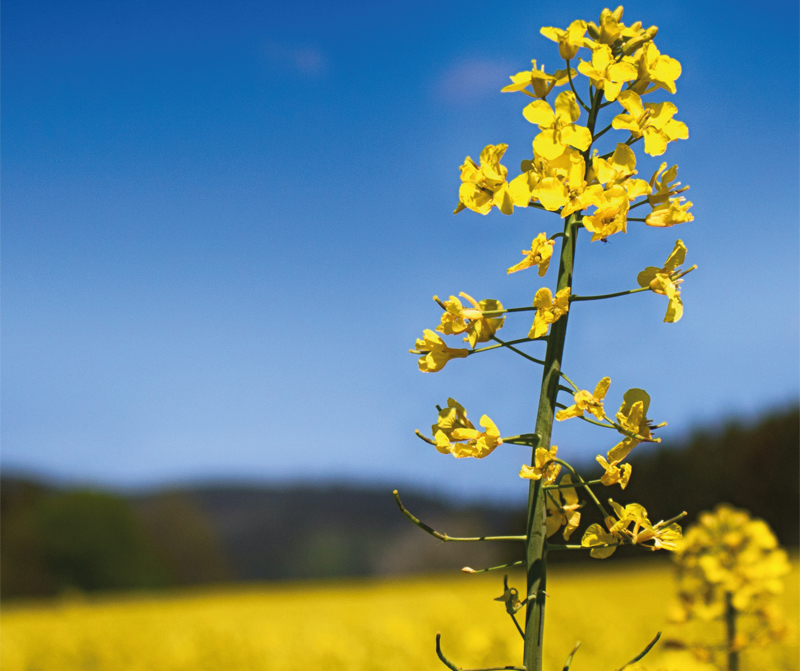
Sipol’s eco-sustainable growth continues with the new bio-based TPC Sipolprene S, combining the excellent performance of TPC-ET with the environmental and economic sustainability needs. Starting from four selected Sipolprene standard grades, a partial replacement of the soft segment with bio-based raw materials allows to reach a percentage of renewable source in all final products (C14/Ctot according to ASTM D6866) not less than 46%. On occasion of the TPE Forum at DKT IRC in June 2022, Sipol launched this range of new thermoplastic co-polyester elastomers.
Focus on sustainability
Sipol SpA, founded in 1998 and now part of the Tecnogi Group, is a chemical company whose core business is the polymerization of high-performance polymers, which are tailor-made for the adhesives and engineering plastics sector. The company currently sells 30 million euro of specialty polymers developed and manufactured at its plant in Mortara (about 40 km west of Milan). Its main activities are the development and manufacturing of thermoplastic co-polyester elastomers (TPC), co-polyester and co-polyamide-based hotmelt adhesives and biodegradable co-polyesters. The company successfully acts on several major markets such as automotive, footwear, packaging, E&E, cosmetics and other industrial sectors, thanks to its complete range of copolymers and it is widening its product portfolio in a more sustainable direction: after the launch of the new certified biodegradable and compostable products Technipol Bio, Sipol presents its new range of biobased high-performance thermoplastic co-polyester elastomers named Sipolprene S.
Sipolprene S, a biobased TPC
TPC-ET are segmented block copolymers obtained through the combination of rigid segments (polyester) and soft segments (polyether) which offers high performances of the final product such as chemical and mechanical resistance. The easiest way to polymerize co-polyester elastomers with a certain amount of monomers coming from renewable source is to substitute synthetic 1,4-Butanediol (BDO) with bio-1,4-Butanediol (bio-BDO) coming from starch and sugar fermentation. Technically, the substitution is easy to be managed and both polytime and properties of the final polymer are not affected. However, this leads to an amount of the renewable source in the final product (C14/Ctot according to ASTM D6866) in the maximum range of 10-30 % and this percentage is very low considering the significant over-cost resulting from the sole use of bio-BDO. To overcome this issue and to further increase the renewable source content in TPC-ET, Sipol developed an alternative route where part of the soft segment (polyether) in the polymer chain can be substituted with a derivate of ricinoleic acid obtained from vegetable oils hydrolysis. This modification brings an additional amount of renewable source between 20% and 35% with a moderate over-cost. Starting from four selected Sipolprene standard grades, in term of hardness, two modifications have been applied: Step 1: Partial replacement of the polyether PTMG in the chain with derivatives of ricinoleic acid from agro-industrial residues, that is the real innovation driver of this study. Step 2: Substitution of BDO with bio-BDO, obtained from starch and sugar fermentation.
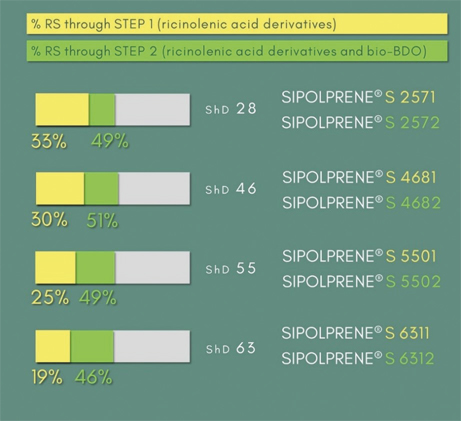
The combination of the two above mentioned modifications allows to achieve a percentage of renewable source in all final products developed (C14/Ctot according to ASTM D6866) not less than 46 %. In this way, for each selected product, two grades have been developed with two renewable sources content levels as described in figure 1.
Features and strengths of Sipolprene S
To better understand the behaviour of the new biobased Sipolprene S range and the extent of this variation in the chemistry of TPC-ET, an in-depth comparative analysis with the related Sipolprene standard grades has been done (tab. 1).
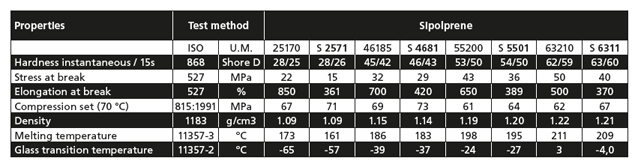
As showed in table 1, the Sipol R & D team have developed biobased alternative grades, maintaining mechanical and thermal properties as close as possible to standard TPC-ET. Moreover, the introduction of the renewable aliphatic moiety in the Sipolprene structure gives technical advantages beyond sustainability. The substitution gives to the final products a comparable thermal behaviour in term of melting temperature, crystallization temperature and Vicat. As expected, the glass transition temperature is slightly affected in comparison to the standard ones generally giving a higher resistance at low temperatures. Regarding the mechanical properties, a minor drop in performance has been observed, specifically stress and elongation at break; while considering hardness as a fixed starting point, density and compression set remained practically unaffected. Polyether segments are well known and studied for their effect on the final polymeric products depending also on their molecular weight and distribution; the introduction of low polarity monomers brings a decrease in water absorption and consequently an increase in water resistance and O2 permeability. In this way the presence of the “green aliphatic monomer” in the chemistry of TPC-ET seems to significantly improve the hydrolysis resistance in comparison to the related standard grades.

As shown in table 2 a comparable chemical resistance was observed; internal tests have been carried out according to ASTM D 543 with the indicated substances: antifreeze, ethanol, hydraulic oil, mineral oil, soap solution, and isododecane. Results after 14 days of immersion at room temperature confirm that the biobased Sipolprene S range shows a good chemical resistance like the standard grades. These results along with an equivalent processability with the standard grades, makes Sipolprene S suitable for different processes, like extrusion and injection moulding. The materials safety requirements are strictly connected to the applications. Sipolprene S offers a similar regulatory package to the standard grades, mainly on food contact compliances, cosmetic, toys regulations and for the absence of substances of concern (Compliance statements and further data are available on request).
Economically … sustainable
Sustainability towards the environment does not often correspond with the financial sustainability in following a more eco-friendly path or solution; furthermore, economical sustainability means, not only minimizing the cost impact of monomers from renewable sources (RS), but rather the development of alternative products industrially feasible in the existing polymerization plant, avoiding any additional costs related to new equipment, and reducing time to market. One of the main Sipol’s goal of this project was exactly the offer of an alternative to the existing TPC-ET product range environmental and economical sustainable.

As mentioned above, there are few possible ways to obtain partially biobased TPC. Considering one of the standard grade Sipolprene 55200 (TPC-ET with hardness Shore D 55, figure 2 shows the additional costs related to three different ways to obtain a partially biobased TPC with comparable properties and performance:
- • with the use of ricinoleic acid derivatives (step 1, Sipolprene S 5501):
- • 25% of RS content, +18% raw materials over cost.
- • with the combination of bio-BDO and ricinoleic acid derivatives (step 2, Sipolprene S 5502): • 49% of RS content, +29% raw materials over cost.
- • To avoid modification in the chemical nature of the polymer, it is possible to substitute both PTMG and BDO with respectively bio-PTMG and bio-BDO. In the case of both replacements, an RS content of 52% can be achieved; although this way leads to a very similar RS content to the one obtained in step 2 of our study, the additional cost on the standard grade is + 86%. The third option was not considered for Sipol’s project because of the economic unsustainability of this solution: notwithstanding the equal renewable sources content to Sipolprene S 5502, the difference in the raw material over cost is unreasonable.
Conclusion
Notwithstanding the advantages of biobased polymers in comparison to the synthetic ones in terms of sustainability, the sole use of renewable raw materials is not enough to make a product truly sustainable. Sipol is already focused on the main aspects of its polymers circularity by developing eco-solutions to minimize both the economic and the environmental impacts: from the use of energy coming only from renewable sources (hydroelectrical, aeolian, biomasses), certified by AXPO, to the use of monomers coming from renewable sources in most of our polymers; in the specific case of Sipolprene S, ricinolenic acid derivatives are obtained from agro-industrial residues. Furthermore, Sipol’s first sustainability report will be issued for the financial year 2022. In order to demonstrate the lower impact on the environment of this technology, LCA studies on Sipolprene S are currently underway. Sipolprene S products are already industrially available and the R & D team is already working on the extension of the hardness range.
Author
E. Bolgiaghi, D. Del Prete
Source
Sipol Spa, press release, 2022-10.
Share
Renewable Carbon News – Daily Newsletter
Subscribe to our daily email newsletter – the world's leading newsletter on renewable materials and chemicals