MIT engineers aim to produce totally green, carbon-free hydrogen fuel with a new, train-like system of reactors that is driven solely by the sun.
In a study appearing today in Solar Energy Journal, the engineers lay out the conceptual design for a system that can efficiently produce “solar thermochemical hydrogen.” The system harnesses the sun’s heat to directly split water and generate hydrogen — a clean fuel that can power long-distance trucks, ships, and planes, while in the process emitting no greenhouse gas emissions.
Today, hydrogen is largely produced through processes that involve natural gas and other fossil fuels, making the otherwise green fuel more of a “grey” energy source when considered from the start of its production to its end use. In contrast, solar thermochemical hydrogen, or STCH, offers a totally emissions-free alternative, as it relies entirely on renewable solar energy to drive hydrogen production. But so far, existing STCH designs have limited efficiency: Only about 7 percent of incoming sunlight is used to make hydrogen. The results so far have been low-yield and high-cost.
In a big step toward realizing solar-made fuels, the MIT team estimates its new design could harness up to 40 percent of the sun’s heat to generate that much more hydrogen. The increase in efficiency could drive down the system’s overall cost, making STCH a potentially scalable, affordable option to help decarbonize the transportation industry.
“We’re thinking of hydrogen as the fuel of the future, and there’s a need to generate it cheaply and at scale,” says the study’s lead author, Ahmed Ghoniem, the Ronald C. Crane Professor of Mechanical Engineering at MIT. “We’re trying to achieve the Department of Energy’s goal, which is to make green hydrogen by 2030, at $1 per kilogram. To improve the economics, we have to improve the efficiency and make sure most of the solar energy we collect is used in the production of hydrogen.”
Ghoniem’s study co-authors are Aniket Patankar, first author and MIT postdoc; Harry Tuller, MIT professor of materials science and engineering; Xiao-Yu Wu of the University of Waterloo; and Wonjae Choi at Ewha Womans University in South Korea.
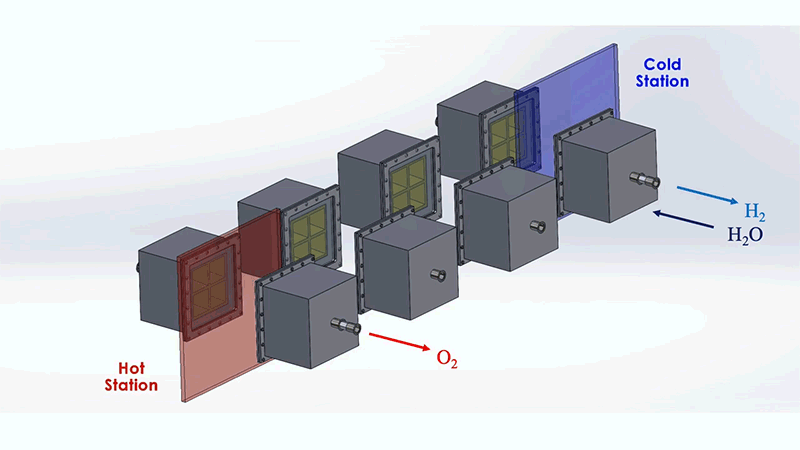
Solar stations
Similar to other proposed designs, the MIT system would be paired with an existing source of solar heat, such as a concentrated solar plant (CSP) — a circular array of hundreds of mirrors that collect and reflect sunlight to a central receiving tower. An STCH system then absorbs the receiver’s heat and directs it to split water and produce hydrogen. This process is very different from electrolysis, which uses electricity instead of heat to split water.
At the heart of a conceptual STCH system is a two-step thermochemical reaction. In the first step, water in the form of steam is exposed to a metal. This causes the metal to grab oxygen from steam, leaving hydrogen behind. This metal “oxidation” is similar to the rusting of iron in the presence of water, but it occurs much faster. Once hydrogen is separated, the oxidized (or rusted) metal is reheated in a vacuum, which acts to reverse the rusting process and regenerate the metal. With the oxygen removed, the metal can be cooled and exposed to steam again to produce more hydrogen. This process can be repeated hundreds of times.
The MIT system is designed to optimize this process. The system as a whole resembles a train of box-shaped reactors running on a circular track. In practice, this track would be set around a solar thermal source, such as a CSP tower. Each reactor in the train would house the metal that undergoes the redox, or reversible rusting, process.
Each reactor would first pass through a hot station, where it would be exposed to the sun’s heat at temperatures of up to 1,500 degrees Celsius. This extreme heat would effectively pull oxygen out of a reactor’s metal. That metal would then be in a “reduced” state — ready to grab oxygen from steam. For this to happen, the reactor would move to a cooler station at temperatures around 1,000 C, where it would be exposed to steam to produce hydrogen.
Rust and rails
Other similar STCH concepts have run up against a common obstacle: what to do with the heat released by the reduced reactor as it is cooled. Without recovering and reusing this heat, the system’s efficiency is too low to be practical.
A second challenge has to do with creating an energy-efficient vacuum where metal can de-rust. Some prototypes generate a vacuum using mechanical pumps, though the pumps are too energy-intensive and costly for large-scale hydrogen production.
To address these challenges, the MIT design incorporates several energy-saving workarounds. To recover most of the heat that would otherwise escape from the system, reactors on opposite sides of the circular track are allowed to exchange heat through thermal radiation; hot reactors get cooled while cool reactors get heated. This keeps the heat within the system. The researchers also added a second set of reactors that would circle around the first train, moving in the opposite direction. This outer train of reactors would operate at generally cooler temperatures and would be used to evacuate oxygen from the hotter inner train, without the need for energy-consuming mechanical pumps.
These outer reactors would carry a second type of metal that can also easily oxidize. As they circle around, the outer reactors would absorb oxygen from the inner reactors, effectively de-rusting the original metal, without having to use energy-intensive vacuum pumps. Both reactor trains would run continuously and would enerate separate streams of pure hydrogen and oxygen.
The researchers carried out detailed simulations of the conceptual design, and found that it would significantly boost the efficiency of solar thermochemical hydrogen production, from 7 percent, as previous designs have demonstrated, to 40 percent.
“We have to think of every bit of energy in the system, and how to use it, to minimize the cost,” Ghoniem says. “And with this design, we found that everything can be powered by heat coming from the sun. It is able to use 40 percent of the sun’s heat to produce hydrogen.”
“If this can be realized, it could drastically change our energy future — namely, enabling hydrogen production, 24/7,” says Christopher Muhich, an assistant professor of chemical engineering at Arizona State University, who was not involved in the research. “The ability to make hydrogen is the linchpin to producing liquid fuels from sunlight.”
In the next year, the team will be building a prototype of the system that they plan to test in concentrated solar power facilities at laboratories of the Department of Energy, which is currently funding the project.
“When fully implemented, this system would be housed in a little building in the middle of a solar field,” Patankar explains. “Inside the building, there could be one or more trains each having about 50 reactors. And we think this could be a modular system, where you can add reactors to a conveyor belt, to scale up hydrogen production.”
This work was supported by the Centers for Mechanical Engineering Research and Education at MIT and SUSTech.
Paper
Author
Jennifer Chu
Source
MIT, press release, 2023-10-16.
Supplier
Arizona State University
EWHA Womans University
Massachusetts Institute of Technology (MIT)
University of Waterloo
Share
Renewable Carbon News – Daily Newsletter
Subscribe to our daily email newsletter – the world's leading newsletter on renewable materials and chemicals