Concrete degradation is one of the most costly problems of our time. Concrete will always crack, although less so if well-designed and well-constructed. Cracks will allow water and air to enter into the structure and eventually reach the steel reinforcement. When this erodes, it swells, causing more cracks. Concrete degradation of our infrastructure now requires major repair costs – which could have been avoided if we had used self-healing concrete in the first place.
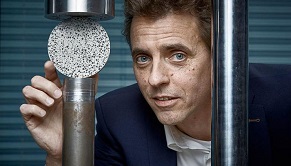
Self-healing concrete by bacterial action
In the past, building regulations may have been tuned too much towards the short term. Self-healing concrete will no doubt raise costs in the short term, but this should be more than offset in the longer term. A promising technology developed by Hendrik Jonkers of Delft Technical University in the Netherlands and commercialized by Basilisk Concrete, uses bacteria. In their self-healing concrete, these bacteria produce limestone if triggered by contact with water and air, and in doing so they repair the crack. Basilisk uses this autonomous repair system in several products that are applicable both for new constructions and in existing structures. For instance, they sell a self-healing agent for fresh concrete mixtures and a self-healing repair mortar for existing structures. And they sell a liquid repair solution for small, narrow cracks in concrete which cannot be sealed with a mortar. After application the liquid forms a gel which seals the crack watertight.
The bacteria then convert the gel into limestone for a permanent seal. Because small cracks are sealed watertight, frost resistance and durability of the structure will increase considerably. Basilisk has formed collaborations with renowned names in the international world of concrete. As a result, they have created a platform for a broad introduction of the technology. Their work has been applied in major projects and has also attracted international attention.
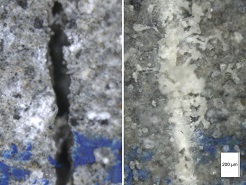
At Ghent University in Belgium, they research more options of self-healing concrete. Bacterial repair is one of them. Like Basilisk, the Ghent researchers embed the bacteria in microcapsules or microgels, where they may survive hundreds of years, whereas they would not be long-lived when introduced into the concrete mixture right away. But they also investigate the use of these hydrogels as such. These gels swell when water enters into the concrete; this partly seals the crack. Then the gel will provide the fluid to the surrounding matrix for internal curing, further hydration and the precipitation of calcium carbonate. In this way, cracks may close completely. Alternatively, encapsulated polymers can be used in self-healing concrete. When a crack appears, the capsules break and the content is released. Due to capillary action, the agent will flow into the crack. After reaction, the crack faces are bonded together and the crack is thus healed. Polyurethane, methyl methacrylate, water repellent agents and elastic polymers are among the polymers used, depending on the primary goal of crack repair: reduction of water permeability, strength restoration, aesthetic view or effective crack sealing. And finally, a form of self-healing concrete can be obtained by adding fly-ash or blast-furnace slag to the concrete mixture. These would seem to be inferior with regard to early age microstructure and strength development, but their self-healing capability can be high, because they will still contain some unreacted particles that can be activated when cracks appear.
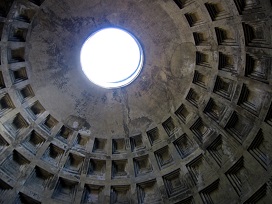
Many options for self-healing concrete
The ultimate goal is to develop concrete materials that continually monitor, regulate, adapt and repair themselves without external intervention. Such self-healing concrete will save both lives and resources, and significantly reduce life cycle carbon emissions. A whole new and promising area of research lies in the incorporation of nano-scale mineral and chemical additives into concrete. This might add new properties, like enhanced mechanical and durability performance, or self-cleaning. Some researchers get excited at the prospect of adding graphene to concrete, which might deliver these new properties and even eliminate the problem of steel corrosion, the biggest and most expensive deterioration problem in concrete.
But will these innovations actually make a breakthrough in the construction industry with its risk-averse attitude? Take the example of Danish concrete hardener, a material with superior properties by its description. This rather inexpensive hardener will do away with the need for maintenance afterwards for decades, because of the strong surface it adds to the concrete, making it very long-lasting and keeping the cracks at bay. Moreover, as the company stresses, the product is environmentally friendly and safe to handle. But in 30 years, they have never had major orders. Although acceptance may also be low because they do not reveal the composition of the product (for commercial reasons), their case seems to testify clearly to the inherent conservatism of the industry, to which we referred in our article on innovative concrete as well.
The ancient Romans already developed a self-healing concrete
And then, the problem of self-healing concrete may have been solved by the ancient Romans already. Some of their concrete structures survive until this day, most famously of course the Pantheon. And piers, objects that nowadays are infamous for concrete degradation under the influence of sea water. That these Roman structures still exist is a 2,000 year achievement that will not easily be met by modern-day structures. The secret seems to be a ‘pozzolanic’ reaction of the material with intrusive water that takes place after construction and produces calcium/aluminium silicate crystals that fill voids and cracks. Strengthening the structures long after the works were finished. Old technologies that need to be revived! Even if this would imply rethinking our the very approach of building with concrete.
Author
Diederik van der Hoeven
Source
Supplier
Ghent University
University of Technology, Delft (NL)
Share
Renewable Carbon News – Daily Newsletter
Subscribe to our daily email newsletter – the world's leading newsletter on renewable materials and chemicals