Introduction
Industrial food processing residues and wastes arise during food and beverage manufacturing, processing and handling. Such materials can be produced in significant quantities by major businesses, such as bakeries, breweries, meat and dairy processing facilities, distilleries and sugar refineries.
Industrial food processing residues and wastes are an unavoidable output from such activities given stringent quality standards and regulations surrounding food production. Where materials are contaminated, spoilt or of low nutritional value, there would be restrictions on or limited interest in them entering the food or feed supply chain – in such cases, these materials would be classified as wastes in line with the Waste Framework Directive, defined as “any substance or object that the holder discards or intends or is required to discard”.
Conversely, where the residual output from the main activity is suitable for consumption or has an alternative market, it would be considered a processing residue, defined as “a substance that is not the end product(s) that a production process directly seeks to produce. It is not the primary aim of the production process, and the process has not been deliberately modified to produce it.” Although nuanced, these definitions are important when it comes to targeting the most suitable use or disposal route for these materials.
Over the past couple of years, NNFCC has undertaken several projects looking at biomass feedstock availability in the UK, with a particular focus on industrial food processing residues and wastes in many cases. Interest in that specific feedstock stream has been revived by existing (and mounting) competition for household and commercial food waste. As such, many bioeconomy stakeholders are looking to diversify and tap into new streams, with industrial wastes now being put under the spotlight, especially within the bioenergy sector.
The value of industrial food processing residues and wastes lies in the purity of each individual waste stream. Being produced from the manufacturing or processing of a specific food or drink, the residues and wastes are less likely to contain contaminants and will not contain any packaging (an issue faced with the processing of household and commercial food waste). As a result, the composition of each waste stream is known to a good degree of accuracy and is typically consistent in both quality and output volume, making subsequent processes more likely to be efficient and successful.
Here, we look at the value of these feedstock streams for the production of biobased products and biofuels via fermentation, and for the production of bioenergy through anaerobic digestion (AD).
Biobased products and biofuels
Industrial fermentation is characterised by the industrial production and processing of chemicals, materials and energy using bacteria, fungi, and yeast1. The applications of this technology seem practically endless and span a very wide range of sectors, from food through chemicals to biofuels. From January 2019 to the summer of 2023, NNFCC participated in the EU-funded ShikiFactory 100 project, the aim of which was to assess the industrial and commercial potential of more than 100 specialty chemicals produced using synthetic biology. Partners developed modified strains of yeasts and bacteria designed to increase the yield potential of those 100+ compounds under fermentationconditions. The molecules studied during the course of the project had theoretical and practical applications in cosmetics, pharmaceuticals and food sciences – most compounds having applications in more than one of these sectors.
Nowadays, the biggest industrial use for fermentation is for the production of bioethanol, with around 100 billion litres produced globally every year2, showing that fermentation has the ability to reach industrial scales. The “true” sustainability of bioethanol in such a context often comes to the fore as most of the global feedstock mix is composed of sugar- and starch-rich, sugarcane, corn, wheat and barley. Establishing reliable industrial supply chains for sugar- and starch-rich waste streams from the food sector could help alleviate some significant challenges.
Industrial food processing residues and waste streams such as bakery and sugar waste offer high quality
organic feedstocks. In addition, as the food and drink industries are at no risk of becoming redundant
– quite the opposite as the food sector continues to grow every year to meet a growing population – the production of high quality outputs will continue to increase. As such, should reliable supply chains be put in place to provide quality feedstocks to the industrial fermentation sector, it could help valorise ubiquitous and ever-growing waste and residue streams from the food industry, support the scaling-up of industrial fermentation globally, and reduce the use of food crops for the production of goods other than food. However, this is likely to create an interesting conundrum for the industry.
Today’s large capacity bioethanol plants were built based on the availability of arable crops, which are already
produced on mass and are often associated with easy transportation (such as cereal grains for example). Food waste-based plants are often smaller scale, while the feedstock streams require more complex transportation strategies (as the materials is often wet and hard to handle) and consistency can vary.
In Scotland, Celtic Renewables has developed a process that uses whisky distillery by-products such as pot ale and draff to produce bioacetone, biobutanol and bioethanol. Usually exclusively produced from petrochemicals, these three chemicals are found widely in our everyday lives, from cleaning products, to medicines and phone casings. Their market is expected to grow to £130 billion by 2030 (from £87 billion currently), showing the breadth of opportunity. Launched in 2012, the company presented its first large scale butanol sample in 2015 (showing a 1,000 fold increase in production), alongside being named the most innovative SME in Europe. In 2020, Celtic Renewables received funding for theconstruction of the company’s first commercial production plant, which is located in Scotland. Since the start of this endeavour, Celtic Renewables has been sourcing feedstock from local Scottish distilleries, showing their ability to adapt their process to local communities, and to valorise local production, while developing a robust commercial-scale supply of quality biobased chemicals.
Bioenergy
Under the Green Gas Support Scheme (GGSS), the main support mechanism for the AD industry at present, feedstock restrictions stipulate that at least 50% of the biomethane output must be derived from wastes and residues. In addition, the Scheme applies strict sustainability criteria to feedstocks where land use and supply chain emissions are taken into account. As such, although crops remain the most productive feedstock stream in terms of biogas yields, AD sites must consider a feedstock mix that includes a significant amount of wastes or residual materials.
As a result, industrial food processing residues and wastes can be a valuable feedstock stream for the AD sector. Being almost exclusively produced as a single stream, the quality of the waste is known and consistent, which allows for more predictable, reliable and efficient energy production further down the line. This makes it a more valuable feedstock stream than household and commercial food waste, for which composition and quality varies widely, and contamination risk is high.
Figure 1 illustrates the typical variation in biogas yields and indicative costs of a range of feedstock types, by classification. Industrial food processing residues and wastes rank second, with yields typically ranging between 70 to 120 cubic metres of biogas per tonne, and on some of the lower yielding materials gate fees are still available, offering an additional financial incentive to AD operators.
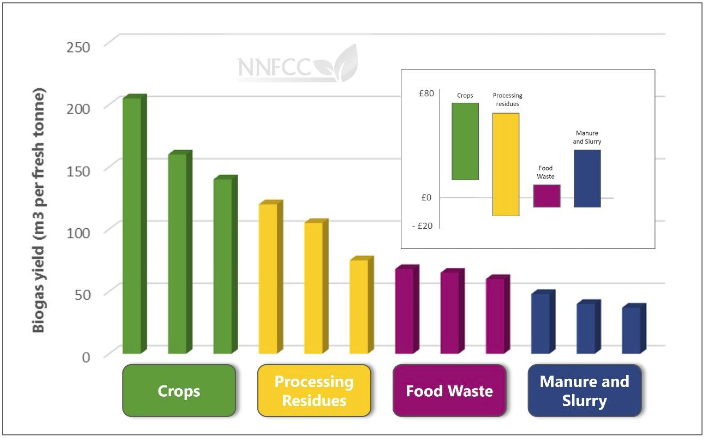
Although certain industrial waste or residue streams might be reserved for chemicals and biofuels production where demand exists (e.g. bakery waste, distillery waste), other categories such as brewery waste and animal processing waste (i.e. abattoir waste, fisheries waste) could be valorised by AD. AD also offers an opportunity for on-site processing of such materials; by siting an AD alongside the food manufacturing or processing facility, the wastes and residues can be digested, extracting biogas for conversion to heat, power and/or biomethane for use within the process. This offers significant opportunity for carbon reduction at site- and product- level, offering the producer an environmental and potentially also a commercial advantage over their competitors. Such activity is viewed favourably for corporate social responsibility (CSR) and environmental, social and governance (ESG) purposes.
The Waste Hierarchy guides how waste is used, giving priority to re-use, then recycling, recovery and last of all disposal. AD would be classified as recycling where quality digestate is produced, putting this as a favourable use to incineration through an energy from waste (EfW) facility; however, it should be noted that re-use of materials arising during the production of food and feed should be prioritised over AD, where the material is still fit for consumption and market demand exists.
Industrial food residues and waste in the UK
WRAP estimates that the UK produces around 1.7 million tonnes of industrial food processing residues
and wastes annually, occupying a 16% share of the total 9.5 million tonnes of food waste arisings (tonnages expressed as fresh weights). Through the course of NNFCC’s recent project work, regional maps of arisings in the three nations of Great Britain have been produced. Regional data was used to estimate waste arisings3 from food and drink manufacturers (see Figure 2).
Regions coloured in green showed the highest production potential for industrial food processing residues and wastes. The yellow, orange and red areas showed lower quantities comparatively, with red indicating the regions with the lowest arisings in the country.
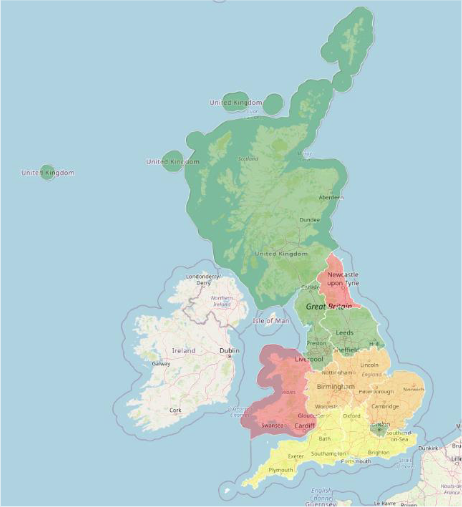
Although mapping arisings provides useful insights into the geographical distribution of feedstocks, it does not take into account current use, and therefore, may provide a skewed assessment of true availability. Figure 3 below shows regional availabilities4, calculated by subtracting current AD treatment capacity for the target waste streams from total arisings. Here, for example, we see that although Scotland is projected to be producing high amounts of potential feedstocks from food and beverage manufacture, a lot of AD capacity for such materials already exists, therefore, availability is considered low. On the contrary, although the North East is one of the areas with the lowest projected arisings, data shows that the region retains a high surplus after all operational AD capacity has been considered.
Further assumptions must be made, as we cannot expect such feedstocks to remain within the confines
of the region it was produced in. Thus, cross-border trade must also be taken into consideration when
assessing availability.
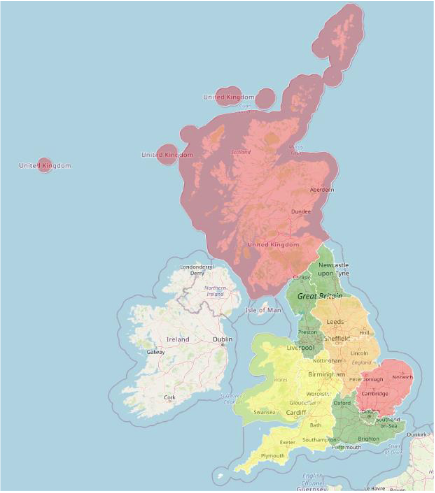
Conclusions
Industrial food processing residues and wastes are a valuable part of the bioeconomy revolution. The feedstock stream combines four key qualities: energy-rich materials; a continuous and ever-growing production capacity; little to no land use change; and reduced GHG emissions compared to the planting,
harvesting and transport of crop feedstocks.
Although exploiting industrial wastes on a commercial scale does come with its own set of challenges (i.e. availability and difficult transport logistics), setting up supply chains could benefit local communities and valorise local independent food and drink production, ultimately answering a key (and often
neglected) aspect of sustainability ideals.
1IDTechEx. 2023. White Biotechnology: Key Technology Trends Reshaping Its Growth.
2Busic et al. 2018. Bioethanol Production from Renewable Raw Materials and Its Separation and Purification: A Review. Food Technology and Biotechnology 56.
3Maximum production capacity.
4 Quantities leftover once competing uses have been accounted for.
Author
Théa Allary
Source
NNFCC, press release, 2024-02-14.
Supplier
Share
Renewable Carbon News – Daily Newsletter
Subscribe to our daily email newsletter – the world's leading newsletter on renewable materials and chemicals