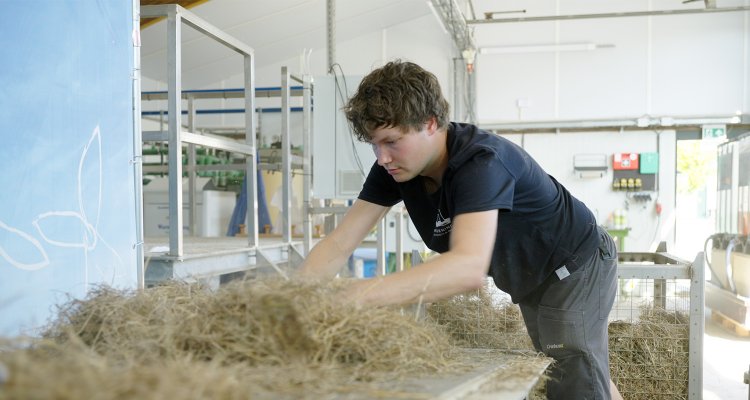
‘This saves trees in Scandinavia as well as removing the need to transport pulp or paper to the Netherlands.’
There is a pleasant grassy smell in the test room of ACCRES in Lelystad, WUR’s trial and development location for sustainable energy and green raw materials. With a sweeping gesture, Kimberly Wevers, researcher at Wageningen Plant Research, chucks armfuls of verge grass onto a conveyor belt. A camera that has been trained using 15,000 photos carries out a rapid scan for foreign objects such as cans or agricultural plastic. ‘We even found a pair of underpants once,’ says the biotechnologist. The objects are discarded through a hole in the conveyor belt system.
The raw grass is deposited in a cage and taken to a specially developed digester where a culture of microorganisms is sprayed on from a shower head. ‘The bacteria convert the sugars into biogas, which we can use for refining the grass further,’ explains Wevers.
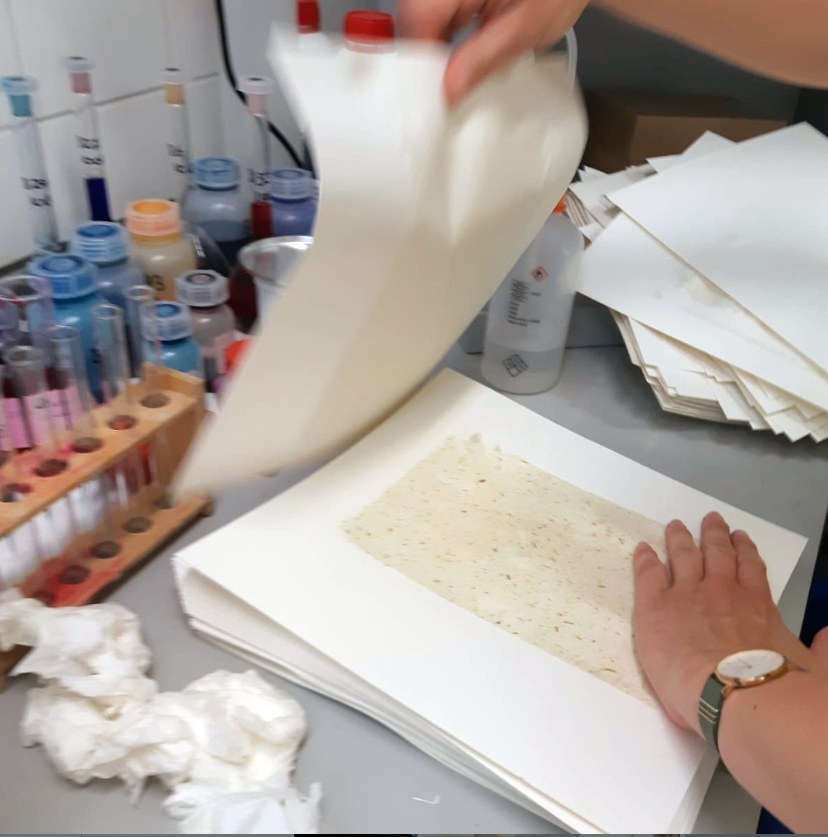
The grass then undergoes a series of additional treatments, such as washing, an alkaline bath, and drying and cutting in a screw press and a second-hand mincer. The researcher shows the final result: snippets of fibrous material that is clean and devoid of sand grains. ‘These smaller fibres link together nicely during the paper-making process,’ says Wevers.
Now that four years of Wageningen research have shown grass to be a viable raw material, the Schut paper factory in Heelsum, the oldest in the Netherlands, is set to start producing paper from verge grass next year. Wevers shows business cards, greetings cards and artists’ paper made by Schut using materials other than wood fibre. ‘Schut has a great deal of experience making paper with fibres from cocoa shells or even worn-out jeans.’
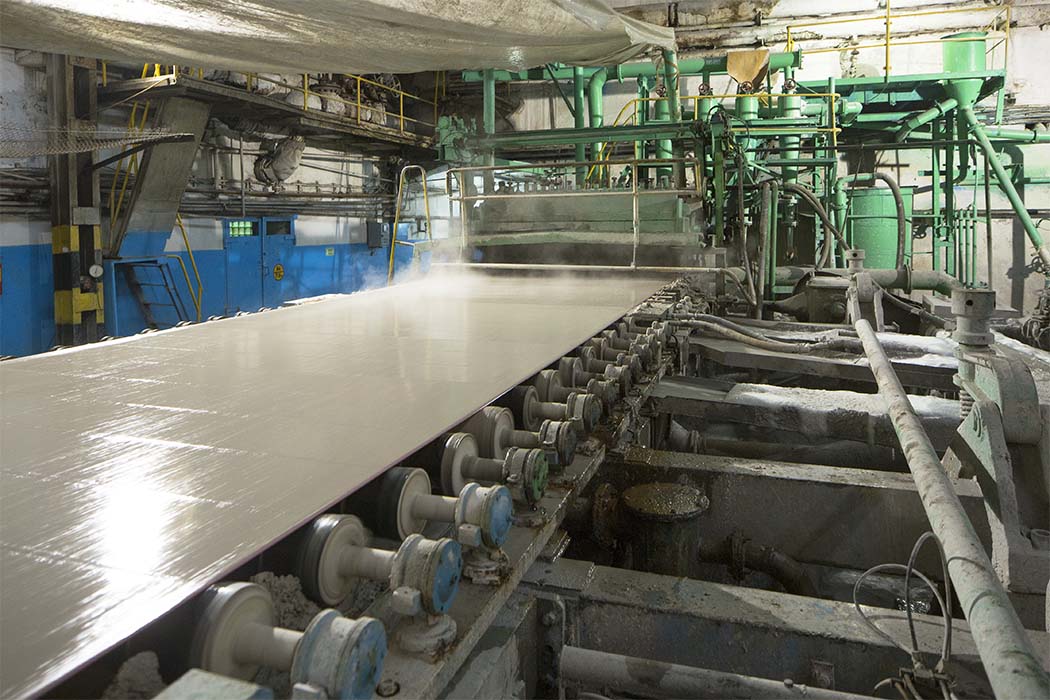
Such special paper for niche markets will soon be among the possibilities, says Wevers, as will packaging material such as cardboard, egg boxes or tomato trays. But grass paper won’t be coming out of the laser printer any time soon. ‘The technical specifications for that are too demanding at present.’ Anyway, the market for cardboard products has better prospects: we are printing less and less, but we are ordering ever more packages online.
Grass with added value
The research in Lelystad is part of the GO-GRASS EU project. The EU programme Horizon 2020 funded four demo projects as part of GO-GRASS, aiming to develop ‘grass-based circular business models for rural areas’ in four countries. More than a fifth of the surface area in Europe is grassland and the idea is to see if that grass can have value as something other than just cattle feed.

In Denmark, researchers are exploring methods for extracting proteins from young grass. ‘Denmark has a lot of pigs, which mainly eat soya as they have difficulty digesting grass,’ says Wevers. If the Danish pigs were able to consume the grass protein, it would reduce soya imports. In Germany, researchers are turning grass into a kind of charcoal – biochar – that can be used to enrich marginal soils with carbon. And in Sweden, researchers are using the grass as litter for stables. All four projects have been a success, says Wevers.
Tough and woody
The Dutch grass paper and cardboard are made from grass from verges and nature areas.
‘This grass is mown once or maybe twice a year at most, so it’s tough and woody and doesn’t contain much protein,’ explains Kimberly Wevers. ‘Verge grass in particular has a negative economic value as it costs money to get rid of it. The Directorate-General for Public Works and the provincial authorities are required to remove it and turn it into compost. Or they leave it lying there. But that is exactly the kind of grass we want. The woodier the better – the tougher the paper. There isn’t enough grass in the Netherlands to satisfy the entire demand for paper, but it’s suitable for niche markets.’
When asked whether the contamination of verge grass with substances from exhaust gases and the rubber particles in car tyres is a problem, Wevers replies: ‘It turns out they mainly end up in the first metre of the verge next to the asphalt. The Public Works directorate can designate the cleanest sections of verge for our raw materials. But the scope of our study didn’t include traffic pollution.’
By turning the verge grass and – much cleaner – grass from nature areas into paper fibres, the grass acquires a positive commercial value and contributes to the regional economy.
According to Wevers, this could become a new business model for composting companies. They already process a lot of grass clippings from the region and they could therefore also turn the grass into fibres for paper applications.
‘This saves trees in Scandinavia as well as removing the need to transport pulp or paper to the Netherlands,’ she says, summing up the benefits. A broad lifecycle analysis shows that ‘grass-based pulp’ scores better from an environmental perspective than conventional wood pulp.
Wevers: ‘It is better in terms of both water consumption and energy consumption. The latter benefit is mainly because we first extract biogas from the grass, which we then use in the production process.’
Source
Wageningen University, press release, 2024-01-02.
Supplier
Horizon 2020
Wageningen University
Share
Renewable Carbon News – Daily Newsletter
Subscribe to our daily email newsletter – the world's leading newsletter on renewable materials and chemicals