Plastic waste can be used as a raw material for making high performance porous membranes. These could then be used in the chemical industry for the energy-efficient separation of complex chemical mixtures or to clean up waste streams, further adding to the environmental appeal of the process.
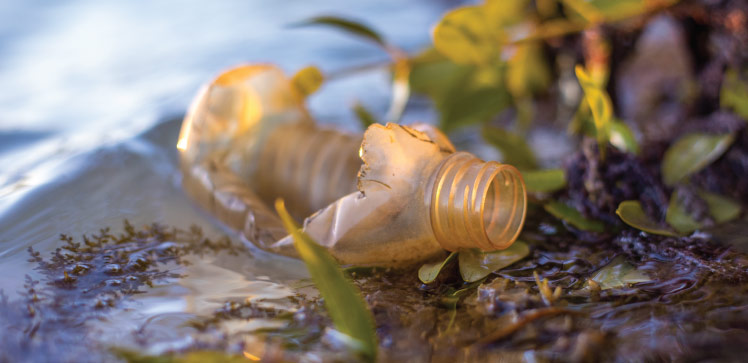
Polymeric membranes could be great partners for addressing many sustainability challenges, says Malinalli Ramírez Martínez, a Ph.D. student who led the research in Suzana Nunes’ group at KAUST. Thanks to their selectively permeable porous structure, they can reduce the environmental footprint of industrial separations, help in the treatment of waste effluent and create access to fresh water, she says.
“However, traditional membrane fabrication approaches mostly use pristine fossil-based nonrenewable materials, which has a negative environmental impact and contradicts the sustainability benefits,” Ramírez Martínez says.
“We wanted to take polymeric membrane sustainability one step further by replacing some of the conventional materials used for their fabrication with bio-based solvents and waste plastics, following the principles of circular economy and green chemistry.”
Polyolefin plastics make up almost half of all discarded items in plastic waste streams. “Polyolefins are very popular due to their low cost and high thermal and chemical stability,” Ramírez Martínez says. “We find them in food packaging, reusable bags, shampoo bottles, toys and many more products.”
These same properties make polyolefins attractive for producing hydrophobic microporous membranes for oil purification and other industrial purification processes. “However, the main challenges for processing polyolefins into porous membranes are the high temperatures required to dissolve them — commonly between 140 and 250 degrees Celsius — and the limited range of solvents that can be used, most of them fossil-fuel based.”
Two bio-based solvents can significantly improve the sustainability of this process, the team has now shown. “We found that terpenes — naturally abundant renewable solvents derived from nonfood biomass — could dissolve polyolefins at just 130 degrees Celsius,” Ramírez Martínez says. “Secondly, using these solvents we successfully made polypropylene membranes using plastic waste from food packaging, transforming single-use plastics into high-performance materials.”
These membranes proved adept at separating the water-in-oil emulsions that can be generated by certain industrial processes. “The rejection values and oil purity we recorded were comparable to state-of-the-art membranes reported in the literature,” Ramírez Martínez says. “We consider it a great achievement to have proved that membranes prepared from plastic waste can have a competitive performance compared to those made from pristine materials.”
Nunes also notes the wider applicability of this work. “Polyolefins are soluble only in a few solvents such as decalin. Finding solvent alternatives, particularly bio-based solvents, is relevant not only for membrane fabrication,” she adds.
References
- Ramírez-Martínez, M., Aristizábal, S.L., Szekely, G. & Nunes, SP. Bio-based solvents for polyolefin dissolution and membrane fabrication: from plastic waste to value-added materials. Green Chemistryadvance online publication, 30 November 2022.| article
Source
KAUST, press release, 2023-02-05.
Supplier
Green Chemistry - Journal
King Abdullah University of Science and Technology (KAUST)
Share
Renewable Carbon News – Daily Newsletter
Subscribe to our daily email newsletter – the world's leading newsletter on renewable materials and chemicals