“You can’t connect the dots looking forward; you can only connect them looking backwards. So, you have to trust that the dots will somehow connect in your future.” – Steve Jobs
Here, I have taken the liberty to connect dots in hindsight with one of the largest ventures in the bio-fuels space i.e., KiOR. The idea not to point fingers at respective personnel, but to learn a lesson and design improvised sustainable solutions for a better tomorrow.
The overall failure of KiOR can essentially be narrowed down to three text-book cases:
- Utilizing (Incorrect/Underdeveloped) Catalyst Systems for Upgrading Biomass,
- Disregarding Inherent Oxygen Content in Biomass,
- Diseconomies of Scale.
I. Utilizing (Incorrect/Underdeveloped) Catalyst Systems for Upgrading Biomass
Catalysis has played a very important role during the 2nd half of the 20th century in the development of refining and petrochemical industries. Exhibit 1. Indicates some of the important dates that marked their history. With the exception of steam cracking, which has always played a leading role in petrochemicals, the importance of purely thermal processes declined steadily over the years, in favor of higher performance catalytic processes.
The proliferation of new catalyst compositions led to the expansion and optimization of the traditional refining processes. The developments were rapid and have led to the formation of the International Zeolite Association, in 1973. In addition, companies such as Haldor Topsøe (Denmark), UOP (USA), Institut Français du Pétrole (IFP) (France), Axens (France), Snamprogetti (Italy), Johnson Matthey (UK), Fortum Oil (Finland), Gasum Oy (Finland), Criterion (USA) affiliated with CRI Catalyst, Shell Global Solutions and Zeolyst International, Süd-Chemie (Germany) now part of Clariant (Switzerland), W. R. Grace & Company (USA), BASF (Germany), Exxon Mobil (USA), Pacific Coast Oil Company now Chevron (USA), Total (France), and many more have developed and licensed commercial technologies for various segments through the years focused on certain specific fractions.
These catalysts were designed for specific reactions – relevant to the petroleum based processes shown in Exhibit 1, and represent significant advances in the field.
Whilst the fundamental underlying chemistry works. Using traditional zeolite catalysts for upgrading biomass – an oxygen rich macromolecule is an inherently incorrect pathway, if the goal is to design a ‘optimum’ bio-refinery that utilizes all of the biomass. The development of such optimized catalysts is still in its infancy. A good example of such progress is IH2 technology developed by the Gas Technology Institute (GTI) of Des Plaines, IL.
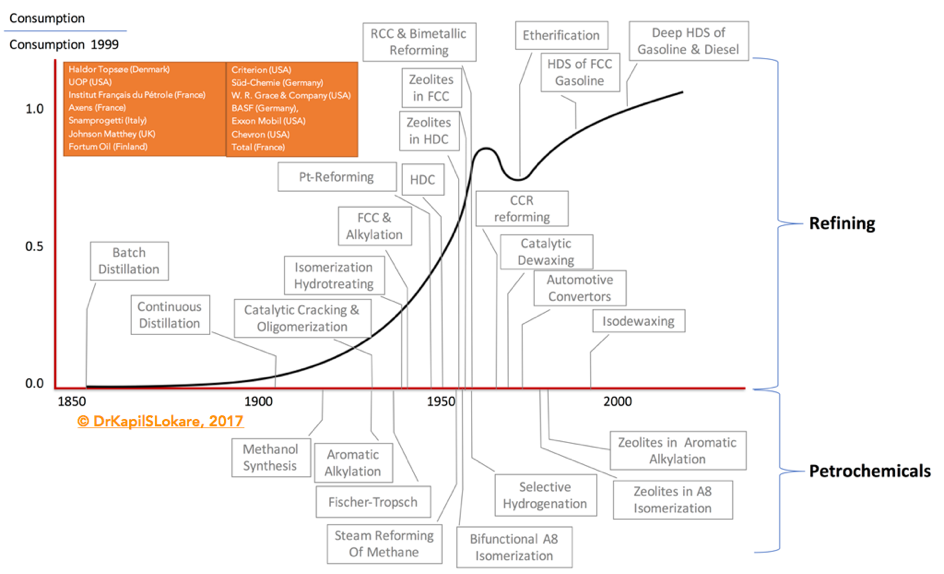
(CCR – Continuous Catalyst Regeneration; FCC – Fluid Catalytic Cracking; HDC – Hydrocracking; HDS – Hydrosulfurization; RCC – Residue Catalytic Cracking)
Now, let’s take a closer look at the T/P parameters for petroleum and bio-based processes. Exhibit 2, shows a qualitative diagram of the regimes of temperature and pressure at which petroleum and bio-based feedstocks are typically processed. Petroleum processes are usually conducted at elevated temperatures, and many of these processes are carried out in the vapor phase. Thermochemical processing of biomass-derived feedstocks, such as gasification, liquefaction, pyrolysis, and supercritical treatments involves high-temperature treatment of biomass. Bio-based feedstocks are usually treated at mild temperatures, and most of these processes are carried out in the liquid phase. Reactions such as hydrolysis, dehydration, isomerization, oxidation, aldol condensation, and hydrogenation are often carried out at temperatures near or below 400 K. Hydrogenolysis, and hydrogenation reactions are usually carried out at higher temperatures (470 K), and aqueous-phase reforming is carried out at slightly higher temperatures (500 K) and at higher pressures to maintain the water in the liquid state (>50 atm). Vapor phase reforming of oxygenated hydrocarbons can be carried out over a wide range of temperatures and at modest pressures (10 atm).
Given the fundamental nature of chemistry, conceptually it was obvious for many in the field given their pivotal role in crude oil refining, zeolites can potentially also play an important role in biomass conversions based on the high similarity between these two. Both conversions require the degradation and transformation of a complex feedstock towards useful components. However, based on the higher oxygen content of biomass compared to crude oil, there are also some major differences affecting the outcomes.
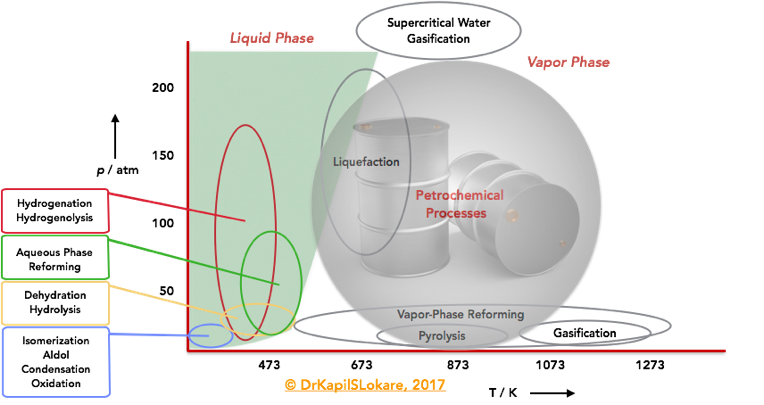
First, where crude oil refining is mostly a gas phase process, biomass conversions take mainly place in condensed phase, mostly aqueous media, which has major implications on the stability of the catalysts. Common industrial zeolite catalysts are mainly designed to withstand gas phase processes, which does not necessarily mean that they also endure in aqueous conditions. The latter becomes particularly relevant when the stability of metal particles in zeolites is considered. By further establishing the stability mechanisms of the zeolite catalysts in aqueous phase conditions, stable zeolites may be designed with simple procedures, which are essential for industrial processes.
Despite the success of acidic zeolites in biomass valorization, the exact nature of the active site in polar aqueous solutions is still vague. Due to the reactive nature of biomass derivatives, it is in some specific cases preferred to use basic sites instead of acidic ones. For example, basic catalysts have much lower deactivation tendencies and consequently higher yields in the aldol condensation of aldehydes.
Due to the low stability of some high-oxygenated components, it may be necessary to convert these products immediately to more stable ones. Therefore, strategic combinations of the active sites are essential, in which the amount and strength of the present functions must be optimally balanced. Moreover, as this balance is in some cases very thin, it is recommended that all active sites are easily accessible for the reactants. When the active sites of one of the catalytic functions are, for example, significant less accessible, the ratio between both catalytic functions is drifted away from the optimal point resulting in an excess of the other catalytic function(s) leading to unwanted side reactions or lower yields.
Bio-based refineries may only be competitive with crude oil refineries when the entire entity of the feedstock is used. In other words, it is important to develop valorization paths for every incoming stream (cellulose, hemicellulose, lignin, triglycerides, turpentine, amino acids etc.) to minimize the amount of feedstock that will end as waste or is burned off. In addition, the role of the pre-treatment is often overlooked (or avoided by using model compounds) in biomass research. Nevertheless, the use of industrial feedstocks often requires some specific changes to the used catalysts. Therefore, integrating industrial feedstocks in the designed lab-scale processes is, from an industrial point of view, at least as important as the catalytic process itself.
The catalytic applicability of zeolites in various biomass processes is, often performed in batch reaction systems. Thereby catalyst deactivation by cokes deposition is not critically addressed. Here, testing in line linked set-ups or even better in continuous mode is necessary and will give a better insight in the process design or in the feasibility to scale-up for industrial use. For example, due to the high oxygen content of biomass and the lower stability of the intermediates, severe coking may occur. Inventive reactor set-ups, where inspiration can be derived from petro-chemistry, could give a solution, Exhibit 3.
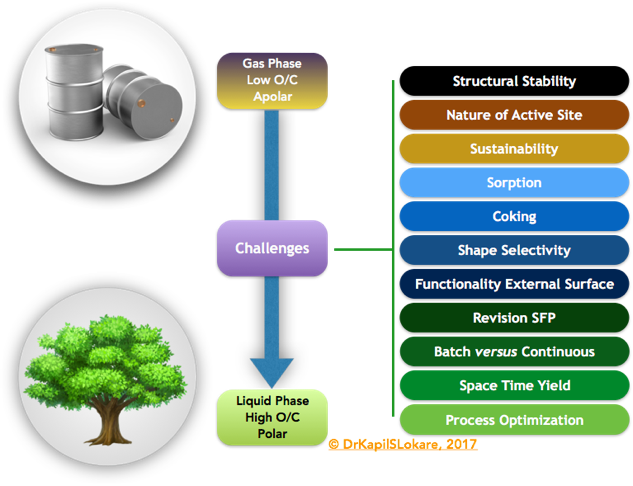
Biomass components are solid substrate due to their high oxygen content, which hampers the interaction with solid catalysts. This may lead to low space-time yields, by, for example, relatively high catalyst-substrate ratios, occasionally up to 1 or 2. Finding alternatives to increase the interaction between the catalyst and the substrate may be crucial in decreasing this ratio. To this end, it is important, instead of focusing merely on the catalytic process, to pay more attention to the engineering aspects of the processes.
Research and development of catalysts does not end when active and selective powder catalysts are developed. Besides the upscaling of the process itself, another important hurdle should be taken, namely the transformation of a research catalyst to an industrial catalyst. Such industrial catalysts contain, besides the active phase, multiple additives to provide desired physical, chemical and mechanical properties. This is exemplified by FCC catalysts, where around 10 wt% of the industrial catalyst may constitute the active phase (USY zeolite). The other 90% comprises binders, catalyst matrix, fillers and other additives. Some of these components, like silica–alumina materials, also exercise a catalytic role by pre-cracking the large oil molecules which facilitates the diffusion towards the active phase. As biomolecules are also bulky molecules, the use of an active pre-cracking matrix, whether or not preceded by a thermal/chemical pre-treatment step, may be an essential element for an industrial bio-refinery catalyst. Here, the differences between both feedstocks will lead to important alterations pertaining to FCC catalysts. There is, for example, less need to design catalysts with active components for the removal of traces of N and S, while hydrogenation of double bonds and/or deoxygenation will be largely in focus, i.e., FCC process whilst good, is probably not the be-all and end-all of biomass upgrading.
II. Disregarding Inherent Oxygen Content in Biomass
Petroleum feeds usually have a low extent of functionality (e.g., OH, CO, COOH) which makes these feeds directly suitable for use as fuels after appropriate catalytic processing. In contrast, functional groups must be added to petroleum-derived feeds to produce chemical intermediates, and the challenge lies in the ability to add these groups selectively (e.g., to add CO groups without complete oxidation of organic reactant to carbon dioxide and water. Unlike petroleum which contains limited functionality, biomass-derived macromolecules (cellulose, hemicellulose and lignin) contain excess functionality for use as fuels and chemicals, and the challenge in this field is to develop methods to control the functionality in the final product.
The “upgrading” of woody biomass essentially refers to oxygen removal and energy densification, which converts the woody biomass i.e., biomass-to-liquids (BtL) while retaining as much hydrogen as possible. Preferentially, the products generated are chemically fungible to their petroleum counter-parts, and, if necessary, are able to be processed further with existing refining technologies so that no new large investments are needed before their introduction can be realized, especially with respect to transportation fuels. Of course, the product distribution would be biomass-dependent. However, the maximum theoretical yield one may achieve is in the vicinity of 35-40% based on dry biomass. The key lies in selective deconstruction of biomass to retain the available oxygen and divert to the bio-chemicals space over bio-fuels, Exhibit 4.
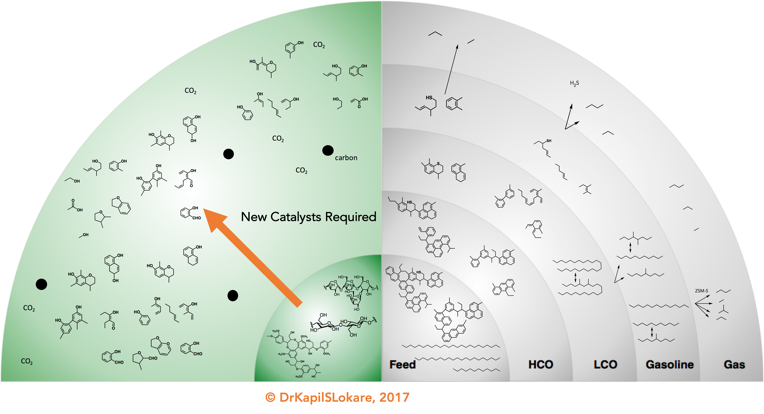
III. Diseconomies of Scale
Based on the fundamental laws of microeconomics, one may think of economies of scale, i.e., factors that cause the average cost of producing something to fall as the output volume increases. Economies of scale were the primary drivers of corporate gigantism in the 20th century and were fundamental to Henry Ford’s revolutionary assembly line, with a more recent example from Nevada, United States, the Tesla Gigafactory with battery production. This continues to be the spur to many mergers and acquisitions within the renewable industry today.
Economies of scale, however, have a dark side – diseconomies of scale, Exhibit 5. The larger an organisation becomes in order to reap economies of scale, the more complex it has to be to manage and run such scale. This complexity incurs a cost, and eventually this cost may come to outweigh the savings gained from greater scale. In other words, economies of scale cannot be gleaned forever. Some might even quote the Ringelmann Effect, discovered by French agricultural engineer Maximilien Ringelmann (1861-1931).
Ringelmann Effect: ‘Pour l’emploi de l’homme, comme d’allieurs des animaux de trait, le meilleure utilisation est réalisée quand le moteur travaille seul: dès qu’on accouple deux ou plusieurs moteurs sur la même résistance, le travail utilisé de chacun d’eux, avec la même fatigue, diminue par suite du manque de simultanéité de leurs efforts …’
Translation: ‘When employing men, or draught animals, better use is achieved when the source of motive power works alone: as soon as one couples two or several such sources to the same load, the work performed by each of them, at the same level of fatigue, decreases as a result of the lack of simultaneity of their efforts …’
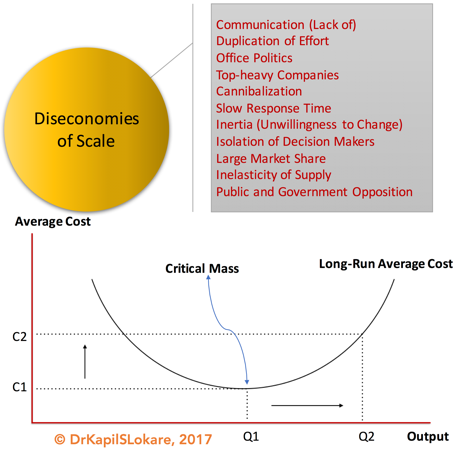
The relatively expensive error on KiOR’s part perhaps recommends a pivot and reconsider the business strategy for the bio-based industry and consider how multiple approaches can be utilized to address sustainability. On a closing note – one may summarize four take away messages:
- Engage/hire wisely,
- Don’t expand too fast in the biomass upgrading space (especially start-ups),
- FCC process whilst good, is probably not the be-all and end-all of biomass upgrading,
- Incremental disruption – try not replace a 100+ -year technology petroleum industry based in a short span.
Source
E2IG Solutions Pvt Ltd, 2017-05-02.
Supplier
Axens Technologies (IFP)
BASF SE
Chevron Corporation
Clariant International AG
Criterion Catalyst Company Ltd.
ExxonMobil
Fortum Corporation
Gas Technology Institute
Gasum Oy
Johnson Matthey
Shell Group
Süd-Chemie
Topsoe
Total
UOP
Share
Renewable Carbon News – Daily Newsletter
Subscribe to our daily email newsletter – the world's leading newsletter on renewable materials and chemicals