Tiny plastic particles harm humans and animals when they enter the food chain. Some of them are even considered carcinogenic. Microplastics are mainly produced where movement causes abrasion. In order to prevent this in the future, particularly in skiing and water sports, Hof University of Applied Sciences is currently researching sustainable gliding surfaces made from biodegradable bioplastics. They are intended to replace the existing sliding components on snowboards, skis and water sports equipment.

Studies show: Microplastics are everywhere. It floats through the atmosphere, it snows on the earth, it is found in human and animal excrement and even in the eternal ice of the Arctic, the unsightly evidence of current human civilization has long been detected. The concentration of microplastics is often significantly higher than assumed. Abrasion from skis and snowboards is also clearly detectable on the slopes of winter sports enthusiasts or – in the case of water skis and wakeboards – in the water.
Degradable plastic abrasion
Dr. Natascha Kuhl has therefore been researching a sustainable and environmentally friendly solution at the Institute for Circular Economy of Bio: Polymers at Hof University of Applied Sciences (ibp) as part of the “BioSlide” project since the beginning of 2023:
We want to curb the current environmental pollution caused by visible plastic abrasion, but above all by invisible microplastics. Biodegradable plastics can help with this, as plastic abrasion itself cannot be prevented. Our goal is to develop 100% sustainable gliding surfaces for the ski, snowboard and water sports sector.”- Dr. Natascha Kuhl
Durability and gliding properties required
Conventional gliding surfaces are often made of ultra-high molecular weight polyethylene (PE-UMHW), which is characterized by outstanding gliding properties.
“The challenge therefore lies in the sustainable material formulation, which on the one hand must fulfill a certain long-term stability during use and on the other hand must be completely biodegradable in the event of abrasion. The sustainable sliding surface should have comparable properties to the conventional materials used to date and withstand a period of use of at least 8 years,” says Dr. Natascha Kuhl.
Three project phases
In the course of the two-and-a-half-year project, the researcher’s first task is to develop and process a resistant, gliding polymer compound including biodegradable and biogenic additives. “We repeatedly test the properties of corresponding samples in order to find the ideal composition with the best properties,” explains Dr. Kuhl.

The second year of the project will then focus on optimizing biodegradability and improving the process for processing the newly developed compound for ski or snowboard production. In the third year of the “BioSlide” project, real tests on ski slopes will then take place and – in the best case scenario – preparations for industrial production will already be underway.
Funding and partners
Creative Plastic Solutions (CPS) GmbH, which already produces high-quality plastics for the winter sports sector and works with many well-known ski manufacturers, is involved in the project. Also involved is silbaerg GmbH, a snowboard manufacturer from Chemnitz, which will carry out the real-life tests in particular. The research project is being funded as part of the Central Innovation Program for SMEs (ZIM). Both industrial partners were brokered by neowistra GmbH from Farchant near Munich. The funding and innovation consultancy for companies and research institutions cooperates successfully with the Hof University of Applied Sciences within the framework of various projects.
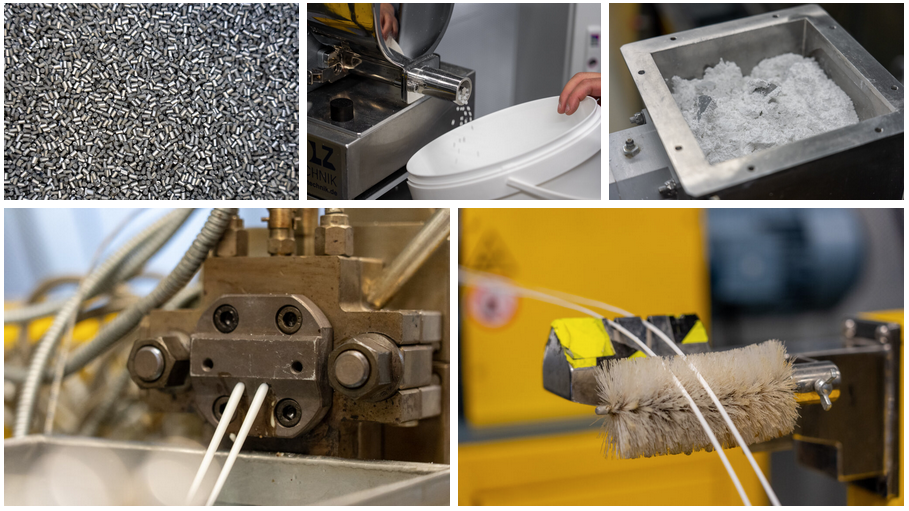
Source
Hof University of Applied Sciences, press release, 2023-11-08.
Supplier
Creative Plastic Solutions (CPS) GmbH
Hochschule Hof - University of Applied Sciences
neowistra GmbH
Silbaerg GmbH
Share
Renewable Carbon News – Daily Newsletter
Subscribe to our daily email newsletter – the world's leading newsletter on renewable materials and chemicals