Start for an EU-wide collaborative project: Under the leadership of the French company Fairbrics SAS, 17 project partners from 7 European countries are coming together. The common goal is to produce end products from polyester in a closed cycle using industrial CO2 emissions and to bring them to market maturity. The DITF produce synthetic fibers from plastics of non-fossil origin.
In order to achieve the European climate targets, the aim is to achieve a long-term and sustainable reduction in greenhouse gases. To achieve this, CO2 emissions must be reduced in the energy sector, in industry, and in households and small consumers. This is the starting point for the EU-wide collaborative project ‘Threading CO2‘, which is funded under the EU’s Horizon funding program. The project will bring products made of environmentally friendly polyester (PET) to market maturity. The technological basis has been developed by Fairbrics SAS from France. It involves the production of monoethylene glycol (MEG), the starting material for the manufacture of polyester, using CO2 extracted from industrial waste gases. This is a completely new approach, because in the classic process fossil raw materials are consumed for the production of polyester. In this way, not only is the release of CO2 into the atmosphere directly prevented. The CO2 also contributes to increased added value by being incorporated into the production of high-quality textile products. The core of the project is the technological upscaling of the new MEG synthesis process in pilot plants, paving the way for industrial production.
In the EU joint project, 17 project partners will contribute their special expertise and further develop the process technologically and make it suitable for industrial use. Within the consortium, DITF Denkendorf will take on the task of accompanying the upscaling and taking the step ‘from molecule to material’: From the sustainably produced monoethylene glycol, polyesters are synthesized in our own laboratories, spun into fibers, textured and further processed. The aim is to test whether the quality of the polyester and its spinnability and processability in the textile value chain are comparable with conventional polyester.
The project partners Faurecia and Les Tissages de Charlieu process the fibers and textiles into car seats and clothing so that the quality can also be assessed in the end product. The subsequent recyclability of the products will also be tested at the DITF. In addition, a security marking is to be developed for this CO2-based polyester to protect it from product piracy.
The scientists at the DITF have many years of experience in polymer production and processing into textiles. This enables them to specifically impart a specific property profile to plastics and the synthetic fibers spun from them. Through their work on the collaborative project, they are helping to produce fiber-based materials from the sustainably and environmentally friendly produced MEG that perfectly meet the requirements of end users.
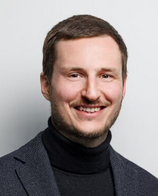
Contact
Dr. rer. nat. Simon König
Deputy Head of Competence Center Chemical Fibers & Nonwovens
T +49 (0)711 93 40-186
E simon.koenig@ditf.de
Source
DITF, press release, 2023-02-23.
Supplier
DITF – Deutsche Institute für Textil- und Faserforschung Denkendorf
Fairbrics
Faurecia
Horizon 2020
Les Tissages de Charlieu
Share
Renewable Carbon News – Daily Newsletter
Subscribe to our daily email newsletter – the world's leading newsletter on renewable materials and chemicals