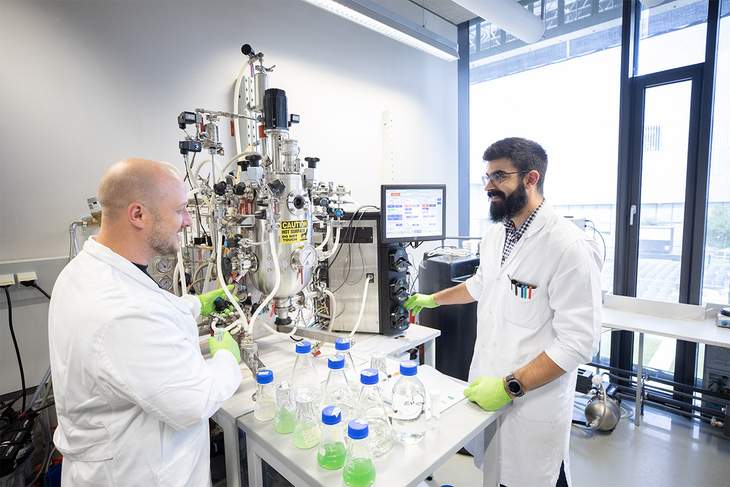
Joint research by BOKU Tulln and IMC University of Applied Sciences Krems shows great potential in the recovery of valuable materials from electronic waste. Up to 85% recovery of rare earths achieved in the laboratory.
A research collaboration between BOKU Tulln and IMC University of Applied Sciences Krems is using the further development of bioleaching and bioaccumulation to develop a two-stage, environmentally friendly and sustainable process for recovering rare earths. In the bioaccumulation step, metal recovery rates of up to 85% were achieved from electronic scrap. The key to success lies in the combination of biotechnological processes. The promising foundations for these methods, which are currently under development, were recently published in the renowned journal Frontiers in Microbiology.
The sharp rise in demand for electronics in recent years, used in a wide range of electronic devices such as mobile phones, electric vehicles and computers, has led to an increase in waste containing rare earths. Most of this waste still ends up in landfills unused, despite the fact that rare earths are an important source of raw materials and have even been classified as critical raw materials by the EU. For this reason, intensive research is being carried out into efficient methods of recovery. Compared to other methods, the microbiology-based methods of bioleaching and bioaccumulation represent a promising ‘green’ alternative technology for recovering critical raw materials from electronic waste. It is cost effective, does not produce hazardous or polluting secondary waste and uses less energy.
The basic principles of the processes are based on the production of acids by certain microorganisms that can ‘leach’ certain metals such as iron, copper or aluminium from the electronic waste. These metals interfere with the absorption process of the valuable rare earths in the subsequent bioaccumulation. Both methods have been researched for some time by the two partners, BOKU Tulln and IMC University of Applied Sciences Krems, and the research teams have now joined forces in a promising collaboration and combined their expertise.
“Nothing comes from nothing”: training for microbes
In addition to the researchers, the current study involved a number of other key players in the bioleaching process, which is summarised in the joint technology: Bacteria of different species. For example, Acidithiobacillus thiooxidans and Alicyclobacillus disulfidooxidans, which were originally collected from an acidic mining lake (pH 2.6) in the Czech Republic and then grown together in the laboratory, were used in the bioleaching process. These acidophilic and chemolithotrophic organisms thrive in acidic environments and derive their energy from the oxidation of inorganic compounds. In terms of bioaccumulation, Escherichia coli, the well-known intestinal bacterium, proved to be the most successful accumulator of rare earths.
The main practical challenge for the enrichment process used to recover rare earths is the high content of other metals typically found in e-waste. In particular, iron, copper and aluminium interfere with the biotechnological process. To overcome this problem, the researchers came up with another innovative option: “training” the microbes. Using a device called a morbidostat developed at IST-Klosterneuburg, the organisms are gradually accustomed to higher metal concentrations. However, the bioaccumulation process has to be carried out carefully so that the organisms do not lose their ability to accumulate the valuable substances.
Efficiency in stages
The methods currently used to extract rare earths are based on chemical processes, which are associated with the formation of environmentally harmful by-products and the creation of new problematic substances. A combination of biotechnological methods has clear advantages over chemical methods, as both the leaching and the accumulation in the cells of the bacteria are environmentally friendly and sustainable, and no hazardous or polluting substances are produced at any stage of the process. However, further research is needed to overcome the wide variation in the composition of e-waste. Even if the concentration of interfering metals such as aluminium, iron or copper is changed, the technology must work in such a way that the results are reproducible and reliable. The researchers at BOKU and IMC Krems are pursuing several strategies to achieve this.
Another strategy is to acclimate the bacteria responsible for bioleaching and bioaccumulation to high concentrations of interfering metals. This is made possible by using a system called morbidostat. In this system, the micro-organisms are exposed to a gradually increasing concentration of interfering metals and then waited until acculturation occurs and the organisms start to grow further.
Together with the conditioning of the microorganisms, systems are being tested that can trigger a reduction in the concentration of interfering metals. The materials being investigated include the so-called lignin hydrogels developed at BOKU.
The combination of these strategies aims to ensure the efficiency and sustainability of the innovative combination of bioleaching and bioaccumulation in order to develop a new, environmentally friendly method for recycling scarce rare earths.
Source
IMC University of Applied Sciences Krems, press release, 2024-06-10.
Supplier
IMC University of Applied Sciences Krems
University of Natural Resources and Life Sciences (BOKU)
Share
Renewable Carbon News – Daily Newsletter
Subscribe to our daily email newsletter – the world's leading newsletter on renewable materials and chemicals