is an example of the electrochemical conversion of CO2. A founding member of CO2 Value Europe, the Volta team cooperates with more than 35 partners through various EU consortia.
With expertise in Gas Diffusion Electrode (GDE) technology and paired electrolysis, their process converts CO2 into higher-value chemicals like formic acid, glyoxylic acid, and glycolic acid. They are also working on the conversion to ethylene glycol to produce CO2-based polymers in association with researchers at the University of Amsterdam.
Future outlook
So, the big question is, “can CO2 be the raw material for chemicals and fuels in the future?”
At the CO2WIN Conference held earlier this year, Prof. Eelco T. C. Vogt from the University of Utrecht presented a keynote speech, where he shared an answer to this question. He noted that a combination of several different processes and technologies at desired scale is required to achieve this. While some of the processes are already industrially available, considerable scale-up will be required for many others.
“The main challenge lies in the capture of CO2 from air. If the refinery of the future, which consumes about 20 kton CO2 per day, would use DAC (direct air capture) for its CO2, this would require a process about 1750 times larger than the present capabilities. Capture from stationary sources would be easier and would require only a three times larger scale”, said Prof. Vogt.
If additional raw materials are to be obtained from plastic waste or biomass, this would require a scale-up of 10 to 15 times. The move to renewable energy will also be critical, and here, material shortage for windmills, solar panels, etc. could be a major hurdle. Therefore, the magnitude of innovation, technology scale-up and investment required will be huge.
Exponential development of technology will need to continue, and the government and industry must work together with a strong and long-term commitment. Clearly, the time to act is now.
Author
Sreeparna Das
Source
Petrochemical Industry, press release, 2021-12-07.
Supplier
Avantium Technologies B.V.
Corbion
Covestro AG
European Union
Far Eastern New Century Corporation (FENC)
India Glycols Limited (IGL)
LanzaTech Ltd.
lululemon athletica
Nouryon
Novomer
Photanol
RENOLIT SE
Rheinisch-Westfälische Technische Hochschule Aachen (RWTH)
Saudi Aramco
Twelve (formerly OPUS12)
University of Amsterdam (UvA)
Utrecht University
Share
Renewable Carbon News – Daily Newsletter
Subscribe to our daily email newsletter – the world's leading newsletter on renewable materials and chemicals