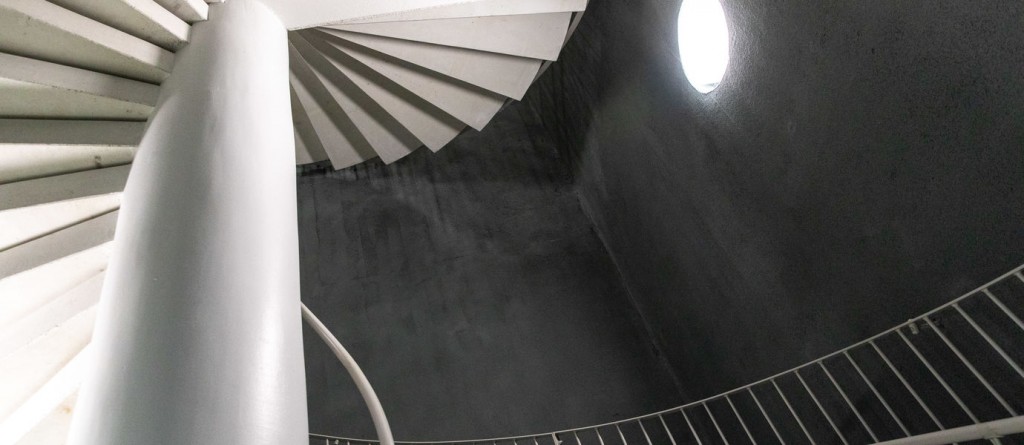
Good acoustics in the workspace improve work efficiency and productivity, which is one of the reasons why acoustic materials matter. The acoustic insulation market is already expected to hit 15 billion USD by 2022 as construction firms and industry pay more attention to sound environments. Researchers at Aalto University, in collaboration with Finnish acoustics company Lumir, have now studied how these common elements around us could become more eco-friendly, with the help of cellulose fibres.
‘Models for acoustic absorption are based on tests done with synthetic fibres, and natural fibres don’t adhere to these models. With natural fibres like cellulose, we can use thinner structures to achieve the same sound absorption as synthetic fibres,’ says Jose Cucharero, a doctoral student at Aalto University.
Cucharero’s research explores the effect of natural fibres’ properties on sound absorption and how these fibres can be used in room acoustics. Synthetic fibres, such as fibreglass and rockwool, are uniform in quality. Cellulose fibres have a complex structure with natural irregularities, which can be an asset for absorbing sound indoors. The origin of fibres also seems to matter: his research has found that hardwood fibres absorb sound better than softwood fibres. Based on the research, this can be attributed to the smaller dimensions of the hardwood fibres.
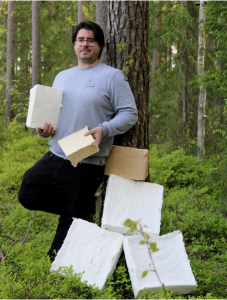
Cellulose fibres store carbon dioxide for decades
In addition to their excellent acoustic properties, cellulose fibres also have positive environmental impacts compared to traditional acoustic materials. The production of cellulose fibres is considerably more energy-efficient, and the fibres also absorb significant amounts of carbon dioxide from the atmosphere. Using the fibre in construction materials is an effective way to store carbon: buildings last for decades, unlike single-use packaging and paper where cellulose is typically used.
‘Acoustics solutions based on cellulose fibres can be applied to a wide range of facilities. For example, acoustic sprays — which can be used on any surface to create a porous, sound-absorbing layer — can significantly improve the comfort of buildings under renovation without changing their visual appearance,’ Cucharero says.
Research results are already used in product development
Alongside his doctoral dissertation, Jose Cucharero works at Lumir Oy, which produces acoustic solutions in line with the principles of the circular economy. The results of the dissertation are used in the development of new cellulose-based acoustics solutions, and the study has been rapidly applied in product development.
The commercial perspective is also complemented by tests that ensure the products’ scalable manufacturing and fire resistance. Based on the results, an industrially scalable process has been developed for the production of acoustic panels based on cellulose fibres.
‘Governments around the world have set out to become carbon neutral. We can’t achieve this by simply reducing emissions; we need to also absorb carbon dioxide from the atmosphere and store it in products.’ , says Lumir’s R&D Director Tuomas Hänninen, Doctor of Technology and Jose Cucharero’s thesis advisor.
Publications
https://link.springer.com/article/10.1007/s10570-021-03774-1
https://www.frontiersin.org/articles/10.3389/fbuil.2021.665332
Contacts
Doctoral candidate Jose Cucharero
tel. +358 (0)44 238 4576
email: jose.cuchareromoya@aalto.fi
Lumir Oy
Professor Tapio Lokki
tel. +358 (0)40 578 2486
email: tapio.lokki@aalto.fi
Aalto University School of Electrical Engineering
Department of Signal Processing and Acoustics
Source
Aalto University, press release, 2021-05-26.
Supplier
Share
Renewable Carbon News – Daily Newsletter
Subscribe to our daily email newsletter – the world's leading newsletter on renewable materials and chemicals