To convert food scraps and other biological waste back into usable materials, the Fraunhofer Institute for Ceramic Technologies and Systems IKTS, together with industry and research partners, built a facility in Thallwitz near Leipzig that is unique worldwide. It produces synthetic fuels and biogenic waxes from biogas – not only from the contained CO2. The biogas is obtained from old fats used in catering and food production. If required, a ceramic electrolyzer can be connected, which also provides the required substances for the process using electricity from renewable energies. IKTS now intends to further develop the innovative plant concept for industrial-scale production in cooperation with a Leipzig-based company.
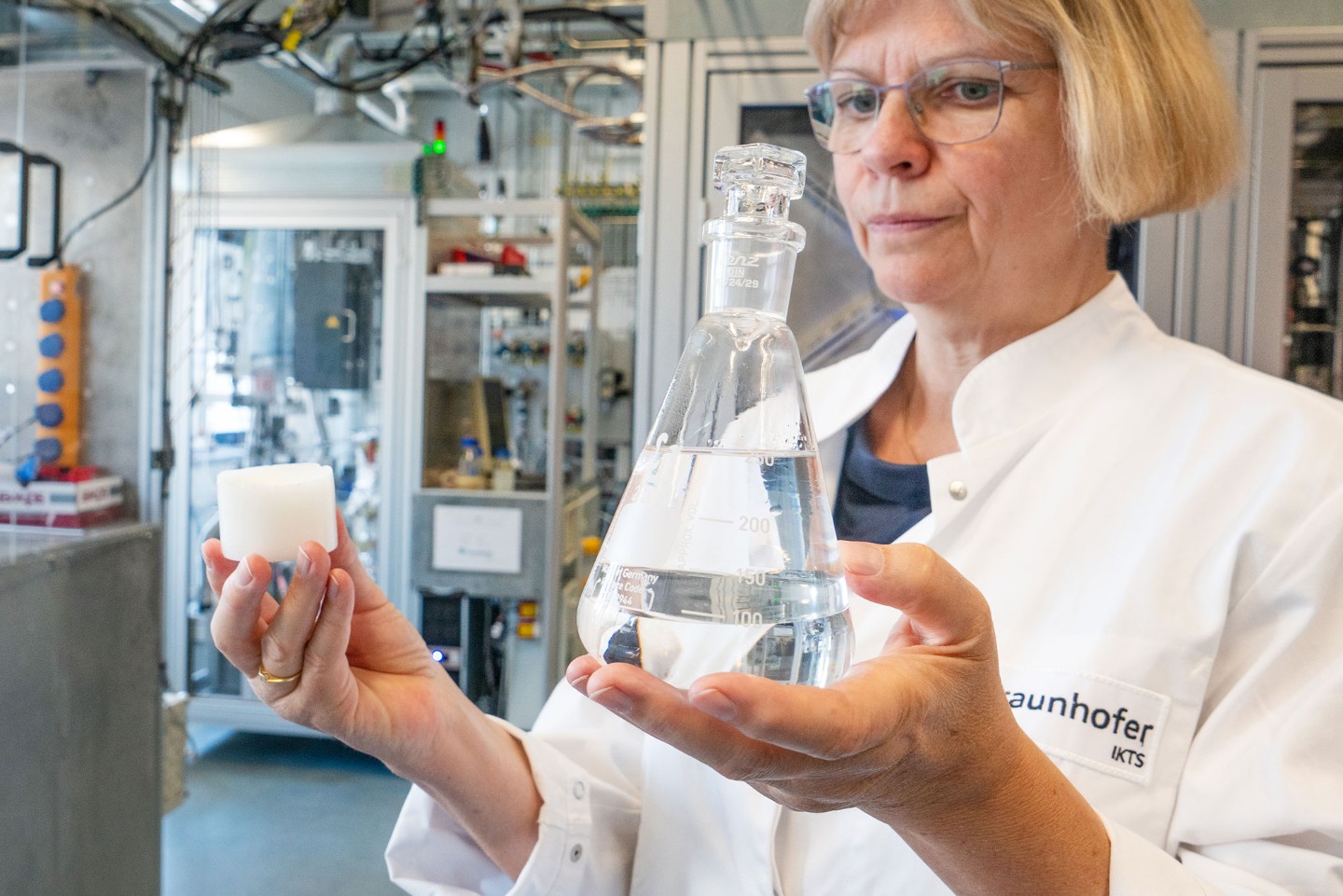
In view of more than 9000 biogas plants in operation in Germany, Dr. Erik Reichelt, head of the IKTS working group Process Systems Engineering, sees considerable market potential: “Such expanded biogas plants open up considerable opportunities to build up new value creation and jobs in the central German mining area already now for the period after the coal phase-out.” In Saxony alone, around 270 biogas plants are currently in operation – and the new system is an interesting option, especially for the larger ones. It could help to operate the plants more economically and to react better to market fluctuations. In addition, the circular economy concept helps to conserve natural resources, reduce the use of fossil natural gas and oil, and protect the environment.
The objective of the project in 2017 had been much more modest. Originally, the development consortium wanted to make the biogas plants “only” more resilient to market fluctuations and feed-in tariffs by additionally upgrading them for wax production. The idea: if it is not worthwhile to convert the biogas into electricity due to unfavorable prices, the operators can switch flexibly to the production of biogenic waxes with some additional technology. This can then be sold to the cosmetics and lubricants industry. However, during the development process, the concept has expanded to include additional technology pathways that also incorporate network serviceability.
Reformer, Fischer-Tropsch reactor and electrolyzer combined
To test these approaches in practice and build a pilot plant, the research institutes Fraunhofer IKTS, TU Bergakademie Freiberg and the TU Dresden, and the Saxon companies Ökotec-Anlagenbau GmbH, Sunfire GmbH and DBI Gas- und Umwelttechnik GmbH, have joined forces to form a development alliance. Ökotec-Anlagenbau made its existing biogas plant available. There, the partners additionally installed a reformer, a Fischer-Tropsch reactor and an electrolyzer. In the first step, the expanded plant feeds biogas and water vapor into the reformer, which produces synthesis gas from it – a mixture of hydrogen and carbon monoxide. The Fischer-Tropsch unit then converts this synthesis gas into methane, liquid hydrocarbons, and wax. The methane is fed right back into the process to heat the plant park. What remains is the wax and the liquid products in the ratio 50 to 50. The latter can then be further processed in refineries into synthetic diesel or kerosene.
As an alternative and additional source for the synthesis gas, a container is docked with the mentioned electrolyzer. This is switched on when there is little biogas available or when there is a particularly high supply of electricity due to peaks in supply from solar or wind power plants. This electrolyzer breaks down water vapor and carbon dioxide into hydrogen and carbon monoxide, i.e. synthesis gas again. It also ensures the continuous supply of the Fischer-Tropsch synthesis plant, which only works efficiently when there is always enough synthesis gas available.
Producing green power or petroleum-free fuels or waxes, depending on market conditions
A biogas plant equipped in this way therefore has several options for responding to market fluctuations: the operator can continue to convert the biogas into electricity, for example using a gas engine and generator, when electricity purchase prices are high. If feed-in tariffs are low, he switches to the production of biogenic wax and synthetic fuels. And if a lot of electricity from renewable sources is available, he switches the electrolyzer on.
The petroleum-free fuels and waxes obtained are still more expensive than corresponding fossil-based products. For example, the synthetic fuels and waxes have a production cost of around € 2.50 per kilogram. However, the current energy price crisis has already greatly reduced the once immense cost differences to petroleum-based products. And even if we assume that prices on the oil and gas exchanges will drop again: the need for sustainably produced energy sources and materials is growing in many industrial sectors. The airlines in particular are under pressure here due to more restrictive environmental protection laws. The German government has announced plans to introduce significant blending of electrically generated kerosene (e-kerosene) with conventional aviation fuel as a mandatory quota from 2026 onwards.
Further demand could also come from other sectors in the future, for example from paint and coatings manufacturers, who could use the biowax obtained for the production of additives. There will also be sufficient customers in the cosmetics and lubricants industries, says Erik Reichelt. In this respect, biogas plant operators who quickly equip their operations with the new technology can be the first to meet this market demand for biogenic waxes. And if this submarket becomes oversaturated, the wax can also be liquefied into fuel through additional plant technology.
Industrial scale transfer planned
The agenda now includes the step from pilot plant to larger industrial scale. For this transfer phase, Fraunhofer IKTS is currently seeking funds from the structural change support program for the coal-mining area. In the next phase of the project, a plant is to be designed that can produce several hundred liters of synthesis products per hour.
Source
Fraunhofer IKTS, press release, 2022-07-28.
Supplier
DBI-Gastechnologisches Institut gGmbH Freiberg
Fraunhofer-Institut für Keramische Technologien und Systeme (IKTS)
Ökotec Anlagenbau GmbH
Sunfire GmbH
Technische Universität Bergakademie Freiberg
TU Dresden
Share
Renewable Carbon News – Daily Newsletter
Subscribe to our daily email newsletter – the world's leading newsletter on renewable materials and chemicals