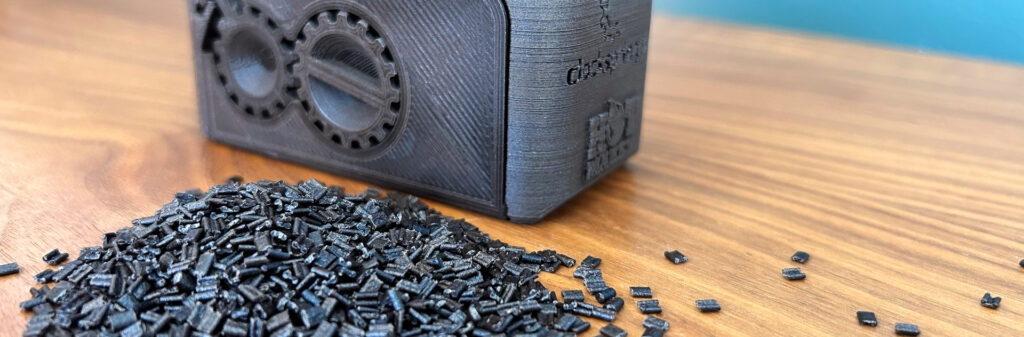
With a focus on hydrolysis lignin valorization, the Synergy Horizon group of companies transforms lignin, a biopolymer that is often discarded as a by-product of the bioethanol industry, into valuable products for various applications.
Their strong competencies involve lignin purification, its chemical modification and functionalization. They offer lignin-derived products for various applications, such as oil and gas extraction, battery production, water treatment, animal feed and more.
With our compounding expertise and our project partner’s unique knowledge of lignin preparation, we have succeeded in incorporating up to 30% lignin into the PLA matrix and producing a compound with natural antioxidant capacity/activity, enhanced mechanical properties, and controlled biodegradability. – Lars Darnedde, Process engineering development and project manager, KraussMaffei Extrusion
From waste product to filler
The group member, Synergy Horizon Poland Sp. z o.o., has also been recently developing a process at its Polish site in Poznan for the production of free-flowing lignin powder that can be metered into the extruder as a filler. Lignin is a 100% natural substance that is second to cellulose as the most abundant organic material on Earth.
Lignin can be extracted from lignocellulosic biomass by various methods. One of these methods is the hydrolysis of biomass for bioethanol production, which generates hydrolysis lignin as a byproduct. Hydrolysis lignins have unique properties that make them stand out from other types of lignin.
Around 50 million tons of lignin, including hydrolysis lignin, are produced annually worldwide as a waste product from wood processing in the paper and bioethanol industries, 98% of which is incinerated. Various research projects have already dealt with the valuable renewable bioresource, but its use as a filler in a biopolymer matrix is so far unique.
“However, processing hydrolysis lignin is not an easy task,” knows Alexander Gonchar, the head of research and development at Synergy Horizon, and is proud of the fact that, thanks to intensive development work, his company now operates a commercial production line for manufacturing lignin powder.
Successful process optimization: KraussMaffei integrates up to 30% lignin into PLA matrix
KraussMaffei has demonstrated the incorporation of the natural raw material into the PLA matrix in its newly established technical center at the Laatzen site. Both the laboratory extruder, a ZE Blue Power 28, and the small ZE Blue Power 42 production compounder succeeded in incorporating up to 30% lignin.
“We have specially adapted the screw configuration to the lignin with heavy-sensitive mixing elements, operate at a low temperature of 160°C maximum, and use both a 6 D-long filling zone and side degassing,” Lars Darnedde gives an insight into the process configuration.
The ZE BluePower generation with its optimum Da/di of 1.55 offers all these possibilities “out of the box” and is thus perfectly suited for processing these shear- and temperature-sensitive polymers.
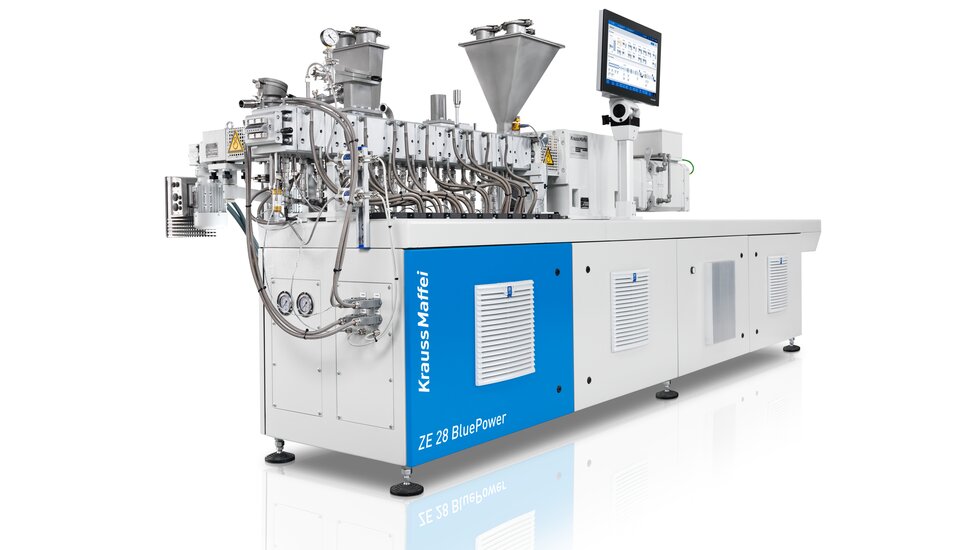
The fact that both the process arrangement of the compounding extruder and the preparation of the lignin at Synergy Horizon are perfect has also been confirmed by extensive mechanical tests. Compared to pure PLA, the lignin reinforcement enables flexural and tensile modulus to be increased by around 30%.
It could be useful in packaging applications where the material needs to be stiff enough to hold its shape under load. Another advantage is that lignin adds sufficient antioxidant capacity that can help particularly in food packaging application to prevent oxidation of the food and maintain its quality and safety by inhibiting the radical oxidation and preventing the formation of off-flavors, odors, or toxic compounds.
Moreover, the biocompound with lignin has no odor unlike other type of lignin, which makes it more suitable for food packaging. A novel bicompound that exhibits antioxidant properties could be applied to biodegradable plastics for agricultural purposes, such as mulch films, to protect them from oxidative degradation.
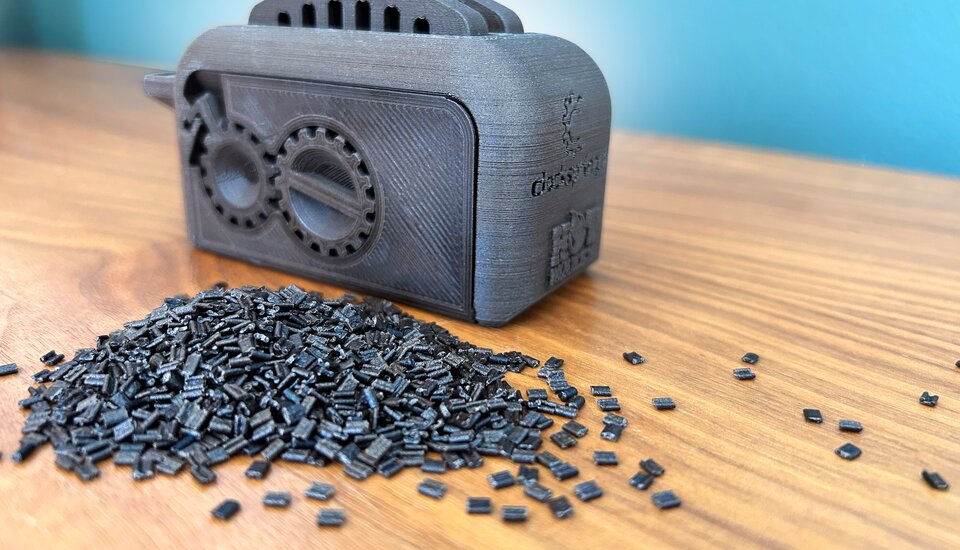
© KraussMaffei
Unlike pure PLA, which has limited biodegradability due to its dependence on specific enzymes and industrial conditions, PLA biocompounds containing lignin exhibit enhanced biodegradation properties with a biodegradation rate of more than 90% in 99 days.
Contact
Lars Darnedde
Process engineering development and project manager, KraussMaffei Extrusion
E-Mail: lars.darnedde@kraussmaffei.com
Source
KraussMaffei, press release, 2024-01-19.
Supplier
KraussMaffei Berstorff
Synergy Horizon Group
Share
Renewable Carbon News – Daily Newsletter
Subscribe to our daily email newsletter – the world's leading newsletter on renewable materials and chemicals