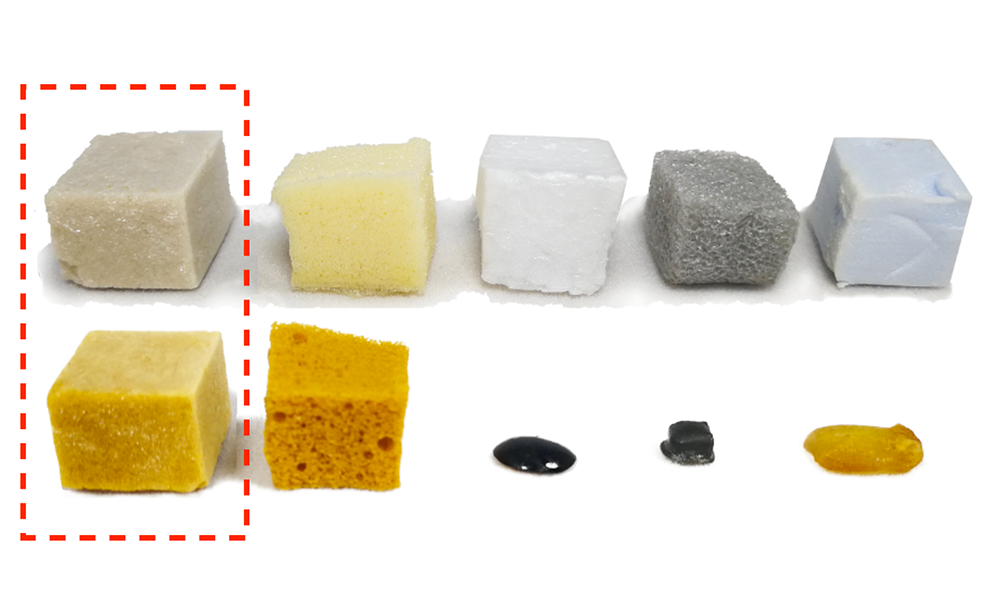
A new high-performance plastic foam developed from whey proteins can withstand extreme heat better than many common thermoplastics made from petroleum. A research team at KTH Royal Institute of Technology reports that the material, which may be used for example in catalysts for cars, fuel filters or packaging foam, actually improves its mechanical performance after days of exposure to high temperatures.
Reporting in Advanced Sustainable Systems, researchers from KTH Royal Institute of Technology in Stockholm say the research opens the door to using protein-based foam materials in potentially tough environments, such as filtration, thermal insulation and fluid absorption.
The basic building blocks of the material are protein nanofibrils, or PNFs, which are self-assembled from hydrolyzed whey proteins—a product from cheese-processing—under specific temperature and pH conditions.
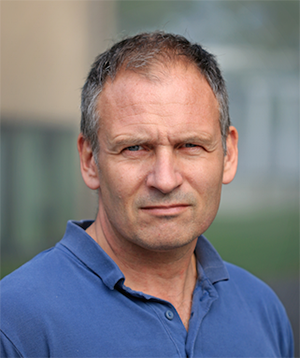
In tests the foams improved with aging. After one month of exposure to a temperature of 150C, the material became stiffer, tougher and stronger, says the study’s co-author, Mikael Hedenqvist, professor in the Division of Polymeric Materials at KTH.
“This material only gets stronger with time,” he says. “If we compare with petroleum-based, commercial foam materials made of polyethylene and polystyrene, they melt instantly and decompose under the same harsh conditions.”
Proteins are often water-soluble, which poses a challenge when developing protein-based materials. Despite this, the material proved water-resistant after the aging process, which polymerized the protein, creating new covalent bonds that stabilized the foams. The foam also resisted even more aggressive substances—such as surfactants and reducing agents —that normally decompose or dissolve proteins. The crosslinking also made the foam unaffected by diesel fuel or hot oil.
The material also showed better fire resistance than commonly used polyurethane thermoset.
“This biodegradable, sustainable material can be a viable option for use in aggressive environments where fire resistance is important,” Hedenqvist says.
Potential applications include providing support for catalytic metals that operate at higher temperatures, such as platinum catalysts for automobiles. The material could conceivably work as a fuel filter, too.
Other possibilities are to use it as packaging foam and in applications for sound and thermal insulation where higher temperatures may occur and where there is a risk of an aggressive environment.
Working with Hedenqvist on the research was lead author Xinchen Ye and co-authors Antonio J. Capezza, Vasantha Gowda, Richard T. Olsson and Christofer Lendel. Funding was provided by the China Scholarship Council, Vinnova, the Bo Rydins Stiftelse (F30/19), and Formas (2017-00396).
Reference
“High-Temperature and Chemically Resistant Foams from Sustainable Nanostructured Protein,” Advanced Sustainable Systems, DOI: 10.1002/adsu.202100063
Author
Peter Ardell/David Callahan
Source
KTH, press release, 2021-06-10.
Supplier
KTH Royal Institute of Technology
Share
Renewable Carbon News – Daily Newsletter
Subscribe to our daily email newsletter – the world's leading newsletter on renewable materials and chemicals