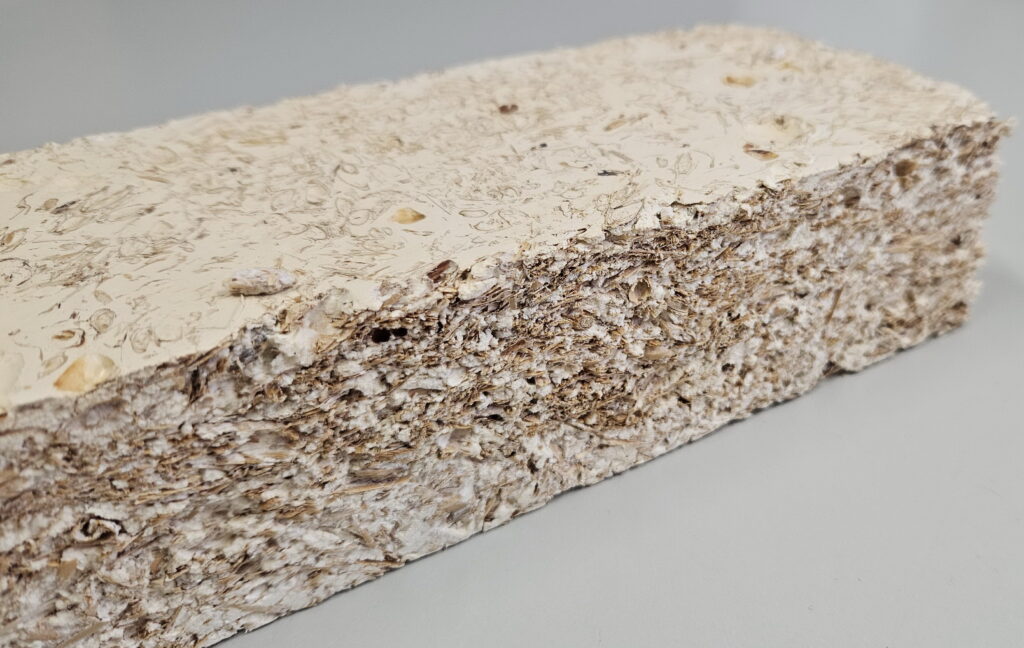
It is easy to spot in mould with the naked eye: the fine mycelial network, which mostly grows hidden in the ground or in biomass. Mycelium possesses properties that can be very useful in avoiding environmentally harmful packaging waste. Scientists from the Universities of Göttingen and Bremen, as well as from the BIBA – Bremer Institut für Produktion und Logistik, are now researching new biodegradable mycelium composite materials for biodegradable packaging applications. They develop adapted production methods by keeping the entire product life cycle in mind and use artificial intelligence for promising material combinations.
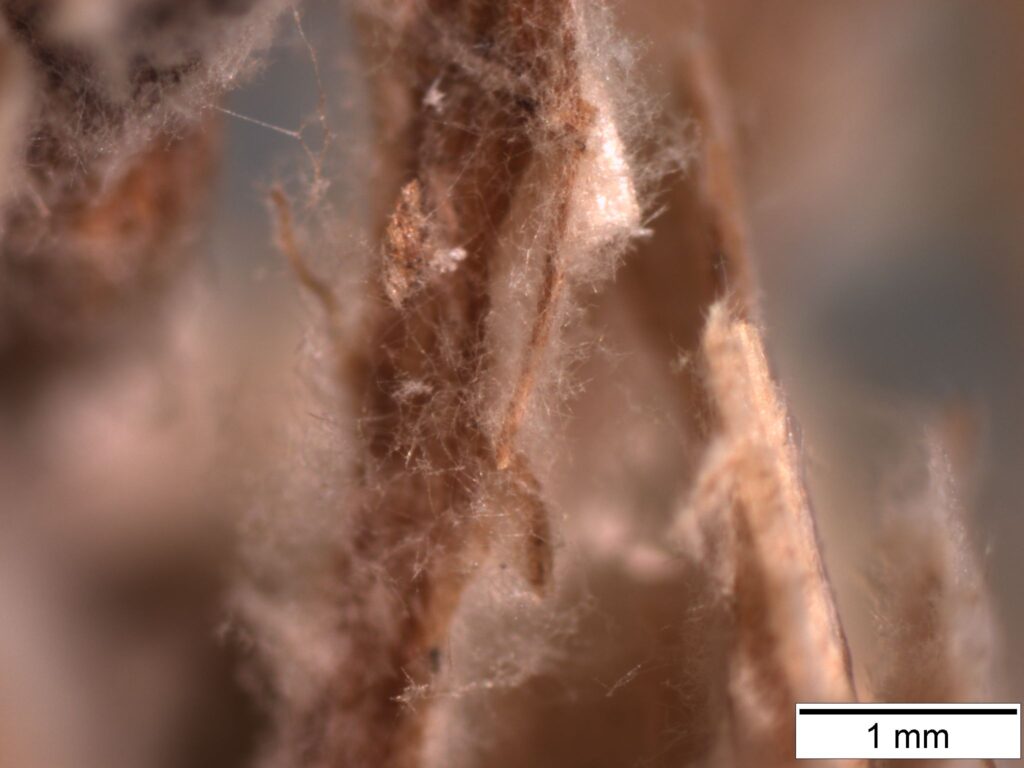
Mycelium has the potential to transform biomass with its thread-like hyphae into a high-performance composite material. The goal of this project is to develop an integrated methodology for the material, process, and product development of mycelium composite materials. This methodology will address the current challenges of the product life cycle in terms of material selection, material preparation, recycling, and reuse.
The focus is specifically on the use of locally available organic residues and waste materials to enable short transport routes and sustainable production. These raw materials are sterilized in an energy-saving way, combined, and processed with consistent quality, so that production, use, and recycling are possible at the highest quality. Above all, the best possible material cycle should be guaranteed.
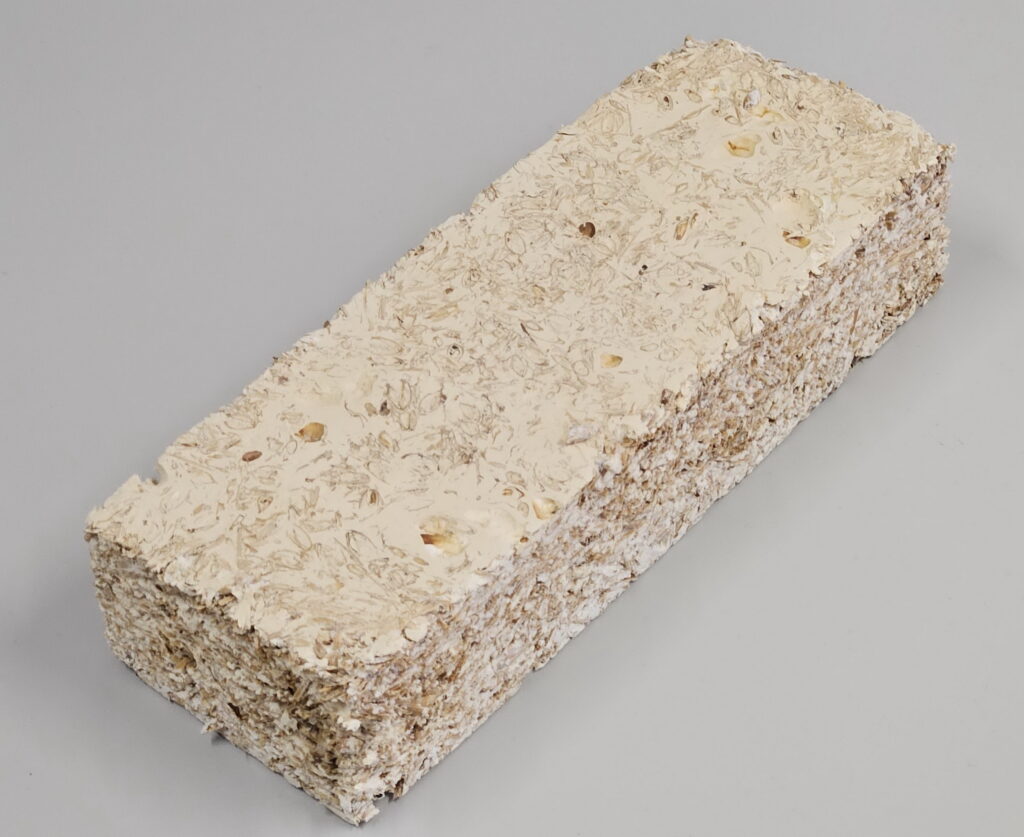
Research case study: Insulated cooler box
A concrete example of the use of mycelium-based materials is cooler boxes for shipping. For this purpose, the research project aims to implement a closed material cycle. It also examines the secondary use of the material as shredded bulk for shipping packaging and even as base material for further mycelium cooler boxes.
Utilizing artificial intelligence
Another highlight of this project is the use of artificial intelligence (AI) to identify optimal starting material combinations and optimize process control. The use of the latest AI technologies ensures that the materials can be made efficiently and sustainably.
“Increasingly a success factor”
Packaging waste in Germany has more than doubled in the past thirty years, and the trend is ongoing.
“Legal regulations also demand changes towards environmentally and climate-friendly products and processes,” says BIBA’s director and project initiator Professor Michael Freitag. “The use of new, ecologically safe materials and corresponding processes are becoming a success factor. The research in the ‘MycelCycle’ project with its holistic considerations are intended to contribute to more sustainable economic activity and an efficient and effective circular economy.”
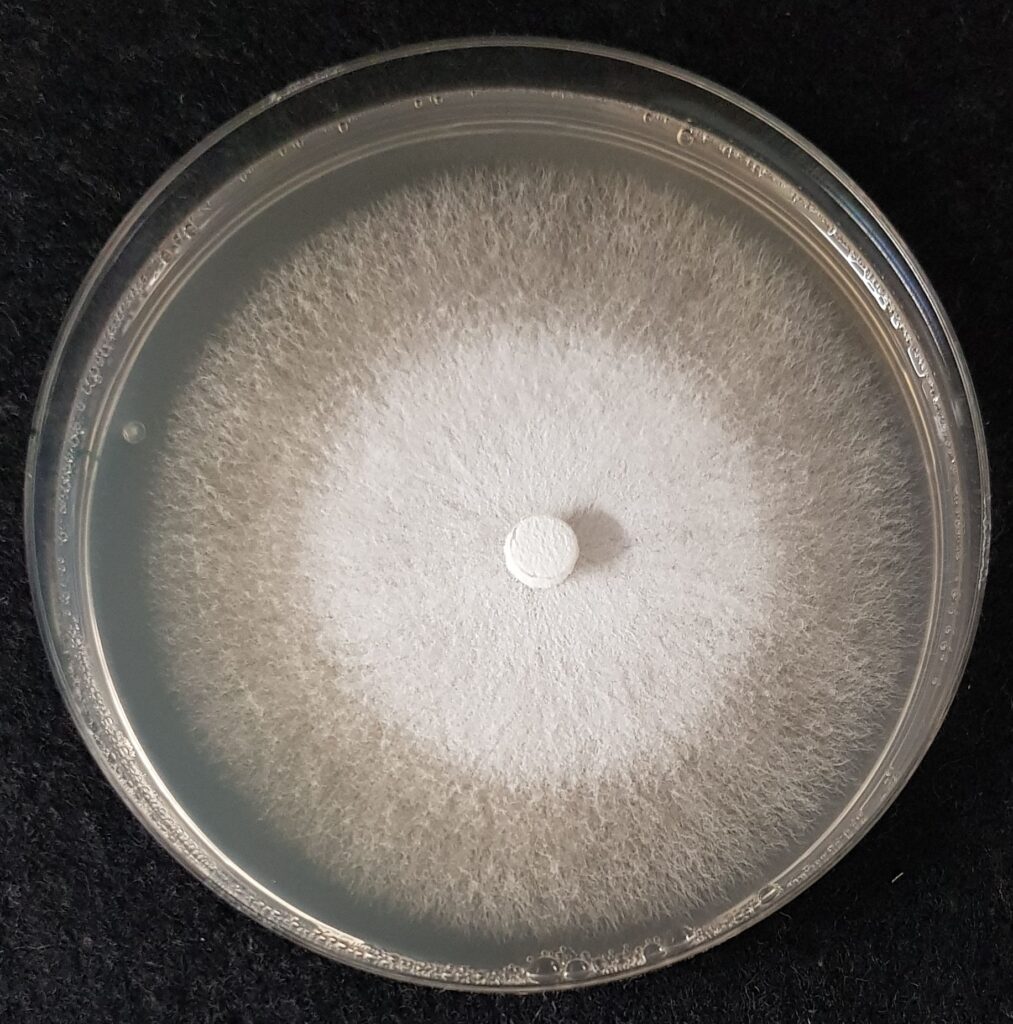
Transfer and dialogue
Another project goal is to share and disseminate the knowledge gained, exchange ideas constructively with all stakeholders from research and practice and thus receive new impulses. In this way, new opportunities for the development of mycelium products for various industries should also be recognized. For further information on this project and to participate in symposia and workshops, please contact:
Dr.-Ing. Michael Lütjen (BIBA)
phone: +49 421 218-50 123
email: ltj@biba.uni-bremen.de.
Key data about the project “MycelCycle”
The 4-year research project “MycelCycle” (Integrated material, process and product development methodology for product life-cycle optimised mycelium-based packaging products as part of circular economy) is funded by the VolkswagenStiftung with 1.26 million euros. Research partners are the Department of Molecular Wood Biotechnology and Technical Mycology at the Faculty of Forest Sciences and Forest Ecology of the University of Göttingen, the Institute for Integrated Product Development (BIK) within the Faculty of Production Engineering – Mechanical Engineering and Process Engineering of the University of Bremen and the BIBA – Bremer Institut für Produktion und Logistik at the University of Bremen.

Source
BIBA (Bremen University), press release, 2024-03-12.
Supplier
BIBA (Universität Bremen)
Institut für integrierte Produktentwicklung (BIK)
Universität Bremen
VolkswagenStiftung
Share
Renewable Carbon News – Daily Newsletter
Subscribe to our daily email newsletter – the world's leading newsletter on renewable materials and chemicals