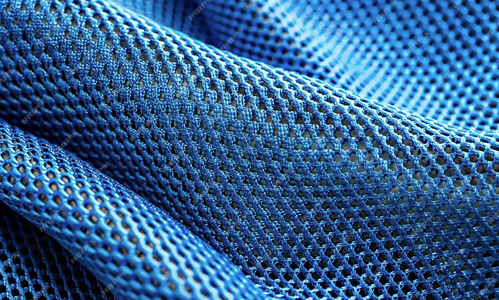
Nylons are a family of synthetic polyamides, often spun into fibres and used as textiles. First produced in the 1930s by DuPont, nylon is now produced on a global scale of around 6 million tonnes a year – significantly less common than polyester which is also used as a synthetic textile – but widely used as a performance material. Nylon fibres are used in the production of waterproof coats and tents. As a film, nylon is also used as food packaging, and as a rigid plastic it is widely used in the production of car parts.
Materials such as Kevlar are also examples of polyamides, more specifically an aromatic polyamide – though not necessarily considered nylon. Aromatic polyamide fibres (sometimes referred to as aramid fibres) are widely used in aerospace and military applications.
Polyamides are simply long chain molecules, made up of repeating units joined by an amide bond. Proteins like silk and wool are examples of natural polyamides. Synthetic polyamides are also commonly referred to as nylon.
Nylon
Nylons are a family of synthetic polyamides, often spun into fibres and used as textiles. First produced in the 1930s by DuPont, nylon is now produced on a global scale of around 6 million tonnes a year – significantly less common than polyester which is also used as a synthetic textile – but widely used as a performance material. Nylon fibres are used in the production of waterproof coats and tents. As a film, nylon is also used as food packaging, and as a rigid plastic it is widely used in the production of car parts.
Materials such as Kevlar are also examples of polyamides, more specifically an aromatic polyamide – though not necessarily considered nylon. Aromatic polyamide fibres (sometimes referred to as aramid fibres) are widely used in aerospace and military applications.
Aliphatic polyamides are named according to their monomers. For example, PA66 is named so because it is a polyamide derived from 2 monomers, both with a carbon chain of 6. PA66, or nylon 6,6 is produced from the condensation reaction of adipic acid and the hexamethylene diamine (Figure 1). Condensation reactions can alternatively just use an aminocarboxylic acid, instead of both a diamine and a dicarboxylic acid. Polyamides can also be produced by ring-opening polycondensation of lactams. PA6 is made from the ring-opening of caprolactam.
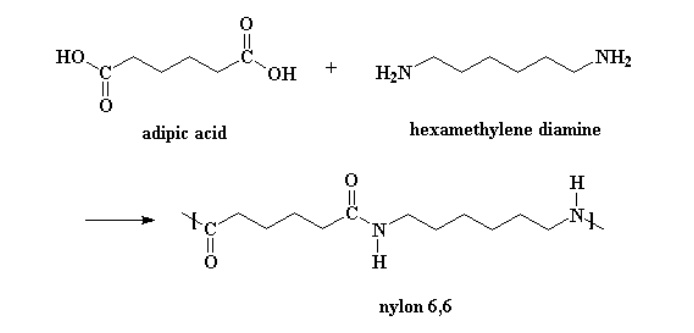
Current biobased polyamide market
Unlike many biobased polymers, biobased polyamides have been produced commercially for many years, with castor oil being the main feedstock. Castor oil contains a mixture of different fatty acids, but the main one is ricinoleic acid. Treating ricinoleic acid with alkali cleaves the carbon chain into two shorter chain molecules, one of them being sebacic acid, a 10-carbon chain carboxylic acid. Sebacic acid is mostly used in the production of polyamides, either as a dicarboxylic acid monomer or as a precursor to a diamine monomer.
Ricinoleic acid can also be cleaved into a 7- and 11-carbon chain, the latter being undecanoic acid. Further processing produces the aminocarboxylic acid, aminoundecanoic acid. The French speciality materials company Arkema, have been making biobased polyamides from castor oil for decades. They make PA11, named Rilsan, which is made using amino and ecanoic acid.
Other examples include Ecopaxx from Envalior which is a joint venture between DSM and Lanxess. Ecopaxx is a PA410 – a 72% biobased polyamide also derived from castor oil. Evonik also make a PA610 which is 62% biobased, and PA1010 which is 100% biobased, marketed as Vestamid terra and derived wholly or partially from castor oil.
The graph below (Figure 2) shows how some of these examples of commercial polyamides are derived from ricinoleic acid from castor oil.
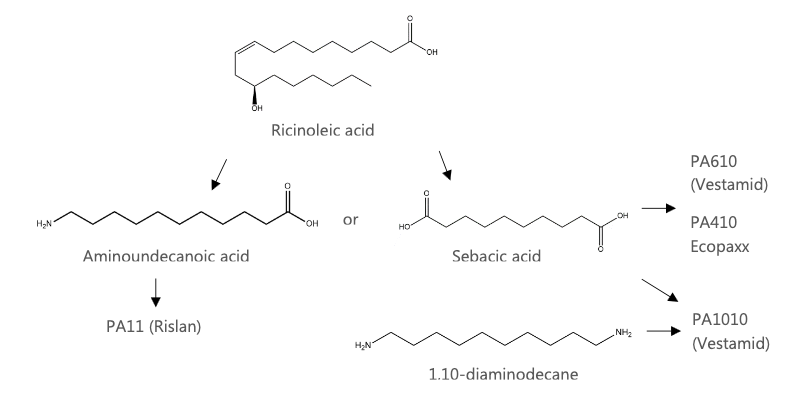
A more recent approach to biobased polyamides is to use monomers produced through the fermentation of sugars. Chinese biotechnology company Cathay Biotech, produce polyamides Terryl and Ecopent – a textile and engineering polyamide respectively, both based on 1,5-pentanediamine, also called cadaverine. Cathay commercially produce cadaverine, as does the Japanese chemical company, Toray. Also using fermentation to produce cadaverine, BioAmni is a partially biobased PA56 made by the chemical company Solvay. Similarly, Dutch company DSM use the C4 diamine putrescene, in conjunction with adipic acid, to make a PA46 with the trade name Stanyl.
In another recent development, Genomatia have taken a different approach to biobased polyamides by adopting the use of lactams. Their technology uses biobased caprolactam produced via fermentation of sugars, as the precursor to PA6. Genomatica’s technology is being taken to the market by sportswear brand Lululemon and is a good example of consumer demand for biobased plastics and uptake of biobased polyamides.
Biobased diamine development
The polymerisation step isn’t necessarily the hard part of producing biobased polymers. The barrier to further uptake is the production of biobased monomers. Looking at the monomers used to produce polyamides, diamines are of particular interest and a number of novel routes to biobased diamines are being pursued.
Shorter chain aliphatic
Using microbial fermentation and biotechnology is a promising method to produce the short-chain aliphatic diamines. Indeed, this is commercially successful for the aliphatic C5 diamine cadaverine. Several biobased synthesis processes have been developed for cadaverine but commercial production is based on the amino acid lysine, derived from sugar fermentation. Over the last few years, research has focussed more on optimising production of the C4 and C5 diamines with both E.coli and C. glutamicum having been engineered for diamine production.
There’s also research into alternative carbon sources, particularly for cadaverine, to decrease production costs and use under-utilised feedstocks. For example, lignocellulosic materials which produce xylose, as an alternative to glucose. Methanol has also attracted interest as readily available starting materials for novel fermentation of diamines.
The C3 and C6 diamines are widely used petrochemicals in high industrial demand but biosynthesis is more challenging. 1,3-diaminopropane is used to produce expoxy resins, and 1,6-diaminohexane is one of the precursors to PA66. Biobased 1,6-diaminohexane is not yet commercially produced, but Genomatica are currently developing routes. Chemical conversion is being researched with an interest in biobased hydroxymethylfurfural (HMF) as a feedstock – a relatively new to the market biobased feedstock.
Longer chain aliphatic
Synthetic routes for other biobased diamines are developing as using biotechnology for longer chain diamines is more challenging. There has been microbial production of 1,8-diaminoctane, 1,10- diaminodecane, and 1,12-diaminododecane from their corresponding diols in literature but direct fermentation of renewable sources to the diamines has not yet been reported.
Aromatic diamines
Biobased production of aromatic diamines is not industrial or in development and they are largely less studied than aliphatic diamines, but where production is being researched it is by chemical conversion and not microbial production. There is academic interest in their production from lignin and cashew nut shell, as typical sources of aromatic compounds. From lignin, aromatic diamines are derived from vanillin and from cashew nut shell, derived from cardanol. There are also examples of synthesis of aromatic diamines from terpenoids, derived from pine.
Summary
Biobased polyamides have been established for many years. This started with Arkema and PA11 but the market has expanded there are now multiple examples of polyamides from castor oil. There are also polyamides with shorter chain monomers in the market such as cadaverine, produced from fermentation. In development are more novel approaches, such as using lactams. Biotechnology and chemical conversion of new platform molecules are also being explored, but research into longer-chain aliphatic and aromatic diamines is limited. As further research into alternative monomers like diamines continues, biobased polyamide production can diversify and see potential in new markets and applications.
Author
Polly-Ann Hanson
Source
NNFCC, press release, 2024-10-03.
Supplier
Arkema
Cathay Biotech
DSM
Envalior
Evonik Industries AG
Geno (formerly Genomatica, Inc.)
Lanxess AG
lululemon athletica
NNFCC
Solvay
Toray Industries Inc.
Share
Renewable Carbon News – Daily Newsletter
Subscribe to our daily email newsletter – the world's leading newsletter on renewable materials and chemicals