Wood has historically been marred by wasteful practices generated during shaping processes, driving up costs and environmental impact. Now researchers in materials science and nanoengineering at Rice have developed an additive-free, water-based ink made of lignin and cellulose, the fundamental building blocks of wood. The ink can be used to produce architecturally intricate wood structures via a 3D printing technique known as direct ink writing.
The work was recently published in the journal Science Advances.
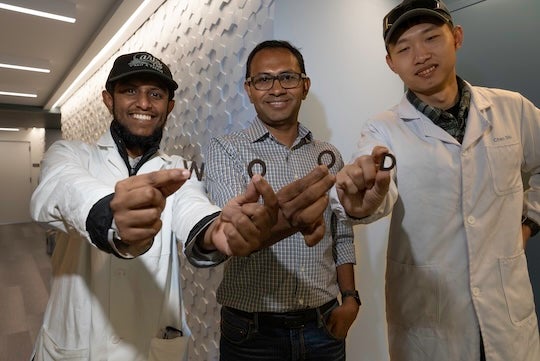
“The ability to create a wood structure directly from its own natural components sets the stage for a more eco-friendly and innovative future,” said Muhammad Rahman, an assistant research professor of materials science and nanoengineering at Rice. “It heralds a new era of sustainable 3D-printed wood construction.”
The implications are far-reaching, potentially revolutionizing industries such as furniture and construction.
“Unlike previous attempts, this method exclusively uses nanoscale wood components for 3D printing, marking a significant advancement in the field,” said Pulickel Ajayan, the Benjamin M. and Mary Greenwood Anderson Professor in Engineering and professor and chair of materials science and nanoengineering.
The university’s research focused on optimizing the composition of the ink by adjusting the ratio of lignin, cellulose nanofibers and nanocrystals while maintaining the natural lignin-cellulose balance, according to both M.S.H Thakur and Chen Shi, lead co-authors on the study.
Although lignin is one of the most abundant biopolymers on Earth, it is the least-valued product in industries, noted Amit Naskar, a project collaborator and senior research and development staff at Oak Ridge National Laboratory.
Post-printing, comprehensive analyses were conducted to assess the surface and internal structures of the 3D printed wood, comparing it to natural wood counterparts. The payoff not only exhibited close similarities to natural wood in texture but also in scent and strength.
Additionally, mechanical tests were performed to evaluate compressive and bending strengths, revealing promising results that surpassed those of natural balsa wood.
The research was supported by Rice and the Rice Shared Equipment Authority and the U.S. Department of Energy’s Office of Science, Basic Energy Sciences and Engineering Division under FWPERKCK60.
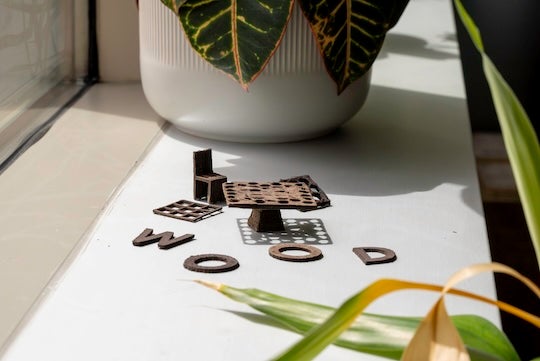
Author
Marcy de Luna
Source
Rice University, press release, 2024-03-19.
Supplier
ORNL Oak Ridge National Laboratory
Rice University, Houston
Science Advances Journal
Share
Renewable Carbon News – Daily Newsletter
Subscribe to our daily email newsletter – the world's leading newsletter on renewable materials and chemicals