Visuals and PDF file in English available at: www.nova-institute.eu/press/?id=279
The custom-made bioreactor or ‘fermenter’, which was installed a year ago, looks impressive. The installation is equipped with steam, gas, compressed air piping, sensors, valves, sampling systems, etc. In short, it is equipped with all relevant peripheral equipment to be able to measure and control what is happening inside the reactor. This is where pure biochemistry takes place: gases such as CO2 and hydrogen, or oxygen, methane or syngas, are the raw materials of a fermentation process carried out by specialised bacteria. This results in products suitable for use in the chemical industry, where they provide an alternative to fossil chemicals from oil and natural gas.
The microbiological conversion takes place in the liquid phase, while the reagents are injected in a gaseous state. ‘The gases we use are typically poorly soluble, which makes the transfer from gas to liquid phase difficult,’ says Heleen De Wever, Project Manager Biotechnology at VITO and project coordinator of the EU-funded project BioRECO2VER. ‘As a result, the conversion by bacteria is also very slow. This is not only a technical problem but also an economic one because the fermentation of CO2 or other gaseous reagents has to be done efficiently enough to be deployed as a feasible climate-friendly alternative in the industry.’
Unique high-pressure fermenter
Therefore, the process engineers at VITO increase the pressure in the bioreactor, allowing the gases to dissolve more easily and speed up the fermentation process. In more traditional (glass) lab fermenters, the maximum pressure is severely limited. This is one of the reasons why VITO commissioned a unique high-pressure fermenter, based on a proprietary design. The funding was provided by the European project BioRECO2VER (www.bioreco2ver.eu).
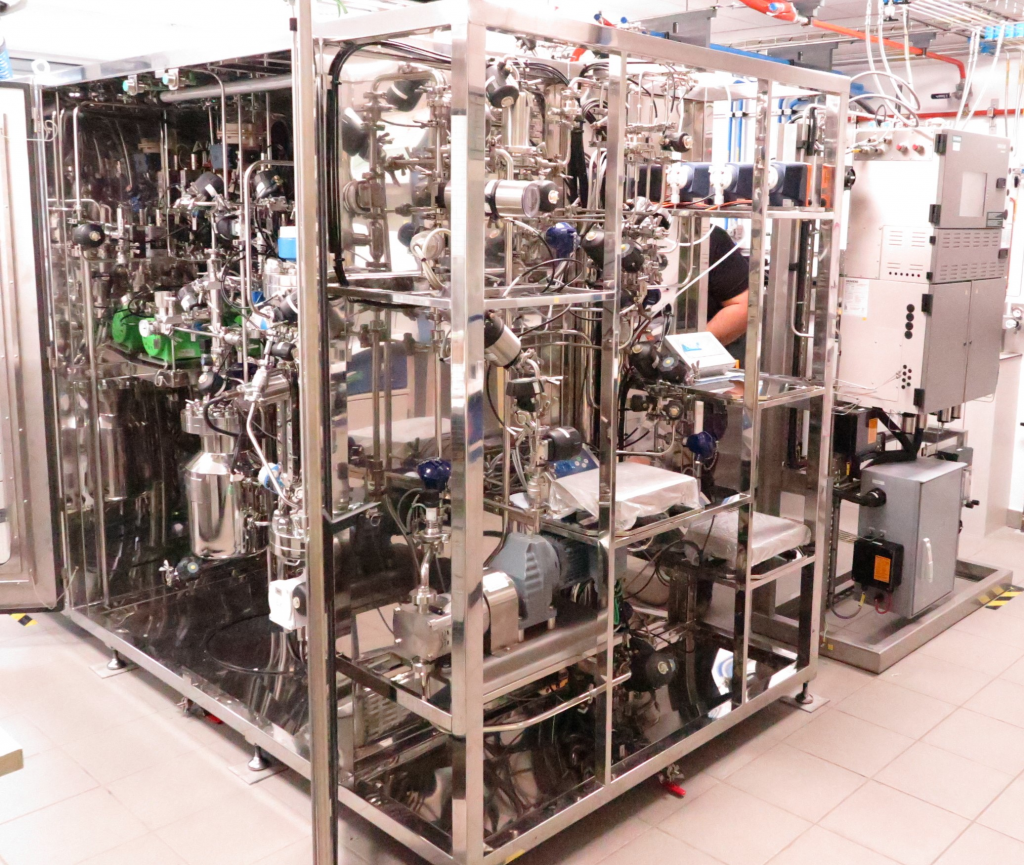
BioRECO2VER and VITO’s activities
In the European funded project BioRECO2VER, a consortium of twelve companies, research institutions and universities investigate the technical feasibility of energy-efficient and sustainable biochemical conversion of CO2 from industrial point sources like refineries and cement production plants into chemical building blocks, i.e., isobutene and lactate. To overcome several of the existing technical and economic barriers for CO2 conversion by industrial biotechnology, VITO focuses with the new installation on maximizing gas transfer in bioreactors and improving scalability.
Further, VITO can extensively research the influence of various parameters such as pressure, temperature and composition and dosage of the gas phase on fermentation. With an online gas chromatograph, samples of the gas phase can be analysed almost continuously, and the gas composition can then be adjusted immediately if required. Many other measurements are also performed online. ‘The maximum pressure in the bio-reactor is 10 bar, which allows an incredible flexibility in experimental conditions,’ says Wouter Van Hecke, researcher at VITO. ‘Hence, we can investigate the fermentation in a broad range of circumstances. We can also apply a wide variety of gas mixtures supplied by companies. Furthermore, the high-pressure fermenter has a membrane filtration unit to retain the micro-organisms in the reactor. This is important for speeding up the process and making it more efficient.’
VITO wants to gain a better understanding of the effect of pressure on fermentation. De Wever: ‘At the moment, gas fermentations are still too often characterised by low productivity and low product concentrations. By increasing the pressure and therefore the mass transfer from gas to liquid, we hope to improve these parameters. On the other hand, the pressure should not be too high either, as this may reduce the performance of the bacteria. ‘

High-tech research platform
The high-pressure fermenter is far beyond the lab scale. ‘It is a prototype that can address several research questions before scale-up to an industrial level,’ says Van Hecke. ‘Its size and complexity are well suited to answer fundamental questions: we study processes in detail and try to optimise them based on the gathered insights. To that end, we want to have as many online measurements and steering capabilities as possible.’
Pressure fermenters are logically more expensive to purchase than conventional fermenters. The trade-off between increased mass transfer and higher investment costs is one of the research questions that VITO wants to answer in the coming months and years.
VITO has a unique high-tech research platform from which other researchers and companies in Flanders (and beyond) can benefit. Companies with an ‘emission problem’ can approach VITO to see if and how their emitted gases can be valorised. ‘As part of the BioRECO2VER project, we are now mainly working with CO2 and hydrogen, but a wide range of production gases and processes can be investigated, whenever gas supply is a constraint for a particular conversion process,’ says De Wever. This could range from dosing oxygen to the conversion of methane or syngas. ‘We comply with all safety regulations, including ATEX certification for explosion safety.’
One of the industrial partners in the BioRECO2VER project is Arkema, a French producer of high-quality chemicals. ‘It is not sufficient to reduce our fossil energy consumption, we also need to look at strategies to consume CO2 in our processes. The major change which is happening is the availability of hydrogen (from electrolysis or pyrolysis which is not coproducing CO2) and carbon-free electricity. Microbial gas fermentation using the right combination of feedstocks and technologies can lead to molecules that are not accessible in a single step by chemical processes. It is then important to investigate the opportunities and challenges of this technology ‘, says Jean-Luc Dubois, Arkema’s Scientific Director.
The high-pressure installation is also interesting for companies that enlarge the assets of the micro-organisms by genetic research. ‘Ultimately, that’s where it begins: the type of bacteria determines which gases you can valorise, and which end product is ultimately produced,’ says Van Hecke. The VITO researchers are therefore eager to test new bacterial strains.
The here mentioned BioRECO2VER project has received funding from the European Union’s Horizon 2020 research and innovation programme under grant agreement No. 760431.
Supplier
Arkema
Flemish Institute for Technological Research (VITO)
nova-Institut GmbH
Share
Renewable Carbon News – Daily Newsletter
Subscribe to our daily email newsletter – the world's leading newsletter on renewable materials and chemicals