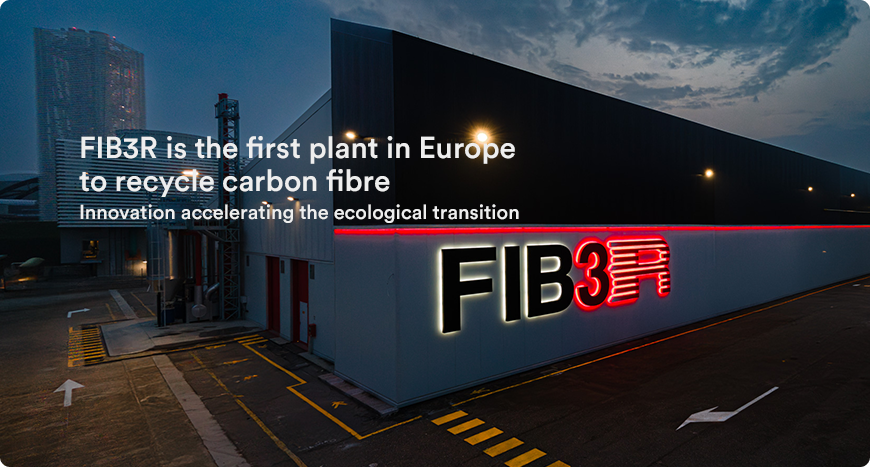
The Hera Group is moving swiftly towards the circular economy of the future and has inaugurated, in Imola (Bologna), at the heart of the country’s Motor Valley, the first plant of its kind in Europe, capable of regenerating carbon fibre on an industrial scale. It is called FIB3R, a name that reflects the 3 R’s that stand at the basis of the project: recover, reduce, reuse. Carbon fibre is thus recovered and reused, reducing the use of virgin fibre and therefore the environmental impact that would be required to produce it.
There is one important competitive advantage: the fibre regenerated from FIB3R retains the virgin fibre’s characteristic lightness and high strength, guaranteeing – through a state-of-the-art pyrogasification process – that the regenerated product is ready to be reused, rewoven and/or impregnated, for the high-performance purposes for which this type of material is intended. The number of industrial sectors interested in these outstanding features is increasing, ranging from automotive to aerospace, nautical, furniture, textiles and fashion in the broadest sense, only to give a few examples.
The Hera Group’s commitment to advancing the ecological transition, as well as the expected increase in demand for carbon fibre over the next few years, have led it to anticipate this megatrend, accepting the challenge of applying it to this material as well, on an industrial scale. This will reinforce the virtuous path towards the circular economy that has been the basis of its strategy for years, combining economic growth with environmental sustainability. This path is the right one, as confirmed by the interest of the European Union, which has allocated FIB3R financing coming to more than 2.2 million euro as part of NextGenerationEU for its innovative technology and the strategic importance of the materials processed. The total investment planned by the Hera Group to build the Imola plant amounts to 8 million euro.
At present, the plant is expected to produce 160 tonnes of recycled carbon fibre each year, with energy savings coming to 75% compared to virgin fibre.
“FIB3R is the first plant of its kind in Europe able to recycle carbon fibre. It is aimed at promoting short and circular supply chains, in line with the strategy of making our served areas more competitive and resilient,” states Orazio Iacono, CEO of the Hera Group. “FIB3R is also a concrete example of how the Hera Group is able to combine technological innovation and sustainability, by exploiting the cross fertilisation between the advanced skills of the Group’s various sectors. Recovering carbon fibre not only reduces the environmental impact of this waste, but also creates new market opportunities in strategic industrial sectors. Investing in this kind of circular infrastructure increases the resilience of production chains, reduces dependence on imports of critical raw materials and, at the same time, creates value through sustainable business models. With over 100 advanced plants and 5 new facilities under construction, we have consolidated our country’s largest and most modern set of plants for material treatment and recovery, strengthening our role as a reference operator in the sector and a driving force for the circular economy in Italy. Our Business Plan confirms this strategy, with 2 billion euro in investments for 2024-2028 destined for regenerating resources, a commitment intended to generate value for all our stakeholders.”
This morning’s inauguration of the FIB3R plant within the Group’s main facility in Imola, near Bologna, offered a chance to engage in a debate on the future of carbon fibre, combining innovation and sustainability. After the institutional welcome given by Marco Panieri, Mayor of Imola, and Irene Priolo, Councillor for the Environment, Local Planning, Mobility and Transport and Infrastructures of the Emilia-Romagna Region, Herambiente CEO Andrea Ramonda opened the event.
This event saw the participation of important representatives of the industrial and academic communities: Davide Abate, Ferrari’s Chief Technologies and Infrastructures Officer; Roberto Frassine, Chairman of Assocompositi; Loris Giorgini, Director of the Department of Industrial Chemistry at the University of Bologna; Raffaella Luglini, Chief Sustainability Officer Leonardo; Horacio Pagani, Founder of Pagani Automobili; Andrea Rangone, Full Professor of Entrepreneurship and Digital Business Innovation at the Milan Politecnico; Ferruccio Resta, Chairman of the Fondazione Bruno Kessler FBK. The meeting came to a conclusion with a contribution by Orazio Iacono, CEO of the Hera Group.
Before FIB3R
The Imola plant was developed by Group subsidiary Herambiente, Italy’s leading waste recovery and treatment operator, which had been experimenting with the carbon fibre recovery process for some time. This involved a collaboration with the Department of Industrial Chemistry of the University of Bologna and its technological partner Curti Costruzioni Meccaniche, a Ravenna-based company and leader in the production of automatic machines for industrial applications, which offered its knowledge and pilot plant to model the formula being studied. After three years of tests, the Hera Group, based on its expertise in engineering and waste treatment, industrially developed the project and built the FIB3R plant, to recycle composite materials and help bridge the gap between supply and demand of virgin fibre, reducing its environmental impact.
Data sheet
How carbon fibre is reborn
In the Imola plant, the rebirth of carbon fibre happens inside a 60-metre tunnel where an innovative and advanced pyrogasification process takes place. In the first phase, pyrolysis, the carbon fibre, which is more resistant to heat, is released from the resin, and in the second phase, gasification guarantees a regenerated fibre of the highest quality, pure, shiny and entirely sustainable as regards the environment. The resin decomposed in a gaseous form is reused to generate part of the energy required for the process, maximising energy recovery. The dust remaining in the fibres is vacuumed and sent to the abatement system. The result, after treatment, is the finest high-purity carbon fibre, with all its mechanical properties intact and ready to be rewoven and impregnated for all the typical uses of virgin fibre.
Energy savings and closing the circle
The recycling is potentially infinite and energy savings are very high compared to the production of virgin fibre, which is extremely energy intensive due to the high temperatures used. Furthermore, producing virgin carbon fibre requires the use of fossil raw materials and an increased reliance on landfills, since waste from fibre processing is almost exclusively destined for disposal. Life cycle analysis shows that energy demand for producing recycled fibre is 75% lower and avoids 74% of greenhouse gas emissions, significantly reducing disposals in landfills. And that’s not all: the unique nature of FIB3R also depends on the total traceability of the processed material. The used carbon fibre, in fact, enters the plant inside containers equipped with a QR code, which contains their identity card: technical characteristics, weight and origin. Once the process is complete, the same traced material returns to its owner in the form of regenerated carbon fibre, closing the circle and ensuring maximum sustainability, transparency and quality.
FIB3R’s travelling companions
To be effective, the closed cycle that distinguishes the innovative Imola plant needs partnerships between Hera Group and companies in the complex carbon chain, given that this material is increasingly present in hi-tech production sectors and, consequently, in waste management cycles. The Leonardo Group has already taken up the challenge of applying the circular economy to its production processes and, in this specific case, through its Aerostructures Division, it has launched an industrial synergy with the Hera Group by supporting a project within the Imola plant to recover carbon fibres used to reinforce the polymer matrix composites used to construct aircraft parts. Therefore, thanks to Herambiente’s assets and the know-how developed in the Leonardo Group’s laboratories, this precious material will be recycled with positive consequences in terms of sustainability and circularity. More specifically, Leonardo’s Aerostructures Division will confer to Herambiente part of the waste fibres deriving from the construction of the components of some of the best-known civil aircraft in the commercial aviation sector, such as the stabiliser of the ATR turboprop, the fuselage and horizontal stabiliser of the Boeing 787, and the tail pieces of the Airbus A220.
Discover the page dedicated to Fib3r.
Source
Herambiente, press release, 2025-03-11.
Supplier
Assocompositi
FBK Fondazione Bruno Kessler
Ferrari
FIB3R (Hera Group)
Hera Group
Leonardo Group
Pagani Automobili
Politecnico di Milano (POLIMI)
University of Bologna
Share
Renewable Carbon News – Daily Newsletter
Subscribe to our daily email newsletter – the world's leading newsletter on renewable materials and chemicals