It is hard to imagine our daily lives without plastics made out of polyolefins. Unfortunately, practical methods for recycling of polyolefins are lacking. In the journal Angewandte Chemie, a research team has now introduced a new approach for making novel polyolefins that can be chemically deconstructed and re-polymerized without a loss of quality. The secret to the method is masked double bonds introduced to the polymer chain by means of a so-called “Trojan horse” functional group in the polymer chain.
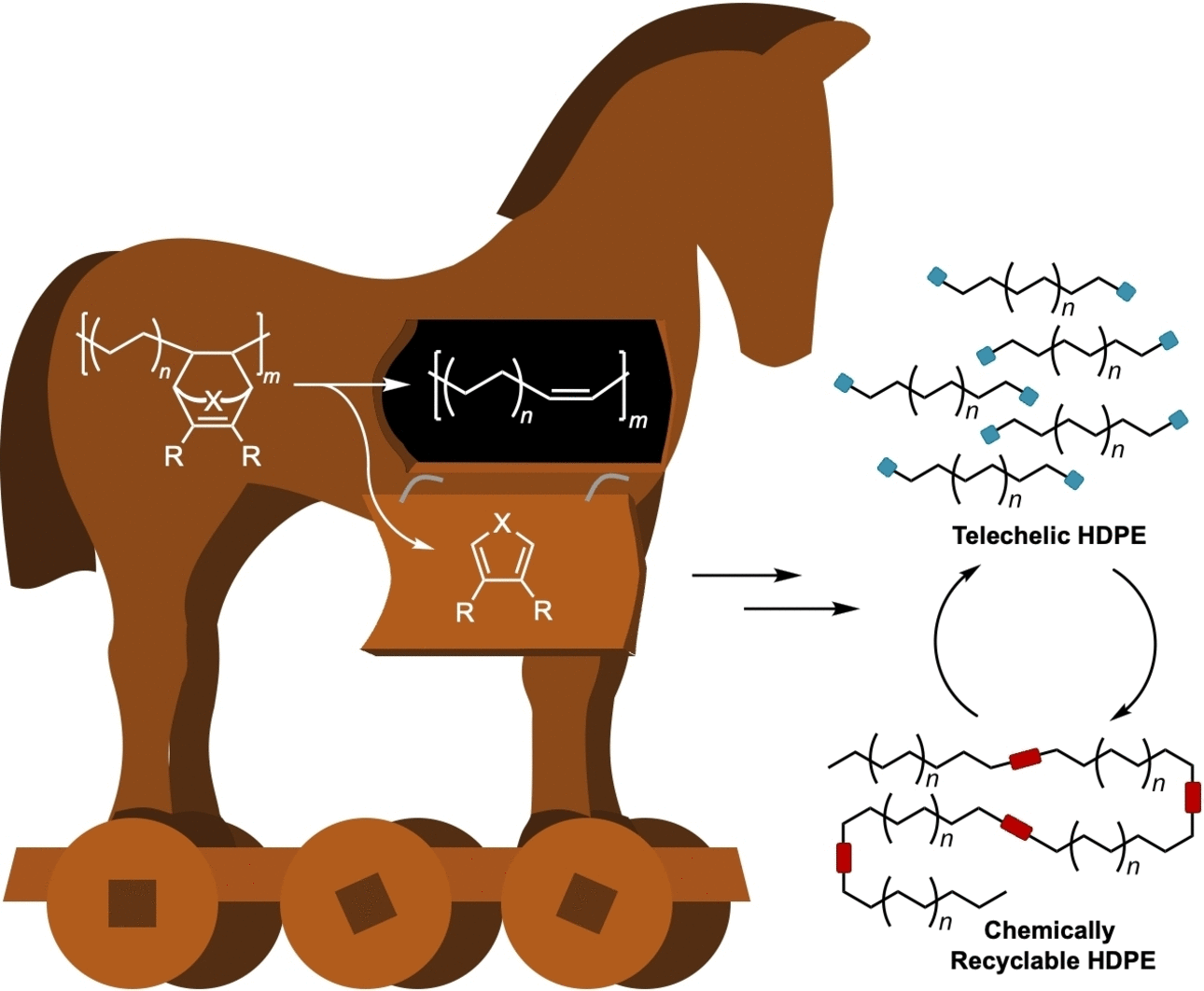
Polyolefins are stable, light, versatile, and inexpensive plastics made of very long hydrocarbon chains. However, their high stability and durability come with a drawback: after use, polyolefins are extremely persistent in the environment. Mechanical recycling forms products with inferior properties. The high chemical stability of polyolefins also inhibits chemical depolymerization to get back the monomers.
It would be more sustainable to have a circular economy based on alternative, chemically recyclable polyolefins that could be disassembled into smaller fragments, purified, and polymerized again. These smaller fragments are also more likely to be biodegradable if they accidentally enter into the environment. Unlike conventional polyolefins, such polymer chains would need to contain cleavable functional groups. A team led by Geoffrey W. Coates at Cornell University (Ithaca, NY, USA) has now taken a step further down this road. Their novel approach is based on a small number of unsaturated bonds that are built into the polyolefin chains with the help of a “Trojan horse” protecting group.
To do so, the team polymerizes ethylene to polyethylene in the presence of a special cyclic co-monomer (oxa-norbornadiene). Heating the copolymer causes the Trojan horse to “open up”; the rings are then cleaved with a retro Diels–Alder reaction, leaving behind a double bond in the polymer chain. The distance between the double bonds in the polymer backbone can be controlled by varying the amount of co-monomer in the feed.
In a reaction known as olefin cross-metathesis, the chains are split apart at the double bonds and attached to another molecule (2-hydroxyethyl acrylate) forming smaller chains with reactive groups at the ends. These macromonomers are then linked back together to form PE with low amounts of ester bonds.
By this method, the team was able to produce polymers with thermal and mechanical properties corresponding to those of high-density polyethylene (HDPE), a very important and widely used plastic. In contrast to HDPE, the new material has ester linkages along the polymer backbone. When recycled, the polymer chains can be chemically split at the ester bonds to regenerate the original macromonomers. After purification, these can be repolymerized again, without a loss in quality.
About the Author
Geoffrey W. Coates is the Tisch University Professor in the Department of Chemistry and Chemical Biology at Cornell University. He has worked in the area of sustainable polymers for over 25 years, and is a member of the US National Academy of Sciences.
Copy free of charge—we would appreciate a transcript/link of your article. The original articles that our press releases are based on can be found in our online pressroom.
Source
Wiley, press release, 2023-06-19.
Supplier
Angewandte Chemie (Journal)
Cornell University (USA)
Share
Renewable Carbon News – Daily Newsletter
Subscribe to our daily email newsletter – the world's leading newsletter on renewable materials and chemicals