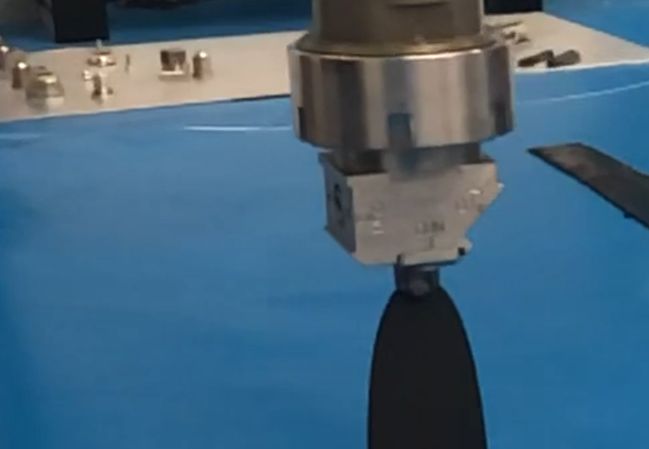
Driving comfort in modern cars includes a low noise level. To achieve this, sound damping systems are used inside the vehicle. In a joint research project, ECOPOX GmbH & Co. KG and the Fraunhofer Institute for Microstructure of Materials and Systems IMWS want to make a novel, ecological liquid plastic suitable for this application. It is to be easy to process, cost-effective and significantly more environmentally compatible than the solutions currently available on the market.
Fans of classic cars appreciate the unusual design of these cars, which exude the charm of bygone eras with their often massive construction and durable materials. However, if you sit in a classic car while driving, you quickly notice a disadvantage compared to today’s vehicles: it is unusually loud. Unlike the model generations of yesteryear, modern cars are equipped with sophisticated soundproofing systems so that the noise from the engine, tires or body has as little impact as possible on travel comfort.
Common solutions for the sound deadening compounds (LASD; Liquid Applied Sound Deadener) used in this process in the vehicle interior are plastics used in solid (bitumen mats or epoxy systems) and liquid form (usually as acrylate dispersions). However, these plastics have their disadvantages in the production, processing, storage or use in cars, such as high weight, the use of environmentally harmful substances or odor emissions. ECOPOX GmbH & Co. KG from Bitterfeld-Wolfen therefore wants to bring new sound-absorbing compounds for automotive construction to market and is being supported by the Fraunhofer IMWS in a research project that will run until April 30, 2022. The special feature of the new approach is that, as far as possible, the development will focus on the use of particularly sustainable raw materials. In the manufacturing process and in use, the focus is also on environmental friendliness, resource efficiency, excellent processability and health compatibility.
“ECOPOX has already developed and applied for a patent for the material, which consists largely of natural, renewable raw materials. This ecological liquid plastic shows promising material behavior for use in soundproofing systems, particularly with regard to vibration and damping behavior. In the project, we want to investigate the relationships between chemical structure, processing methods, microstructure and application-relevant physical properties in more detail. In this way, we are paving the way for transfer to large-scale production and application in automotive engineering. This is because manufacturers make very precise specifications regarding the properties and quality of such materials,” explains Prof. Mario Beiner, who heads the project at the Fraunhofer IMWS.
The research institute from Halle (Saale) contributes its extensive expertise in the field of material-specific structure-processing-property relationships, including the development of material models. Particularly relevant to the project are the competencies on flow properties of complex liquid systems (such as polymer melts and solutions filled with micro- and nanoparticles) as well as on the description, prediction and control of structure formation processes during the curing of liquid multiphase systems, which also play a decisive role in the application and drying process of the silencing compounds, determining the product properties. Equally significant are the possibilities of the Fraunhofer IMWS to elucidate the microstructure of materials, for which, for example, spectroscopic and electron microscopic methods are used in the project.
The existing ECOPOX formulation is to be investigated and optimized with regard to the fillers used, processability, thermal stability and crosslinking properties. The formulation, which will be further developed in terms of material structure and composition, is expected to offer advantages in terms of sprayability, pumpability, baking temperature and mechanical behavior. The in-depth findings will make it possible to control the damping properties specifically according to the specifications of end users, to shorten cycle times in production or to enable longer service lives.
“We can contribute and further develop our knowledge of structure formation processes during the mixing and curing of highly filled polymer systems in the project. This should help establish a new, environmentally friendly solution for an important automotive application area that overcomes the weaknesses of previous silencing systems”, says Beiner.

Source
Supplier
Fraunhofer-Institut für Mikrostruktur von Werkstoffen und Systemen (IMWS)
Share
Renewable Carbon News – Daily Newsletter
Subscribe to our daily email newsletter – the world's leading newsletter on renewable materials and chemicals