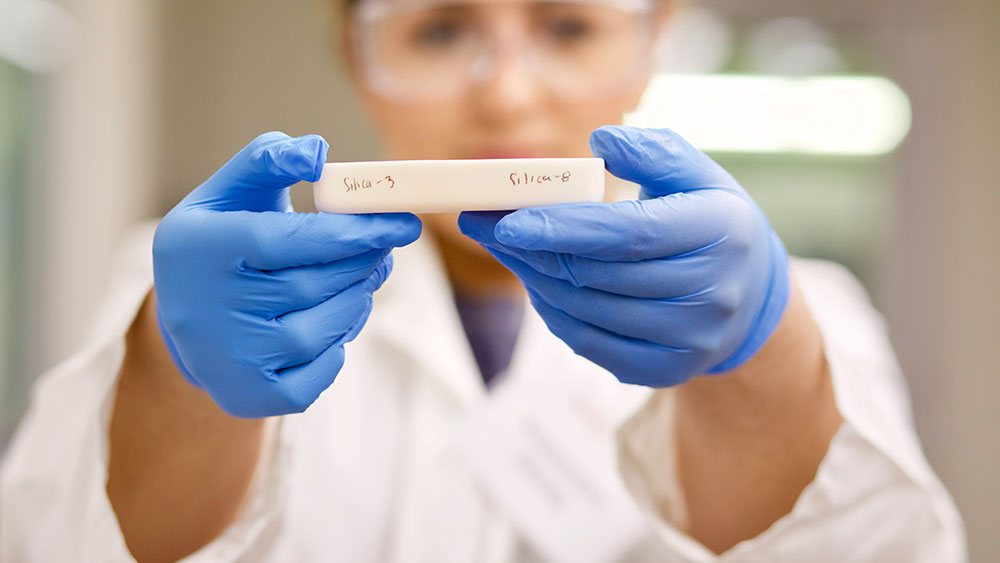
A team of researchers is using carbon dioxide and table salt to make 3D-printed polymers more environmentally friendly through a process that allows the polymers to naturally degrade over time.
Research led by Emily Pentzer, associate professor in the Department of Materials Science and Engineering and the Department of Chemistry at Texas A&M University, is a collaborative effort that includes researchers from the College of Engineering, the Texas A&M Engineering Experiment Station, the Department of Chemistry and the University of Kashmir.
The research was published in the journal Angewandte Chemie.
“Our goal was to create sustainable degradable polymeric structures,” Pentzer said. “We did this by leveraging the microstructures afforded by chemistry in conjunction with the macrostructures afforded by 3D printing.”
Most commercial synthetic polymers consist of large molecules that do not break apart under normal conditions. When left in the environment, manufactured items such as foam cups or plastic containers break down into small pieces that are unseen by the naked eye, but the long polymer molecules remain present forever.
“It’s not just the plastic bottle being kicked down the road,” Pentzer said. “These materials break down into microplastics that stay in the environment. We don’t fully understand the impact of microplastics, but they’ve been shown to carry diseases, heavy metals and fecal bacteria.”
To make the degradable polymers, Pentzer collaborated with Don Darensbourg, Distinguished Professor in the Department of Chemistry at Texas A&M, to use carbon dioxide and table salt to create the ink that was used in the 3D printing process. After printing, the structures are washed with water to dissolve the salt and solidify the structure. While the outside of the structure continues to look smooth, the process creates thousands of small pores which allow the chemical compounds to degrade at a quicker rate.
“Under the right conditions, the polymers we’ve created will actually degrade quickly,” Pentzer said. “Ideally, they’ll break apart into small molecules that are not toxic. These smaller molecules won’t be able to carry things like heavy metals or bacteria.”
More at the College of Engineering
Source
Texas A&M University, press release, 2022-11-04.
Supplier
Share
Renewable Carbon News – Daily Newsletter
Subscribe to our daily email newsletter – the world's leading newsletter on renewable materials and chemicals