After JEC World 2020 was cancelled due to the pandemic and held purely digitally last year, the world’s leading International Composites Show will be held again this year in Paris-Villepinte from May 3 to 5. The FRIMO Group will present itself again this year as a tool and equipment supplier for complete solutions in the field of composite applications.
FRIMO is also the right contact for companies that want to think outside the box and implement innovative, sustainable product ideas. Some examples of such projects are certainly among FRIMO’s trade show highlights this year.
Innovative upholstery material
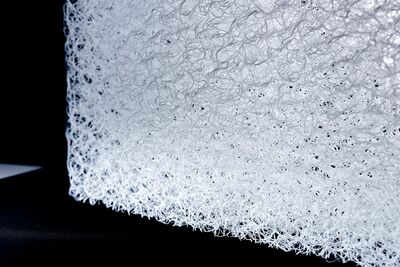
With the aim of giving this environmentally friendly product more complex geometries for applications such as automotive seat posts or in the furniture industry, FRIMO has developed an innovative processing method in collaboration with PHP Fibers. In this process, the primary material, which is cut into a cube shape, is inserted into a mold and shaped to the exact contour by a sophisticated heating, forming, and cooling process, while optimally maintaining the elastic yet sufficiently rigid loop structure. “It is a real challenge to heat this material evenly and to form and cool it down again quickly,” says Thomas Joachim, Director of Sales of the FRIMO Center of Competence Form & Punch. In addition, the integration of further functions, such as molded-on or pressed-on holders for seat covers, etc., in conjunction with corresponding textiles, allows the production of single-material systems. These thermoplastic single-material systems are comparatively easy to recycle, entirely in line with circular economy efforts.
An innovative 3D structure made of elastic continuous polyester filaments is one alternative for seat cushion production. The recyclable BREATHAIR® product from PHP Fibers is highly water repellent, antibacterial and exceptionally permeable to air and moisture. Breathair is already used, for example, in geometrically simple mattresses but also in seat cushions for the Japanese high-speed train Shinkansen.
Pallets from coconut fiber
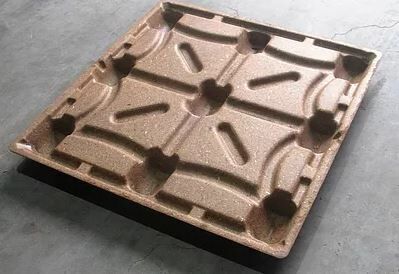
Southeast Asia has the highest demand for one-way export pallets. Due to the scarcity of wood, it must be imported, although it only ends up being used for a few weeks until subsequent disposal. In Asia alone, around 170 million trees are cut down every year for conventional disposable pallets. Last but not least, wood is one of the raw materials currently affected by supply and price problems. Forests do not grow in a year, and these shortages cannot be fixed anytime soon. This wood is better off being used for long-term purposes such as furniture and construction.
The Dutch startup CocoPallet offers a sustainable alternative with novel disposable pallets made from coconut waste. In a processing method specially developed by FRIMO for CocoPallet, the powdered and fibrous waste from coconut husk is compressed under pressure and heat to form sturdy pallets. In the process, the coconut fibers are bonded only with the naturally contained lignin in such a way that no additional substances need to be added. FRIMO has been supporting the startup company for several years. Now, together with CocoPallet, a special filling and dosing system and a prototype tool to produce these innovative stackable pallets have been developed. In addition, the pallets are recyclable but also biodegradable. Building on the success of the pallets, CocoPallet is already planning to use the process for other applications.
Wet compression molding
To produce fiber-reinforced structural components in automobiles, FRIMO offers fully automated systems for wet compression molding of monolithic and sandwich components. In this process, dry continuous fiber layups or fabrics are impregnated with a reactive resin outside the press, then brought into the press and consolidated there, where the matrix materials cure.
The lower process pressures compared to RTM make it possible to combine the fiber composite structures in the pressing process with sandwich cores, for example made of foamed polyurethane or polyethylene cores, or paper honeycombs in a single step. In addition, more cost-effective tools can be used and cycle times can be significantly reduced. Another advantage WCM has over RTM is the elimination of three-dimensional preforming of the fiber structures in advance.
Joint project “LightMat Battery Housing”
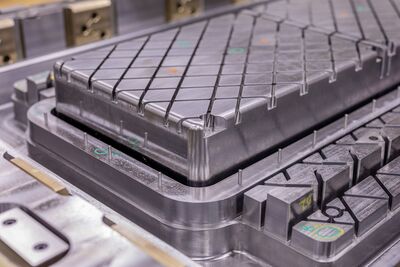
The trend towards electric cars leads to a strong focus on the whole battery package. The aim of the joint project LightMat Battery Housing (EFRE-0801511) is to develop functionalized, unidirectional fiber-reinforced semi-finished products for high volume production of highly stressed lightweight plastic battery housings. For the battery housing, this translates to a significant weight reduction compared to today’s e-vehicles with maximum functional integration in terms of stiffness, strength, EMC shielding, fire protection and process flow. FRIMO is contributing with its expertise in developing special tooling and process technology for UD and D-LFT Tapes.
UD-tapes are continuous fiber-reinforced thermoplastics that offer the most mechanical properties in fiber direction. Direct long fiber thermoplastics (D-LFT), however, provide more design freedom because of their good flow behavior. When both are combined and metal inserts are added, a new degree of freedom is reached and the lightweight potential for hybrid structures can be better utilized. Combining different materials creates special requirements for tooling. FRIMO has developed a special tool concept for this. In this concept, the pre-heated, compressed UD tapes (tailored blanks) along with the D-LFT strands are placed in the tool cavity and compressed with precision-controlled advancing pins. The advancing pins in the FRIMO Tape-D-LFT tool drape the “tailored blanks” and form the rib structure cavity to be locally overflowed with D-LFT. The additional tool closing movement presses the D-LFT into the ribs. The FRP/metal mixture makes weight savings of up to 25% possible compared to a steel construction, with a cycle time of less than a minute. This doesn’t just turn into weight savings, but also time and money savings.
Complete value chain
In addition to the highlights mentioned above, FRIMO will present its expertise and experience in thermoforming, milling, punching, and joining of composites, as well as in the automation and interlinking of processes and equipment at JEC World 2022.
FRIMO offers more than just tools, machines, and equipment in a technology portfolio that is unique on the market. Customers also benefit from the comprehensive consulting expertise of a technology company that is the market leader in many fields. This ranges from initial consultations and pre-engineering to completely customized concepts. Companies that think sustainably and want to participate in implementing a Circular Economy will find competent, creative contacts at FRIMO.
Supported by global sales and project management, FRIMO continues to stand for One Stop. All Services along the entire value chain.
About FRIMO
For more than five decades, FRIMO has bundled a unique technology spectrum that makes the Group the leading full-line supplier of manufacturing systems for the production of high-quality plastic components.
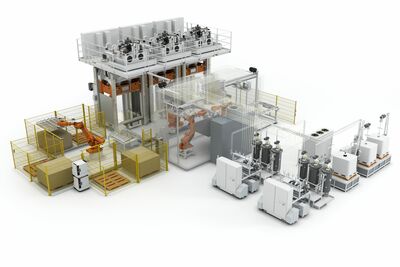
- For more than 1,000 employees at 15 production and sales locations in Europe, Asia and the Americas, High Tech and High Passion means acting as a dependable partner and making a contribution every day to the success of our customers. As a consequence, local customers benefit from the competence of the global FRIMO network.
- FRIMO equipment is used in many industries:
- Automobile | Rail | Construction | Equipment | Heating & Plumbing | Aviation
- Medicine | Furniture | Commercial Vehicles | Sports & Leisure | Household Appliances
- FRIMO is the global technology partner, supporting its customers in every step of the process from the idea through to series production:
- PUR processing | flexible cutting | punching | pressing, molding
- thermoforming | press lamination | edge folding | joining, gluing
Source
FRIMO, press release, 2022-05-03.
Supplier
CocoPallet
FRIMO Group GmbH
PHP Fibers GmbH
Share
Renewable Carbon News – Daily Newsletter
Subscribe to our daily email newsletter – the world's leading newsletter on renewable materials and chemicals