The new chemical process is not limited to wind turbine blades but works on many different so-called fibre-reinforced epoxy composites, including some materials that are reinforced with especially costly carbon fibres.
Thus, the process can contribute to establishing a potential circular economy in the wind turbine, aerospace, automotive and space industries, where these reinforced composites, due to their light weight and long durability, are used for load-bearing structures.
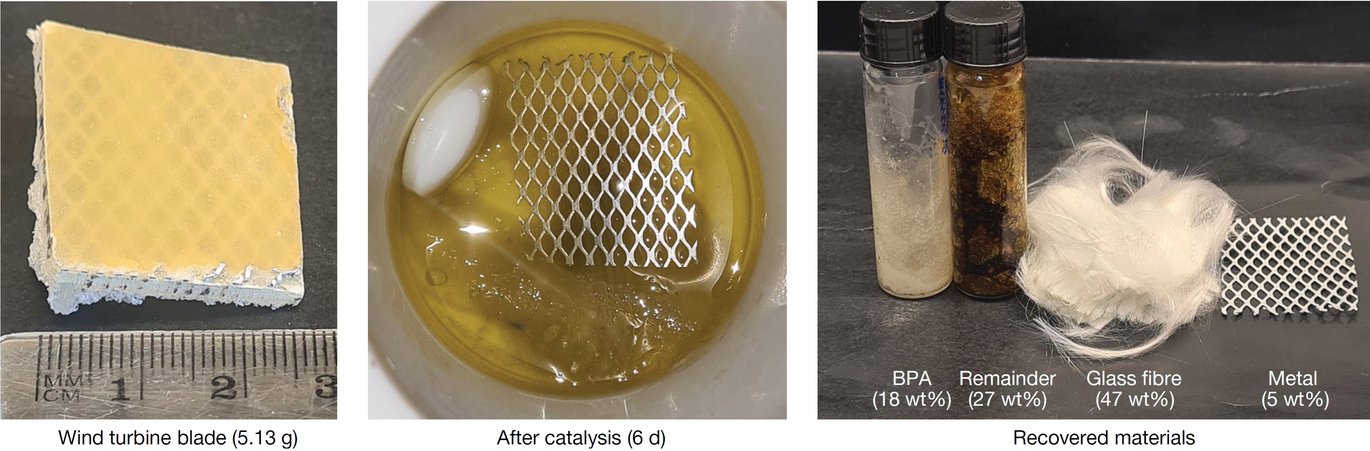
Being designed to last, the durability of the blades poses an environmental challenge. Wind turbine blades mostly end up at waste landfills when they are decommissioned, because they are extremely difficult to break down.
If no solution is found, we will have accumulated 43 million tonnes of wind turbine blade waste globally by 2050.
The newly discovered process is a proof-of-concept of a recycling strategy that can be applied to the vast majority of both existing wind turbine blades and those presently in production, as well as other epoxy-based materials.
The results have just been published in the leading scientific journal Nature, and Aarhus University, together with the Danish Technological Institute, have filed a patent application for the process.
Specifically, the researchers have shown that by using a ruthenium-based catalyst and the solvents isopropanol and toluene, they can separate the epoxy matrix and release one of the epoxy polymer’s original building blocks, bisphenol A (BPA), and fully intact glass fibres in a single process.
However, the method is not immediately scalable yet, as the catalytic system is not efficient enough for industrial implementation – and ruthenium is a rare and expensive metal. Therefore, the scientists from Aarhus University are continuing their work on improving this methodology.
“Nevertheless, we see it as a significant breakthrough for the development of durable technologies that can create a circular economy for epoxy-based materials. This is the first publication of a chemical process that can selectively disassemble an epoxy composite and isolate one of the most important building blocks of the epoxy polymer as well as the glass or carbon fibres without damaging the latter in the process,” says Troels Skrydstrup, one of the lead authors of the study.
Troels Skrydstrup is a professor at the Department of Chemistry and the Interdisciplinary Nanoscience Center (iNANO) at Aarhus University.
The research is supported by the CETEC project (Circular Economy for Thermosets Epoxy Composites), which is a partnership between Vestas, Olin Corporation, the Danish Technological Institute and Aarhus University.
Author
Peter F. Gammelby
Source
Aarhus University, press release, 2023-04-27.
Supplier
Aarhus University
Danish Technological Institute
nature (Journal)
Olin Corporation
Vestas®
Share
Renewable Carbon News – Daily Newsletter
Subscribe to our daily email newsletter – the world's leading newsletter on renewable materials and chemicals